Exploring Vancomycin Production: Processes and Quality
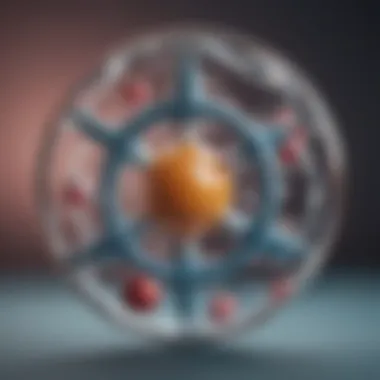
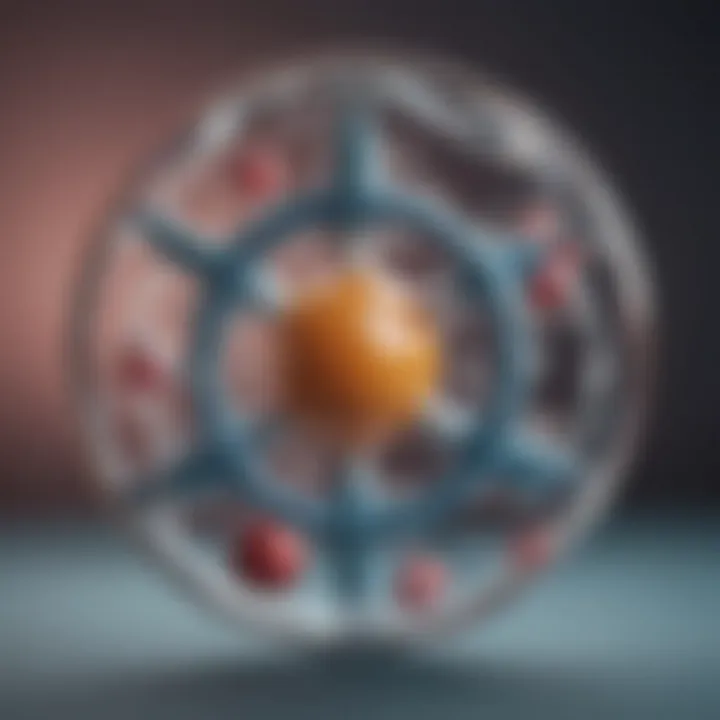
Intro
Vancomycin is often hailed as a cornerstone in the fight against serious bacterial infections, especially those caused by resistant strains like MRSA. With the increasing complexity of microbial resistance, understanding the manufacturing landscape of vancomycin has become more critical than ever. The process is not only about creating an effective antibiotic; it also involves rigorous quality control, which is essential for patient safety and treatment effectiveness.
In this article, we will navigate through the nuances of vancomycin production. From the variety of manufacturing processes used by key players in the industry to the quality assurance measures that ensure efficacy and safety, we will touch on every crucial aspect. Furthermore, we will explore how advancements in technology and evolving regulatory requirements impact the antibiotic supply chain. This comprehensive guide aims to demystify the complexities surrounding vancomycin manufacturing, offering valuable insights for students, researchers, educators, and professionals alike.
Research Overview
Summary of Key Findings
The manufacturing of vancomycin involves several intricate steps, reflecting a balance between efficiency and the stringent demands of quality assurance. Key findings from recent inquiries into this field highlight:
- The prevalence of different fermentation techniques and their respective yields.
- Challenges posed by raw material sourcing, particularly in ensuring microbial quality and consistency.
- Innovations in purification methods that enhance overall production metrics.
- The necessity for compliance with international regulatory agencies like the FDA and EMA, which set the standards for antibiotic manufacturing.
Methodologies Employed
A thorough examination of vancomycin's production involves various methodologies, largely centered around qualitative and quantitative analyses:
- Case studies on manufacturers: Analyzing production processes of significant players like Teva Pharmaceutical Industries and Eli Lilly offers an in-depth look at diverse practices.
- Laboratory evaluations: Conducting tests to compare potency and purity yields under different processing conditions helps clarify best practices in manufacturing.
- Regulatory compliance audits: Reviews of companies' adherence to guidelines from health authorities provide insights into the importance of maintaining high quality standards.
In-Depth Analysis
Detailed Examination of Results
The results of recent studies indicate that the fermentation methodology plays a pivotal role in determining both the quality and yield of vancomycin. Solid-state fermentation (SSF), although traditionally less common, has shown promise in enhancing the production rates of secondary metabolites. The efficiency metrics indicate that companies utilizing SSF can see up to a 30% increase in yields compared to conventional submerged fermentation methods.
Furthermore, advancements in chromatography techniques, especially high-performance liquid chromatography (HPLC), have become critical. These innovations allow manufacturers to achieve higher purity levels, a fundamental requirement given the scrutiny on antibiotic efficacy.
Comparison with Previous Studies
When juxtaposed with prior research studies, the advancements in technology and methodology become evident. Earlier studies primarily focused on classic fermentation techniques, whereas modern research embraces a more integrated approach, combining both biological and chemical engineering principles.
Moreover, many past investigations lacked a thorough evaluation of regulatory environments. In contrast, recent findings underscore the necessity of aligning production practices with evolving regulations, highlighting how companies now prioritize compliance as a core aspect of their operational strategies.
"The evolution of antibiotic manufacturing practices not only reflects technological progress but also embodies the industry's response to global health challenges."
By focusing on these elements, we open avenues for a thorough understanding of the complexities inherent in antibiotic production, which stands at the forefront of medical science today.
Prologue to Vancomycin
Vancomycin stands as a cornerstone in the pharmacological arsenal against serious bacterial infections, specifically those caused by Gram-positive organisms. Its significance is underscored by its ability to combat resistant strains of bacteria, particularly methicillin-resistant Staphylococcus aureus (MRSA). With the rise of antibiotic resistance, the need for reliable access to effective antibiotics has never been more pressing. Vancomycin not only treats infections but also plays a crucial role in preventing surgical site infections, translating its importance from labs to actual patient care.
The development and manufacturing of vancomycin require a nuanced appreciation of its history and its chemical intricacies. This article seeks to illuminate the many facets involved in vancomycin production, from initial precursor generation, through fermentation techniques, to the purification methods that ensure its efficacy and safety.
Historical Development of Vancomycin
Discovered in 1953, vancomycin emerged from the soil of a remote Philippine island, specifically from a bacterium named Amycolatopsis orientalis. The initial use of vancomycin was limited due to its route of administration—primarily via intravenous injection. During the 1970s, it became widely adopted, especially as a last-resort treatment for patients who exhibited resistance to other antibiotics.
The drug was a game-changer—prescribing it allowed healthcare professionals to tackle infections that had previously deemed untreatable. However, with the widespread use of vancomycin came the rise of vancomycin-resistant enterococci (VRE), underscoring the need for ongoing vigilance in antibiotic stewardship. The history of vancomycin is a textbook example of the double-edged sword of antibiotic use: the more we utilize powerful agents, the quicker resistance can develop.
Chemical Properties and Mechanism of Action
Vancomycin is a glycopeptide antibiotic, featuring a complex structure composed of a cyclic heptapeptide with various substituent groups. This intricate makeup grants it the ability to bind specifically to the D-alanyl-D-alanine terminus of cell wall precursor units, inhibiting cell wall synthesis of susceptible bacteria.
The mechanism by which vancomycin operates makes it particularly effective against Gram-positive bacteria. By blocking cell wall construction, it weakens the bacterial cells, causing lysis and eventual death.
- Solubility: Vancomycin is moderately soluble in water, which affects its formulations and delivery methods.
- Stability: It is stable under a range of conditions, making it valuable in the manufacturing process as it retains efficacy over time.
- Spectrum of Activity: Primarily active against Gram-positive bacteria, vancomycin also exhibits limited activity against some Gram-negative organisms, but its main role is in treating infections caused by resistant strains.
The complexity of its mechanism of action underscores the necessity of rigorous manufacturing processes to ensure the purity and potency of vancomycin. This understanding of its chemical properties provides a framework for the subsequent discussions on the manufacturing processes and quality control measures essential for producing this vital antibiotic.
The Manufacturing Process of Vancomycin
The manufacturing process of vancomycin is a crucial element in ensuring the availability and effectiveness of this life-saving antibiotic. Understanding the intricacies involved provides insight into not only how this drug is produced but also the challenges faced by manufacturers in adhering to high standards of quality and efficiency. The entire process consists of distinct stages: precursor generation, fermentation techniques, and purification methods. Each step is laden with significant intricacies that require meticulous control and optimization. This section will examine these components, illuminating their implications for the wider pharmaceutical landscape and the ongoing fight against antibiotic resistance.
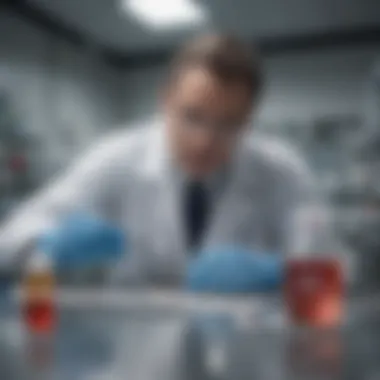
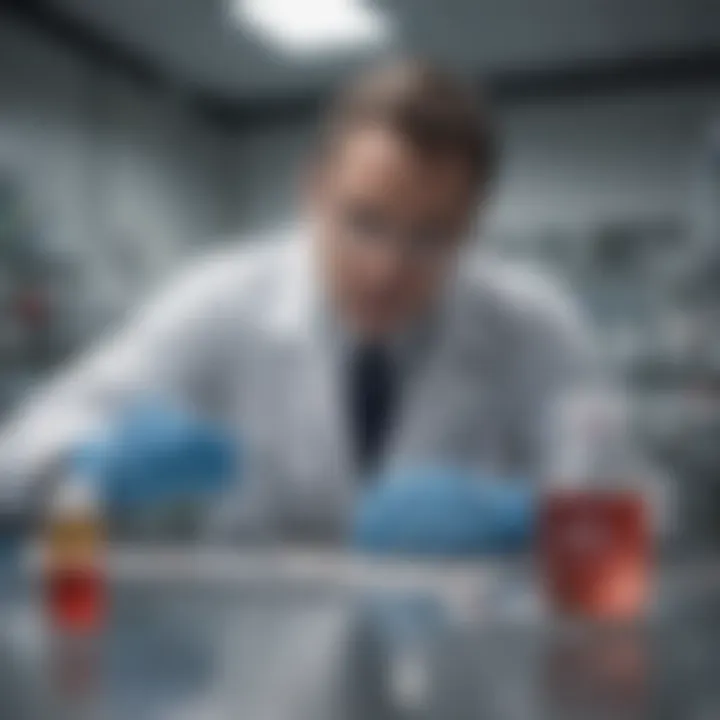
Precursor Generation
The journey of vancomycin begins with precursor generation, which is pivotal for its eventual biosynthesis. Precursors are the raw materials from which vancomycin is derived, and their quality directly impacts the final product. Typical precursors include sugars and amino acids, which are assembled through various pathways to create the necessary building blocks for vancomycin.
Producing high-quality precursors requires not only careful selection of raw materials but also advanced methodologies. For instance, carbohydrate fermentation is often favored due to its efficiency in yielding high amounts of glucose, a critical component. The materials are typically sourced from agricultural produce, ensuring sustainability and cost-effectiveness.
"The production of precursors is like laying the foundation of a house; without solid groundwork, the structure is bound to crumble."
Fermentation Techniques
Once the precursors are generated, they undergo fermentation—a critical phase that effectively transforms these materials into vancomycin. Different microorganisms, mostly Amycolatopsis orientalis, are utilized in fermentation. This choice of organism is not arbitrary; its genetic make-up has been optimized over years to maximize yield and minimize by-products. The fermentation process itself is monitored closely, including temperature, pH levels, and nutrient supply, to ensure optimal conditions for microbial growth.
Fermentation can take place in batch or continuous systems. Batch systems are often simpler and more cost-effective for smaller production volumes, while continuous systems can provide greater output and consistency for larger-scale operations. The fermentation process can last several days, during which the microorganisms convert the precursors into vancomycin, releasing it into the culture fluid.
Purification Methods
The final stage of vancomycin manufacturing pertains to purification, a complex but essential process that assures the drug's safety and effectiveness. After fermentation, the broth containing vancomycin must be cleaned to remove impurities, by-products, and residual microbial material.
Several techniques are employed in this purification phase, including solvent extraction, chromatography, and crystallization. Each method serves a unique purpose, enhancing the overall quality of vancomycin. For instance, chromatography is especially effective in isolating vancomycin based on its chemical properties, while crystallization can yield pure vancomycin in solid form for subsequent processing.
This purification regime is governed by stringent regulatory standards to ensure that the final product is not only effective but also devoid of harmful contaminants. The meticulous approach to purification cannot be overstated, as it directly correlates with the safety profile of the antibiotic.
Key Manufacturers in Vancomycin Production
The landscape of vancomycin production is shaped significantly by its manufacturers. These industry players determine not just the scale of production but also the quality and availability of this essential antibiotic. Vancomycin is vital for treating severe bacterial infections, especially in cases of antibiotic resistance. Thus, understanding who produces it and how they operate provides valuable insight into the antibiotic supply chain. Moreover, the choices made by these manufacturers can have far-reaching implications for public health.
Leading Global Suppliers
Among the top manufacturers are some prominent names like Teva Pharmaceuticals, Sandoz, and Fresenius Kabi. These companies have established a strong global presence, producing substantial quantities of vancomycin to meet demand across various markets.
- Teva Pharmaceuticals is known for its wide-ranging portfolio, including generic medications and specialty pharmaceuticals. Their commitment to quality assurance in vancomycin production aligns with strict regulatory standards.
- Sandoz, a division of the Novartis group, focuses on providing high-quality generics and has invested in innovative production techniques to ensure consistent output and reliability in their vancomycin offerings.
- Fresenius Kabi has carved a niche in infusible medications and has developed its vancomycin formulation for intravenous use.
These manufacturers maintain high standards and collaborations, ensuring that supply chains are efficient and responsive to the fluctuating demands of healthcare providers.
Regional Players and Their Contributions
In addition to global giants, regional manufacturers also play a crucial role in vancomycin production. Companies like Aurobindo Pharma in India and Wockhardt have made notable contributions to the market.
Aurobindo Pharma, for instance, not only focuses on cost-effective production but also on target markets often overlooked by larger firms. Their facilities comply with international standards, addressing the need for affordable antibiotics in lower-income regions.
On the other hand, Wockhardt has made headlines by optimizing their production processes, which includes eco-friendly practices that reduce waste. Their efforts not only contribute to the economy but also promote sustainability in pharmaceutical manufacturing.
Generally, regional players help to diversify the production base, providing alternatives to larger manufacturers and contributing to competitive pricing.
Emerging Manufacturers in Developing Markets
New players are emerging in developing markets, enhancing the production capabilities of vancomycin. These include companies like Kusum Healthcare and Hindustan Antibiotics.
Kusum Healthcare has started to gain momentum in the local antibiotic scene, bridging the gap between affordability and quality. Their locale-based production minimizes import dependency and makes medications more accessible to local populations.
Similarly, Hindustan Antibiotics, one of the oldest pharmaceutical enterprises in India, is exploring advanced technologies to step up their production processes, working towards compliance with global regulatory standards.
These emerging companies signify a shift towards localized manufacturing, which could strengthen resilience in antibiotic supply chains worldwide, especially amid concerns of antibiotic resistance and global health emergencies.
"While the global players set the pace for production, regional and emerging manufacturers are crucial in making vancomycin accessible where it’s most needed."
Quality Control in Vancomycin Manufacturing
The importance of quality control in vancomycin manufacturing cannot be overstated. It serves as the backbone of production processes, ensuring that the antibiotic not only meets safety standards but also is effective for patients. Given vancomycin's critical role in treating severe bacterial infections, particularly those caused by resistant strains, maintaining high quality throughout its production is essential.
Quality control focuses on several specific elements that influence the process, including adherence to regulatory standards, rigorous testing methods, and robust quality assurance measures. These facets contribute to not just the product quality itself but also the overall reliability of the supply chain.
A well-established quality control framework mitigates risks, such as contamination or substandard efficacy, that could have far-reaching implications for patient health. Through various methodologies, manufacturers are able to ensure that their product can withstand the tests of time, evolves with emerging bacterial challenges, and adheres to the increasing scrutiny of regulatory bodies.
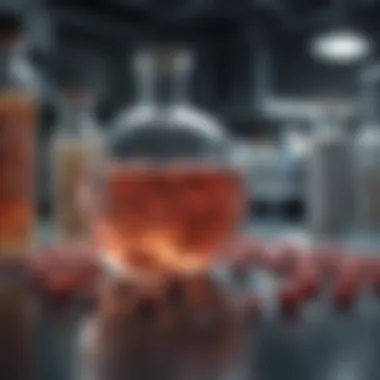
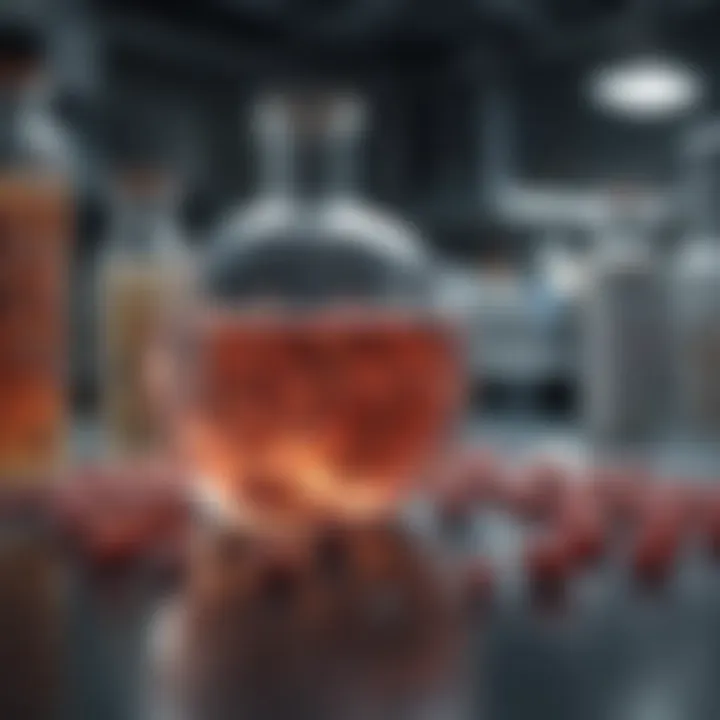
Regulatory Standards and Compliance
Navigating the regulatory landscape is a critical aspect for vancomycin manufacturers. Various organizations, including the Food and Drug Administration (FDA) in the United States and the European Medicines Agency (EMA) in Europe, have laid down stringent guidelines for antibiotic production. These not only dictate manufacturing practices but also set the bar for safety, quality, and efficacy.
Compliance with these standards is mandatory. Non-compliance can lead to recalls, legal ramifications, or worse, failure to deliver life-saving medicines to those in need. Key regulations include:
- Good Manufacturing Practices (GMP): These guidelines are foundational, defining the quality standards that must be upheld throughout the production process.
- Quality by Design (QbD): This proactive approach ensures that quality is inherently built into the product from the early stages of development through to production.
- Clinical Trial Guidelines: Before vancomycin reaches the market, it must pass through rigorous clinical trials to demonstrate its efficacy and safety profile.
By adhering to these regulations, manufacturers assure that their products are not just compliant but also competitive in the marketplace.
Testing Methods for Purity and Efficacy
Testing methods play a pivotal role in ensuring the purity and efficacy of vancomycin. Various techniques are used to ascertain that the final product is free from unwanted contaminants, meets its labeled potency, and is safe for clinical use. These methods include:
- High-Performance Liquid Chromatography (HPLC): Widely employed to analyze the chemical composition of vancomycin, HPLC can quantify active ingredients and detect impurities effectively.
- Mass Spectrometry (MS): This method offers high sensitivity, allowing for the detection of molecular structures and contaminants that may compromise drug safety.
- Microbiological Assays: Since vancomycin is an antibiotic, microbiological assays are critical. They help determine the minimum inhibitory concentration (MIC) needed to combat specific bacterial strains.
Deploying these testing methods ensures that any batch of vancomycin produced is not just adequate but of the highest quality, ready to safeguard health.
Traceability and Quality Assurance Measures
Traceability is another significant aspect that contributes to quality assurance in vancomycin manufacturing. This system tracks every component from raw materials to finished products, making it easier to identify and rectify problems when they occur. It also helps in understanding the entire supply chain, thus ensuring that all materials used in production meet predefined quality criteria.
Quality assurance measures include:
- Regular Audits: Scheduled audits add an extra layer of oversight, ensuring that processes are adhered to and any deviations are quickly addressed.
- Documentation Practices: Maintaining rigorous documentation of production processes helps in audits and recalls, providing a comprehensive trail of the product's lifecycle.
- Training Programs: Implementing continuous training for staff involved in vancomycin manufacturing ensures that they are updated on best practices and regulatory requirements.
By integrating traceability and stringent quality assurance measures, manufacturers not only comply with regulatory expectations but also enhance their credibility in a market that demands accountability and quality.
The Role of Technology in Vancomycin Production
The integration of advanced technology in the production of vancomycin represents a seismic shift in how antibiotics are manufactured. With the escalating threat of antibiotic resistance, the need for efficient and robust production methods has never been more pressing. Technology acts as a catalyst for change, driving innovation and enhancing quality control throughout the manufacturing process. The deployment of state-of-the-art techniques provides manufacturers with the ability to streamline operations, reduce costs, and maintain compliance with regulatory standards. Moreover, technology significantly impacts product quality and the overall supply chain, making it essential to dissect its role thoroughly.
Advancements in Biotechnological Approaches
Recent years have witnessed remarkable progress in biotechnological innovations aimed at improving the efficiency of vancomycin production. One area of focus has been metabolic engineering, where researchers manipulate the metabolic pathways of microorganisms to increase yield.
- Gene Editing: Techniques like CRISPR-Cas9 have enabled precise edits to enhance microbial strains, granting them the capacity to produce vancomycin more effectively.
- Synthetic Biology: This emerging field combines biology and engineering principles to design and construct new biological parts. Such innovations allow for the creation of microorganisms that can produce antibiotics in a more efficient and sustainable manner.
- Fermentation Optimization: Enhanced fermentation techniques are now being utilized to improve product yield. These methods can modify pH levels, temperature control, and nutrient feed strategies to foster an ideal environment for bacteria to thrive and produce vancomycin.
"The application of advanced biotechnological approaches is not only about quantity but also about improving the quality of the end product."
Automation and Process Optimization
Automation has become an integral part of modern vancomycin production processes. The implementation of automated systems touches on various stages of manufacturing, ensuring that production is consistent and efficient.
- Continuous Manufacturing: This innovative method allows for an uninterrupted flow of materials, streamlining production timelines while minimizing waste.
- Robotic Systems: Employing robots in laboratory settings boosts efficacy in handling substances, reducing human error and enhancing safety protocols.
- Real-Time Monitoring: The use of sensors and automated data logging aids in the closer monitoring of production parameters. This ensures compliance in real-time, addressing any deviations immediately before they result in significant quality issues.
Data Analytics in Supply Chain Management
With the increasing complexity of vancomycin production, leveraging data analytics in supply chain management is paramount. Effective data management strategies not only improve individual stages of production but can lead to improved decision-making throughout the manufacturing process.
- Predictive Analytics: By analyzing consumer demand and historical data, manufacturers can forecast future needs more accurately, facilitating better resource allocation and inventory management.
- Risk Assessment: Advanced data analytics can help identify potential risks in the supply chain such as supply disruptions or regulatory challenges. This enables proactive measures to mitigate those risks, ensuring a more stable production environment.
- Quality Improvement: Collecting and analyzing data related to product quality allows for continuous improvement initiatives. Monitoring quality in the supply chain enables manufacturers to respond effectively to any quality concerns, maintaining a high standard for product efficacy.
In sum, the role of technology in vancomycin production cannot be overstated. From advancements in biotechnology to the automation of processes and savvy data analytics, these elements converge to enhance not only the efficiency of production but also the integrity of the final product. This technological revolution is paving the way for a more dependable, safe, and resilient antibiotic supply chain.
Challenges Facing Vancomycin Manufacturers
The world of vancomycin manufacturing is fraught with challenges that not only test the resilience of companies but also affect the entire healthcare landscape. Addressing these obstacles is crucial for producing effective antibiotics and ensuring a steady supply in the face of growing antimicrobial resistance. Manufacturers must keep their fingers on the pulse of various issues, including supply chain disruptions, antibiotic resistance, and regulatory hurdles. Each of these factors plays a significant role in shaping production strategies and ultimately impacts patient care.
Supply Chain Disruptions
Supply chain disruptions can significantly hinder the manufacturing of vancomycin. Whether due to global events, such as pandemics, natural disasters, or even geopolitical tensions, the flow of essential raw materials is often disrupted. For instance, interruptions in the supply of specialized chemicals or fermentation nutrients can delay production schedules or compromise quality.
- Example of disruption: A sudden lockout in a key manufacturing location can halt the entire supply chain. If a critical country faces instability, it can create a ripple effect that reaches manufacturers worldwide, reducing the availability of raw materials needed for antibiotic production.
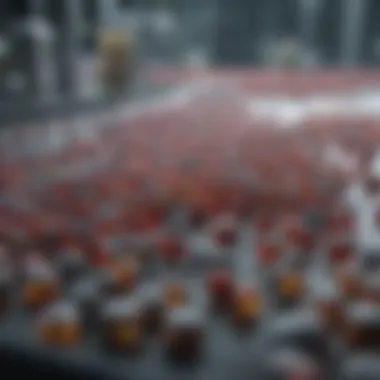
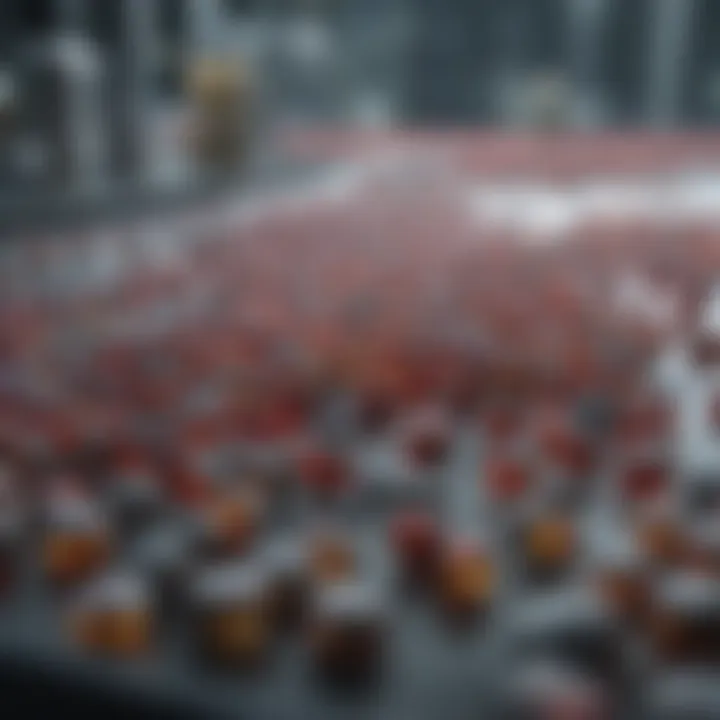
This underscores the need for strategic planning and diversification. Manufacturers are increasingly looking to establish a more resilient supply chain by sourcing raw materials from various geographical locations. Furthermore, investing in strong relationships with suppliers can ensure better communication and responsiveness in challenging times.
Antibiotic Resistance Issues
Antibiotic resistance looms as a significant concern for vancomycin manufacturers and public health. With the increasing prevalence of resistant strains of bacteria, particularly among healthcare-associated infections, the efficacy of vancomycin is under siege. In addition, the emergence of new resistance mechanisms means that manufacturers must remain ahead of the curve.
- Accommodation for advancements: Companies are therefore pressured not just to maintain the current production of the antibiotic but also to invest in research to develop new formulations or alternative therapies. This may involve spending resources on studies to enhance vancomycin's effectiveness against resistant strains, which can be a daunting task with no guaranteed outcomes.
By focusing on innovation and adapting to emerging resistance patterns, manufacturers can play a critical role in combating the threat of resistance while ensuring the viability of their products in the market.
Regulatory Hurdles
The stringent regulatory framework governing pharmaceutical production adds another layer of complexity to vancomycin manufacturing. Compliance with regulations laid down by authorities such as the FDA or EMA can be resource-intensive and challenging. Manufacturers must not only adhere to rigorous testing and production standards but also navigate the multilayered approval processes that can delay bringing a product to market.
- Implications of delays: Each delay can translate into lost revenues, which may push smaller manufacturers to the brink of financial instability. More significant players may absorb such shocks better, but they too face consequences when it comes to upholding their market position.
In this environment, staying abreast of changing regulations and investing in quality control systems is paramount. Manufacturers should seek continuous improvement and incorporate best practices into their processes to ensure compliance without compromising production speed.
"Adaptability in the face of challenges is what differentiates successful manufacturers from those who falter under pressure."
In summary, the interplay among supply chain disruptions, antibiotic resistance, and regulatory hurdles exemplifies the intricate challenges vancomycin manufacturers face. Their ability to adapt and innovate in response to these issues is essential in navigating the ever-evolving landscape of antibiotic production.
Future Perspectives in Vancomycin Production
The future perspectives of vancomycin production invite examination not just of the existing processes but also of the innovations on the horizon that could revolutionize manufacturing. In light of the rising global concern regarding antibiotic resistance, advancements in production methods serve not only the pharmaceutical industry but also the broader healthcare landscape. As we delve into sustainable practices and collaborations within research, we unveil the pathway forward that leverages innovative technologies while promoting responsible antibiotic use.
Sustainability in Antibiotic Manufacturing
The conversation surrounding sustainability in antibiotic manufacturing is more relevant than ever. Traditional methods of antibiotic production often come with significant environmental costs, such as high energy use and harmful by-products. Finding solutions that prioritize ecological balance is essential.
Key considerations include:
- Utilizing Renewable Resources: Transitioning from non-renewable to renewable feedstocks can dramatically reduce the carbon footprint associated with production.
- Waste Minimization: Implementing processes that minimize waste not only helps the environment but also enhances overall efficiency. Technologies that recycle by-products can lead to cost savings and improved profitability.
- Green Chemistry Approaches: Adopting green chemistry principles in the production of vancomycin can lead to safer and more environmentally friendly manufacturing practices. This includes using non-toxic solvents and reagents that meet stringent environmental regulations.
Researchers continue to explore various pathways to integrate sustainability in antibiotic manufacturing, thus aligning with global commitments to protect the environment.
Innovations on the Horizon
In the realm of vancomycin production, a slew of innovative methods stands poised to redefine processes. With technological advancements emerging at an unprecedented pace, manufacturers must stay ahead of the curve to ensure that they can meet the future healthcare demands effectively.
- Biotechnological Advances: The application of synthetic biology enables the redesigning of bacterial pathways to enhance vancomycin yield. This genetic manipulation can improve efficiency and reduce production costs.
- Continuous Manufacturing Techniques: Shifting from batch processing to continuous production systems can streamline operations, reduce downtime, and cut costs, allowing companies to respond swiftly to market demands.
- AI and Machine Learning: Employing data analytics and algorithms to optimize fermentation conditions can lead to significantly higher yields and quicker turnaround times in production cycles.
These innovations are not mere enhancements; they signify a shift toward a more agile and responsive production landscape.
Collaborations and Partnerships in Research
It's clear that overcoming the challenges in vancomycin production necessitates a collective approach. Collaborations across various sectors play a pivotal role in leveraging knowledge and resources efficiently. By fostering partnerships, stakeholders can accelerate research and development in antibiotic production.
- Public-Private Partnerships: Collaborations between governments and pharmaceutical companies can lead to shared benefits in research funding, reinvigorating the antibiotic pipeline.
- Academic and Industry Ties: Engaging universities in research can lead to cutting-edge discoveries and innovations that benefit manufacturing processes.
- Global Collaboration: As antibiotic resistance knows no borders, international partnerships can facilitate knowledge transfer, ensuring that best practices in production are shared and implemented worldwide.
"In the fight against antibiotic resistance, collaboration and innovation are not just advantageous—they are imperative for the continued effectiveness of antibiotics like vancomycin."
The future of vancomycin production will require a multifaceted approach that weaves together sustainability, cutting-edge innovations, and a cooperative spirit. By addressing these core elements, stakeholders in the antibiotic production ecosystem can not only meet the challenges of today but also prepare for those of tomorrow.
Closure: The Path Forward for Vancomycin Manufacturers
In the realm of pharmaceutical production, particularly in antibiotic manufacturing, the future for vancomycin manufacturers is a topic that deserves considerable attention. With rising instances of antibiotic resistance and the increasing demand for effective treatments, the responsibility to meet these health challenges has become more pressing than ever. A well-structured approach to evolving production processes, quality control measures, and innovative technologies is vital for staying ahead in the industry.
Strategic Recommendations
As the production landscape for vancomycin changes, manufacturers need to develop strategic approaches that not only enhance efficiency but also bolster overall efficacy. Here are some recommendations that may guide producers:
- Invest in Advanced Technology: Embrace cutting-edge technologies such as artificial intelligence and machine learning. These tools can facilitate the optimization of fermentation processes and quality control protocols, ultimately improving yields and reducing waste.
- Focus on Sustainability: Implementing green practices in manufacturing is critical. Utilizing biodegradable materials and reducing energy consumption are both environmentally and economically beneficial. This allows manufacturers to contribute positively to the planet while meeting regulatory requirements.
- Strengthen Partnerships: Forming alliances with research institutions can propel innovation. Engaging in collaborative research can aid in developing new formulations or processes that enhance the effectiveness of vancomycin against resistant strains.
- Remain Agile: Given the unpredictable nature of market demand and regulatory changes, maintaining flexibility in production capabilities is essential. Manufacturers should be prepared to pivot methodologies or adapt to new guidelines swiftly.
The Importance of Continuous Innovation
Continuous innovation stands as a cornerstone for success in vancomycin manufacturing. In a fast-evolving industry, resting on one’s laurels is a recipe for obsolescence. The importance of fostering a culture of innovation cannot be overstated. This not only addresses the immediate challenges faced by manufacturers but also positions them as leaders in the field.
"Innovation is not just about doing something new; it's about doing something better."
To adapt to the shifting landscape of microbial resistance and regulatory pressures, firms must be proactive in their research and development activities. Developing new techniques, investing in process improvements, and exploring alternative manufacturing pathways pave the way for enhanced product quality and reliability.