Understanding Carbon Arc: Principles and Applications
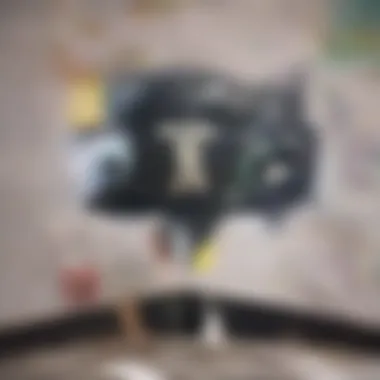
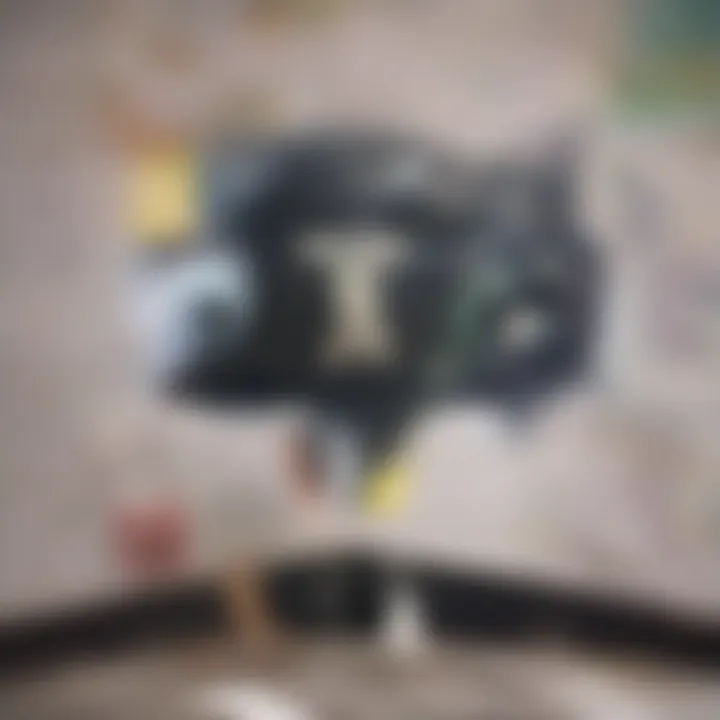
Research Overview
Carbon arc technology has gained increasing significance in various fields, owing to its efficiency and versatility. This technology utilizes the principles of arc discharge—specifically, the generation of light and heat through electric arcs between carbon electrodes. The research aims to provide a detailed exploration of the fundamental principles underpinning carbon arc processes, tracing their historical evolution and uncovering their contemporary applications across multiple sectors such as industry, art, and research.
Summary of Key Findings
The investigation into carbon arc technology has revealed several key insights:
- High Efficiency: Carbon arcs produce substantial amounts of light and thermal energy, making them efficient for applications like welding and lighting.
- Versatile Applications: The technology is employed in fields ranging from metallurgy to artistic endeavors, demonstrating its wide applicability.
- Safety and Technological Advances: Modern advancements have improved the safety of using carbon arc equipment while enhancing overall performance.
Methodologies Employed
To gather comprehensive data, a mixed-methods approach was adopted. This included both qualitative reviews of historical literature and quantitative analyses of contemporary research studies. By synthesizing findings from multiple sources, a clearer picture of carbon arc technology emerged, highlighting not only its foundational principles but also its evolving applications.
In-Depth Analysis
Exploring the individual components of the carbon arc provides a deeper understanding of its functionality and diverse uses. The following sections breakdown important aspects of this technology.
Detailed Examination of Results
Carbon arc generation involves a few specific processes. Firstly, a high-voltage electric current is passed between two carbon electrodes, creating an arc. This arc results in a plasma state, a highly energetic phase that generates extreme temperatures conducive to various applications.
- Welding: The high temperature achieved during carbon arc generation allows for effective welding processes, where seams can be fused together.
- Lighting: It has been historically used in carbon arc lamps, which provided bright, powerful illumination used in film, theater, and even street lighting.
Comparison with Previous Studies
Comparative research indicates a significant shift in the application of carbon arc technology. Earlier studies primarily focused on industrial welding and electric lighting, whereas recent explorations have highlighted its integration into cutting-edge fields like materials science and conservation. There is a growing interest in using carbon arcs in 3D printing and in creating aesthetic installations as well. Some notable studies, such as those by researchers at MIT, have examined the potential of carbon arc systems in fusion energy research.
"The transition from carbon arc's historical roles to its emergent applications underscores the versatility of this technology in modern society."
Prelims to Carbon Arc
Understanding carbon arc technology is crucial for anyone interested in industrial applications, scientific research, or artistic expressions. This section aims to give a clear overview of what carbon arc is, its relevance, and its impact across various fields.
Carbon arc refers to an electric arc formed between two carbon electrodes that are energized. As it produces intense heat, the carbon arc finds its place in numerous applications, from welding to lighting effects and more. One of the significant benefits of carbon arc technology is its efficiency in conducting heat, which can be harnessed for various tasks.
Importance and Applications
The discovery and application of carbon arc have paved the way for advancements in both mechanical and artistic domains. The arc provides a suitable medium for high-temperature environments, making it invaluable for welding metals and processing materials. With precise temperature control, industries can achieve better material fusion and integrity.
In artistic contexts, carbon arc technology allows for unique lighting and sculptural methods that produce striking visual outcomes. This duality underlines how carbon arc transcends traditional applications by integrating into both practical and creative realms.
Key Considerations
Understanding carbon arc also involves consideration of safety and environmental impacts. The generation of carbon arc involves the risk of hazardous fumes and exposure to high temperatures. Therefore, adopting appropriate safety measures is critical in any setting utilizing this technology.
The evolving nature of carbon arc technology presents continuous learning opportunities for students and professionals alike. Its applications are not static; they adapt based on innovations in technology and materials science. As such, being informed about the basic principles can greatly benefit various stakeholders.
In summary, the introduction to carbon arc encapsulates the essence of a versatile technology with numerous implications in modern industries and arts. This foundation will pave the way for deeper explorations into its historical context, fundamental principles, and evolving applications.
Historical Context
The historical context of carbon arc technology is essential to comprehend its development and the impact it has made across various industries. Understanding the timeline of its innovation provides insights into how the technology has adapted and evolved in response to changing demands and advancements. The origins trace back to the early 19th century when the fundamental principles of arc discharge were first explored, leading to a plethora of applications that still resonate today.
Early Innovations
The concept of arc lighting was pioneered by Sir Humphry Davy in 1802 when he demonstrated the first electric arc lamp. This marked a significant turning point in how people viewed electric light and its potential applications. Soon after, various inventors, including Nikola Tesla and Thomas Edison, further contributed to the development of electric lighting, where the carbon arc became integral.
During the late 1800s, carbon arc lamps illuminated streets and theaters, introducing a new era of public lighting. These lamps consisted of two carbon rods, which, when electricity passed through, produced a bright light. The brightness of the arc compelled many sectors to adopt carbon arcs, inspiring innovations in electrical engineering and materials science.
Evolution of Usage
Over the decades, the usage of carbon arc technology has evolved from initial lighting solutions to pivotal applications in industrial processes. By the 20th century, carbon arc welding emerged as a method for joining metals. This process took advantage of the intense heat generated by the arc, allowing for the melting and fusion of workpieces. The demand for stronger and more durable materials in manufacturing sectors fueled this transition.
Modern advancements have refined the efficiency and applications of carbon arc systems. With the rise of automation and stricter safety standards, usage has become more specialized. Today, carbon arc technology is not only prevalent in welding but also in sculptural applications and artistic lighting setups. The knowledge accumulated over the years has highlighted the versatility and significance of carbon arc systems in contemporary industry and art.
The historical trajectory of carbon arc technology illustrates a fascinating interplay of science, industry, and art, shaping its current status as a vital tool in modern applications.
Principles of Carbon Arc Generation
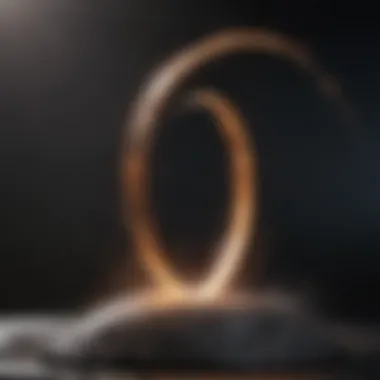
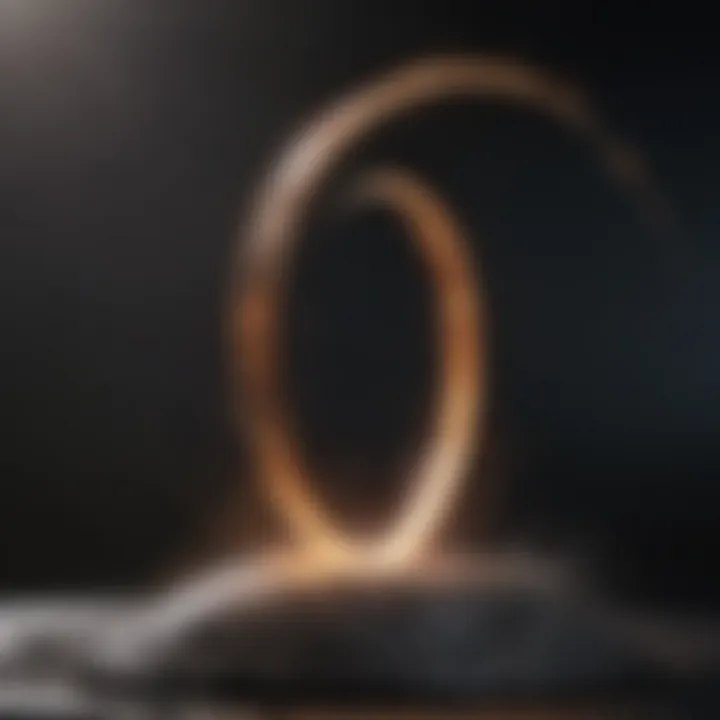
The principles of carbon arc generation form the foundation of understanding how this technology operates and its significance in various applications. This section provides insights into the mechanics and electrical characteristics of carbon arc systems. A thorough grasp of these principles is critical because it assists technicians, researchers, and students in evaluating performance aspects and benefits of carbon arc compared to other technologies.
Basic Mechanics
The basic mechanics of carbon arc generation involve creating an electrical arc between two carbon rods. When a sufficient voltage is applied, a path of ionized gas forms between the carbon electrodes, leading to a high-temperature arc. This is crucial for numerous applications, including welding, as it produces intense heat necessary for melting and fusing materials.
- Electrode Interaction: The distance and alignment between electrodes influence arc stability and energy output. Variations in spacing can affect the arc's intensity and direction, important factors during welding or heating processes.
- Arc Stability: Stability is primarily dependent on current flow. An unstable arc can fluctuate, leading to inconsistent results. Effective control of the supply current helps maintain a steady arc, improving the quality of the work performed.
- Cooling Mechanisms: Managing temperature is necessary to prolong the life of electrodes. Efficient cooling systems reduce the risk of damage to components and improve overall system performance.
These mechanical aspects allow professionals to design effective carbon arc systems aligned with specific industrial needs.
Electrical Properties
The electrical properties of carbon arc generation are essential for characterizing its operational effectiveness. Understanding current, frequency, and voltage influences how the arc behaves during operation.
- Current: Typically, carbon arcs operate on direct current (DC) to facilitate stable arcs. Current effectively governs the heat produced and dictates how well materials can be welded or processed.
- Voltage: The voltage must be carefully managed to sustain the arc without leading to instability. Too low a voltage may extinguish the arc, while excessive voltage can cause excessive wear on electrodes.
- Resistance and Conductivity: The fabric of the carbon electrodes impacts the overall efficiency of the arc. Carbon possesses specific resistive properties that affect how electricity flows through it. Ensuring a compatible composition of the electrodes helps maximize conductivity and minimize losses during operation.
Overall, the understanding of electrical properties not only fosters the efficiency of carbon arc systems but also enables innovation in enhancing their capabilities.
Understanding the principles behind carbon arc generation is key to maximizing its potential in various industrial applications. This knowledge empowers professionals to adapt technology for improved efficiency and effectiveness.
Comparison with Other Arc Discharges
The section on comparing carbon arc discharges with other types is vital for understanding the relative advantages and specific applications of carbon arc technology. It enriches the reader's knowledge about how different methods of arc generation can influence outcomes in various contexts. Each arc type has unique characteristics that impact efficiency, safety, and application.
Tungsten Arc
Tungsten arc welding, also known as Tungsten Inert Gas (TIG) welding, utilizes a non-consumable tungsten electrode to create the arc. This process allows for precise control of the heat input, making it suitable for critical applications where integrity is paramount. The arc produced is stable and can be used with or without filler material, which provides flexibility depending on the task.
Some key points of Tungsten arc technology include:
- Versatility: It works well on a range of materials such as steel, aluminum, and even exotic metals.
- Quality: The welds produced are generally of high quality, as the heat is controlled more effectively compared to other methods.
- Cleanliness: Produces less spatter and requires less cleanup.
Despite its advantages, Tungsten arc also has limitations:
- Speed: It is generally slower than some other methods, making it less suitable for high-volume production.
- Skill Requirement: Operators need specific training to wield the machine competently, which can be a downside in places where skilled labor is limited.
"Tungsten arc welding delivers precision but at the cost of increased skill and time investment."
Metal Inert Gas (MIG) Arc
Metal Inert Gas (MIG) welding employs a continuous wire feed and an inert gas shield, making the process highly efficient for mass production and industrial applications. This method creates a stable arc, allowing for deeper penetration and faster welding speeds, which can be beneficial for combining materials quickly.
Key aspects of Metal Inert Gas technology include:
- Speed: MIG welding is faster than tungsten arc due to the continuous wire feed.
- Ease of Use: Higher tolerance to operator skill levels, allowing for quicker ramp-up times for workers.
- Cost Efficiency: It tends to involve less protective equipment and setup, reducing overall operational costs.
However, MIG welding does present challenges:
- Heat Input: It may not provide as fine control over heat versus TIG, leading to risks of warping, especially in thinner materials.
- Spatter: The process often leaves behind more spatter, requiring additional cleanup time.
In summary, while carbon arc technology offers unique benefits like artistic applications and certain metal processing advantages, comparing it with Tungsten and MIG arcs offers crucial insights into its role in the broader welding landscape. Understanding these differences allows industries to select the most appropriate arc discharge method based on specific needs and applications.
Applications in Industry
The applications of carbon arc technology in industry are vast and varied. Recognizing the significance of carbon arc methods allows for deeper insights into its practical uses that span several sectors. Carbon arc serves as a versatile tool for both welding techniques and material processing. Its adaptability and efficiency contribute to its status as a key player in modern industrial settings.
Welding Techniques
Carbon arc welding is a prominent application of carbon arc technology. This technique involves using an electric arc between a carbon electrode and the workpiece. The heat generated melts the base material, allowing for strong fusion of metals. It's valued for several reasons:
- High Temperature Generation: The carbon arc can reach extremely high temperatures, facilitating the melting of various metals.
- Strong Joints: This method produces robust welds, with excellent mechanical properties that resist cracking.
- Cost-Effectiveness: Compared to other welding methods, carbon arc welding can be more economical in terms of equipment and operational costs.
However, there are considerations as well. The process typically produces significant fumes and light, requiring proper ventilation and protective gear for operators. Ensuring safety is paramount, as the intense light and sparks produced can pose serious hazards.
Material Processing
Beyond welding, carbon arc technology is employed in material processing, particularly in applications like cutting and surface treatment. The characteristics of the carbon arc make it ideal for these processes.
- Cutting: The high temperature of the carbon arc makes it suitable for cutting through thick materials, such as steel and other alloys, quickly and efficiently. This allows for precision in manufacturing and assembly tasks.
- Surface Treatment: Carbon arc processes can also be used for surface hardening, providing enhanced durability to materials. The heat treatment improves wear resistance and extends the lifespan of components.
The relationship between carbon arc and material processing illustrates how this technology contributes to increased productivity. Operators have been able to achieve precise results more efficiently compared to traditional methods.
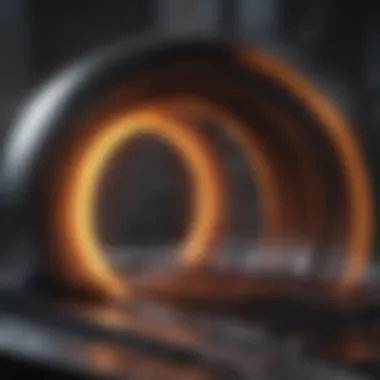
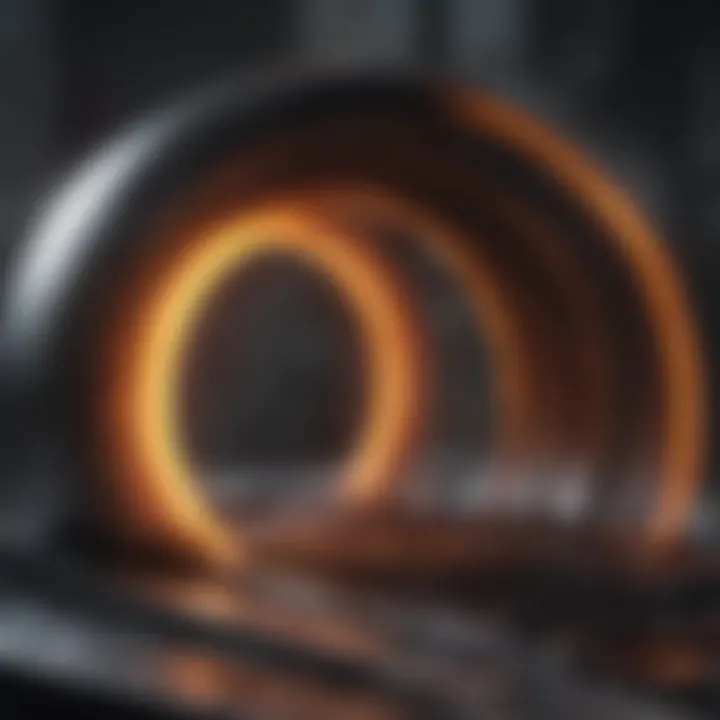
In summary, the applications of carbon arc in industry, most notably in welding techniques and material processing, highlight its essential role in advancing productivity and efficiency. As industries evolve, understanding these applications becomes increasingly important for informed decision-making regarding technology adoption.
Artistic Uses of Carbon Arc
The artistic dimension of carbon arc technology reveals a fascinating intersection between science and creativity. Artists and creators leverage the unique properties of carbon arc for a variety of applications, transforming conventional practices into innovative expressions. This section digs into two primary areas of artistic use: sculptural applications and lighting effects.
Sculptural Applications
Utilizing the carbon arc for sculptural endeavors provides an artist with unparalleled opportunities for manipulation of materials. The intense heat generated during carbon arc welding permits the fusion of various metals and materials that may otherwise resist bonding.
Artists can sculpt and fabricate with precision, often enhancing the structural integrity of their pieces. For instance, large-scale installations benefit from the strength exhibited by carbon arc techniques.
The ability to create intricate designs using carbon arc leads to effects that are difficult to reproduce using traditional methods. Remarkably, the versatility allows for experimentation with metal textures and surface finishes, promoting a range of expressions from polished to oxidized appearances.
Additionally, carbon arc can be applied to various metals, including steel and aluminum, enriching the artist's palette. Some artists combine welding with other disciplines, such as glassblowing, to create complex works that embody a dialogue between different media. This integration can yield stunning visual and tactile experiences. Further exploration into artist methods can be found on platforms like wikipedia.org.
Lighting Effects
Lighting applications of carbon arc technology further amplify its significance in art. Historically, carbon arc lights were among the first forms of electric lights, imparting a bright, white glow that is striking. Their utilization was widespread in early theater productions and film, enhancing dramatic scenes with illumination that was hard to replicate with other lighting types.
Today, artists create installations that incorporate carbon arc lighting to achieve unique visual impacts. The arcs produce distinct shadows that can enhance depth, leading to captivating results when combined with spatial arrangements. Light-sculptures often utilize the dynamic interplay of light and shadow, engaging audiences as they move through the space.
"The sophistication of light controlled by arc technology allows for creative experimentation. It’s a canvas in itself for conceptual themes and emotional responses."
Classroom applications also showcase carbon arc technology through interactive exhibits aimed at educating audiences about electrical principles and light behavior. Artists may merge science and art, drawing in visitors to experience a new narrative through light.
In summary, the artistic uses of carbon arc extend beyond mere aesthetics. They embody a blend of innovation and tradition, fostering dialogue between artist and material, while also inviting the audience to perceive the work in multifaceted ways.
Safety Considerations
Safety considerations surrounding carbon arc technology are critical for minimizing risks associated with its operation. Carbon arc generation involves high temperatures and intense electrical currents that can pose various safety hazards. Ensuring safety not only protects the individuals operating the equipment but also safeguards surrounding personnel and properties. The significance of addressing these considerations cannot be overstated, especially for students, researchers, and professionals who engage with this technology.
Hazards of Arc Generation
The generation of a carbon arc can lead to several hazards that users must be aware of:
- Electrical Shock: The high voltage involved in creating an arc can cause severe electrical shocks. This risk is higher if proper grounding and insulation measures are not taken.
- Exposure to Radiation: Arc discharges emit ultraviolet (UV) radiation, which can cause skin burns and eye damage. Users are at risk of arc eye, a painful condition resulting from exposure to UV light without proper eye protection.
- Fumes and Gases: When materials undergo the carbon arc process, they can release harmful fumes. Prolonged inhalation of these gases can have serious health implications.
- Heat and Burns: The temperatures generated can exceed thousands of degrees Celsius. This poses a risk of burns if operators come into contact with hot surfaces or molten materials.
Users must be thoroughly trained to recognize and mitigate these hazards. Implementing safety protocols is essential in a workspace where carbon arc technology is applied.
Protective Equipment
Using adequate protective equipment is a fundamental aspect of ensuring safety when working with carbon arc systems. Some key items of personal protective equipment (PPE) include:
- Protective Eyewear: Specialized welding helmets or goggles should be worn to protect the eyes from UV radiation and flying debris. These items should meet standards that filter out harmful light.
- Heat-Resistant Clothing: Protective clothing, such as fire-resistant jackets and gloves, helps in preventing burns from both thermal radiation and contact with hot materials.
- Respirators: In applications where fumes and gases are prevalent, the use of respirators is crucial. They protect the user from inhaling harmful substances.
- Ear Protection: Carbon arc operations can produce loud noises. Therefore, ear protection is recommended to prevent hearing loss.
- Foot Protection: Steel-toed boots are an essential part of safety gear to protect the feet from heavy objects and reduce injury risk from potential falls.
Utilizing this gear consistently and appropriately is key to maintaining safety in environments where carbon arc technology is practiced.
Efficiency Factors of Carbon Arc Systems
The efficiency of carbon arc systems is a critical discussion in the context of modern applications. Understanding these factors not only enhances performance but also contributes to sustainability and cost-effectiveness.
Energy Consumption
Energy consumption is a key aspect to consider when evaluating the efficiency of carbon arc systems. These systems rely on a substantial electrical current to initiate and maintain the arc. Typically, higher current levels yield greater arc stability and improved thermal output. However, they also lead to increased energy use. Therefore, balancing current intensity and energy efficiency is vital.
Reducing energy consumption can involve optimizing equipment settings and understanding the materials involved in the process. Utilizing advanced technologies, such as variable frequency drives, can aid in achieving efficiency improvements. Operators can also monitor their energy usage to identify potential waste sources. This allows for more informed decisions on settings and equipment upgrades.
It is important to highlight that inefficient energy use directly affects operating costs. A focus on minimizing energy consumption not only benefits the environment by lowering carbon emissions but also enhances the overall economic viability of the processes that utilize carbon arc technology.
Performance Metrics
Performance metrics are essential to evaluate how well a carbon arc system operates. These metrics encompass several factors, including output quality, thermal efficiency, and speed of operation. Understanding these parameters helps determine the real-world effectiveness of carbon arc systems across different applications.
The following performance metrics are often considered:
- Arc Stability: A stable arc generates consistent energy output, which is crucial for processes such as welding and cutting.
- Heat Generation: Measuring the amount of heat generated is important for applications requiring specific thermal regimes. Excessive heat can lead to material damage, while insufficient heat may not achieve desired effects.
- Material Efficiency: This metric evaluates how effectively the arc melts or processes the target material. Higher material efficiency can mean less waste and better economic outcomes.
- Response Time: In processes that demand rapid adjustments, the response time of the system to changes in current or voltage is pivotal.
Having a clear overview of performance metrics allows operators to make informed procedural changes that enhance performance, optimize energy consumption, and maintain the integrity of the materials being processed.
"Efficiency in carbon arc systems is not just about performance; it's about creating sustainable practices for the future."
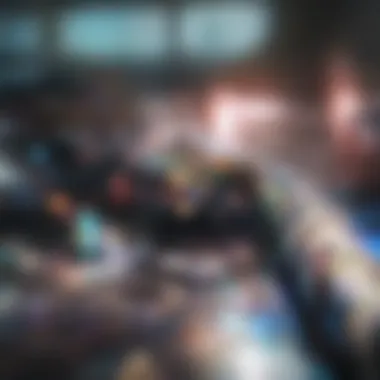
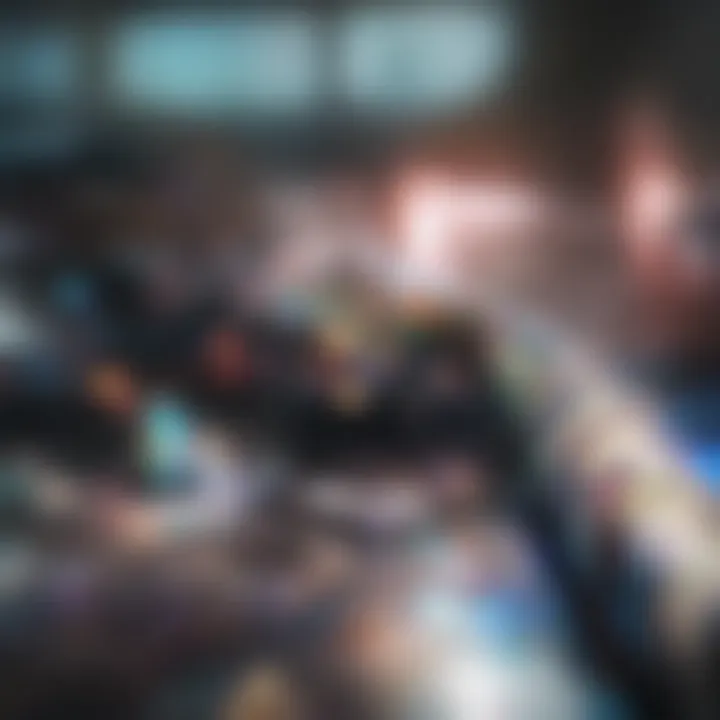
Through careful evaluation of both energy consumption and performance metrics, one can see the practical implications of efficiency in carbon arc systems, paving the way for better practices in industrial and artistic applications.
Technological Advancements
Technological advancements in carbon arc technology have greatly shaped its current applications and efficiency. The primary aim of these advancements is to optimize performance while reducing the impact on the environment. The development of more sophisticated equipment has made carbon arc processes more controllable and precise. This is vital for industries deploying these technologies for tasks like welding or material processing, where accuracy can significantly affect the outcome.
Innovations in Equipment
Recent innovations in equipment related to carbon arc technology have transformed its practicality. New power supply systems have emerged, allowing for greater control over the arc characteristics. This improves the overall quality of the work produced. Enhanced cooling mechanisms are now common in welding machines, which mitigate overheating issues that can lead to failures or reduced performance over time.
Furthermore, the design of electrodes has improved, leading to increased longevity and efficiency. For instance, carbon-based electrodes can now better withstand the intense conditions during operation. The integration of digital controls into carbon arc devices has also made them more user-friendly and responsive to varying operational demands. Equipment that supports these advancements can streamline the workflow, reduce downtime, and lower operational costs.
Integration with Other Technologies
The ability to integrate carbon arc technology with other modern technologies is transformative. One prominent area is robotics. Automated welding systems using carbon arc technology have become increasingly common in manufacturing. These systems boost productivity and allow for more complex welds that would be difficult for human operators to achieve consistently.
Additionally, the use of simulation software helps technicians visualize and plan welding processes. This reduces the potential for errors and enhances the efficiency of the operation.
Another significant integration is with digital monitoring tools. These tools can assess the quality of the weld in real time, allowing for immediate adjustments. By combining carbon arc processes with these technologies, industries can enhance both safety and quality control.
"Technological advancements not only enhance the effectiveness of carbon arc processes but also expand their potential applications and markets."
In summary, technological advancements in carbon arc systems mark a pivotal shift toward more efficient, precise, and versatile applications across various industries.
Environmental Impact
The environmental impact of carbon arc technology is a critical aspect of its discussion. As industries increasingly prioritize sustainable practices, understanding how carbon arc generation affects our environment is essential. This section examines two significant elements: the carbon footprint associated with carbon arc processes and strategies related to waste management. By analyzing these factors, we highlight both the benefits and challenges that carbon arc technology presents concerning environmental sustainability.
Carbon Footprint Assessment
In assessing the carbon footprint of carbon arc technology, several variables must be considered. The carbon arc process itself produces emissions, primarily from energy consumption. Since carbon arcs often require substantial electricity, the source of this energy is vital in determining the overall emissions profile. If the electricity comes from fossil fuels, the carbon footprint increases significantly compared to renewable energy sources.
Furthermore, the materials used in carbon arc applications can also influence the carbon footprint. For instance, the choice of carbon electrodes and other associated materials affects the overall lifecycle emissions. Understanding these factors is vital for industries aiming to reduce their environmental impact and comply with increasingly strict regulations.
Waste Management Strategies
Proper waste management strategies are essential to minimize the environmental impact of carbon arc technology. This includes the handling of used electrode materials and hazardous waste generated during the process. Recycling programs for carbon electrodes can help mitigate waste and reduce the reliance on new materials.
Additionally, companies can implement best practices to ensure that waste is treated according to environmental standards. Effective training for employees on waste handling and disposal is vital. Industries need well-structured waste management plans that include:
- Identification of waste types: Categorize waste based on toxicity and recyclability.
- Collection protocols: Establish systems for the safe collection and storage of waste materials.
- Partnerships with recycling firms: Collaborate with specialists in waste processing to enable proper disposal and recycling methods.
By implementing efficient waste management strategies, companies can substantially lower their environmental impact, ensuring a more sustainable approach to carbon arc technology.
Future Prospects of Carbon Arc Technology
As industries continue to innovate, the future of carbon arc technology presents a compelling narrative filled with potential. The evolution of this technology is essential for various applications, including welding, material processing, and artistic endeavors. Understanding its future prospects allows stakeholders to adapt and integrate new advancements into current practices.
Emerging Research Directions
Recent research is focusing on improving the efficiency and sustainability of carbon arc systems. Advances in material science contribute to more durable electrode materials that can withstand higher temperatures and prolonged use. Moreover, efforts are directed toward the development of automation and robotics to optimize processes that use carbon arc technology. Researchers are exploring ways to minimize emissions and energy consumption while maximizing output quality. These directions not only aim to enhance performance but also address environmental concerns that accompany traditional methods.
For example, projects exploring hybrid technologies that combine carbon arc principles with alternative energy sources are gaining traction. Innovations such as integrating carbon arc welding with solar energy could significantly reduce the carbon footprint of manufacturing processes. This aligns with broader sustainability goals that many industries are adopting.
"The push towards cleaner technology necessitates a reevaluation of existing processes, making carbon arc a subject of immense study in the quest for greener solutions."
Potential Market Trends
The landscape for carbon arc technology is poised for change. As more sectors embrace automation, the demand for skilled professionals adept in carbon arc techniques will likely rise. Educational programs may evolve to include advanced training related to carbon arc systems. This could attract students and specialists from various academic backgrounds.
In addition to education, market trends point toward increased collaboration between manufacturers and research institutions. This collaboration aims to spawn innovations that not only enhance product performance but also foster sustainable practices.
Some notable trends to watch include:
- Increased application in renewable energy sectors: The search for effective methods for joining materials in energy production opens avenues for carbon arc techniques.
- Expanded role in the artistic world: Carbon arc technology is being redefined in artistic creation, leading to unique opportunities in sculpture and installation art.
- Integration of AI in process optimization: Artificial intelligence could play a role in refining carbon arc operations, enhancing precision and reducing waste.
Closure
The conclusion serves as a pivotal moment in this article, summarizing the rich landscape of carbon arc technology while also emphasizing its significance across various domains. Through the discussions in earlier sections, readers gain a layered understanding of the principles, applications, and implications of carbon arc systems. This technology is not merely a relic of historical experimentation; it remains a relevant and evolving force in contemporary society.
One important element is the clarity provided regarding safety considerations. It highlights the potential hazards associated with carbon arc generation. Understanding these risks ensures that professionals can engage with this technology safely, safeguarding both personnel and the environments in which they operate.
Moreover, assessing the environmental impact is crucial. The focus on carbon footprint assessment and waste management strategies provides insights into how carbon arc usage can align with sustainable practices. This understanding is particularly relevant in today's climate-conscious world, where industries are increasingly held accountable for their ecological footprints.
The article also paints a picture of future prospects. Emerging research directions and potential market trends point toward a vibrant future for carbon arc technology. This should inspire students, researchers, and professionals to consider innovative applications and advancements that may not yet be universally recognized.
In summary, this article offers a comprehensive dive into carbon arc technology. It encapsulates its foundational principles while presenting a roadmap of its various applications. The insights gathered from this exploration will equip the reader with knowledge that is both theoretically rich and practically applicable.