Exploring Magnetic Rotors: Principles and Applications
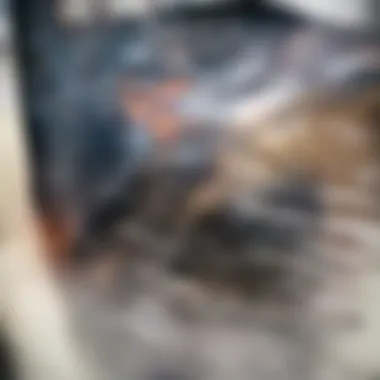
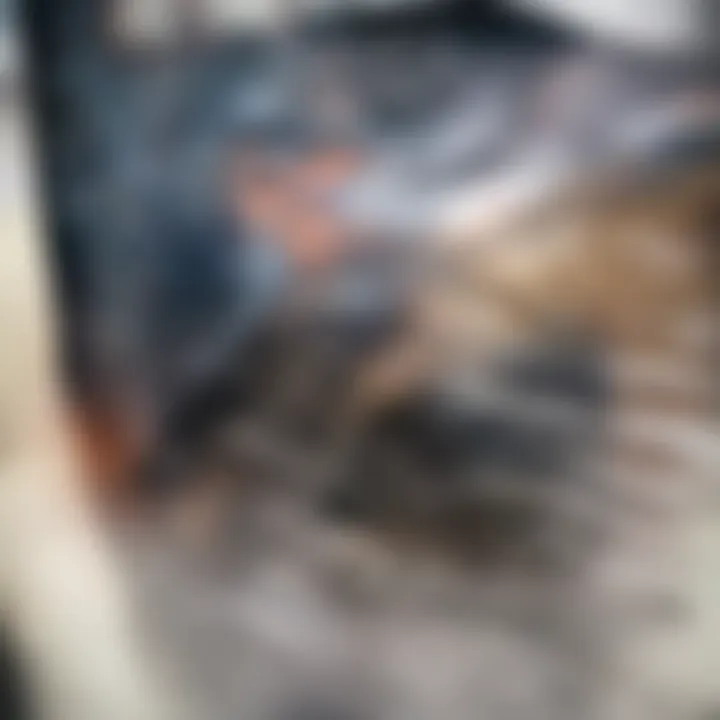
Intro
Magnetic rotors play a crucial role in the field of engineering and technology, influencing a variety of applications from electric motors to advanced robotics. Understanding the principles and mechanics behind these components is essential for developments in many sectors. Throughout this article, we will dissect the fundamentals of magnetic rotors, detail their intricate designs, and examine various applications in contemporary technology.
As we navigate through the concepts, readers will gain insights into the innovative uses of magnetic rotors and their potential to shape the future of engineering. This examination serves not only to inform but also to inspire those involved with or studying engineering and applied sciences.
Research Overview
Summary of Key Findings
Our intensive exploration into magnetic rotors reveals several key findings that reflect their significance. Firstly, we discover that magnetic rotors utilize the principles of magnetism to generate motion. This characteristic allows for increased efficiency in power conversion compared to traditional mechanical rotors. Additionally, the design of these rotors is highly adaptable, making them suitable for diverse applications across various fields such as renewable energy, automotive, and consumer electronics.
Furthermore, recent innovations in materials science have facilitated the development of lighter and more efficient magnetic rotors. As we consider their applications, the ongoing research into superconductors and permanent magnets illustrates the potential for even greater efficiencies and capabilities.
Methodologies Employed
To achieve these findings, a combination of theoretical analysis and practical experimentation was used. Theoretical approaches included:
- Mathematical modeling to predict rotor behavior under varying conditions.
- Simulation software to visualize magnetic interactions and optimize designs.
On the experimental side, techniques such as:
- Prototyping and testing were conducted to validate the theoretical predictions.
- Data collection focused on performance metrics such as torque output and energy consumption.
The synergy of these methods provides a comprehensive understanding of magnetic rotors.
In-Depth Analysis
Detailed Examination of Results
The results from our research indicate that the efficiency of magnetic rotors significantly surpasses that of traditional rotors in specific applications. For example, in electric vehicles, magnetic rotors facilitate smoother acceleration and better energy management. Additionally, when integrated with modern control systems, they exhibit enhanced responsiveness and adaptability in dynamic conditions.
Comparison with Previous Studies
Contrasting our findings with previous studies highlights substantial advancements in the field. While earlier work focused primarily on basic magnetic theories, contemporary research encompasses advanced materials and complex algorithms for better performance. This shift reflects a broader understanding of how magnetic rotors can be optimized for specific tasks as opposed to a one-size-fits-all mentality.
Intro to Magnetic Rotors
Magnetic rotors play a crucial role in various technological realms, making this topic vital for understanding modern engineering applications. Their unique functionality arises from the principles of magnetism, enabling efficient motion in devices ranging from electric motors to renewable energy systems. This section aims to delve into the core aspects of magnetic rotors, shedding light on their importance in both practical and theoretical contexts.
Definition and Functionality
At its core, a magnetic rotor is a rotating component that utilizes magnetic fields to generate motion. It works by interacting with stator systems, making use of either permanent magnets or electromagnets. The design generally accommodates various configurations based on the needs of the application. For example, in an electric motor, the rotor rotates inside a stator, producing torque that powers vehicles, appliances, and countless other devices.
The functionality of magnetic rotors is underpinned by their ability to convert electrical energy into mechanical energy effectively. Additionally, they provide higher power density compared to traditional systems, which is an advantage for applications requiring compact designs. The efficiency ratios of these devices can be significant, especially when optimized for specific tasks.
Historical Development
The evolution of magnetic rotors is closely tied with advancements in magnetism and electrical engineering. The initial concepts began taking shape in the early 19th century, with Pioneer scientists like Michael Faraday and Joseph Henry laying foundational work in electromagnetism. The understanding that magnetic fields could induce motion led to the birth of the first electric motors.
As technology progressed, so did the complexity and design of magnetic rotors. The mid-20th century saw significant innovations relating to materials and assembly methods. For instance, the introduction of rare-earth permanent magnets in the late 20th century revolutionized rotor performance, allowing for smaller and more efficient designs. Today, researchers continue to push the boundaries, exploring new materials and configurations to enhance rotor performance in various applications.
Core Principles of Magnetism
Understanding the core principles of magnetism is crucial for grasping the operational mechanisms behind magnetic rotors. These principles serve as the foundation for various applications where magnetism is utilized. Magnetic rotors rely heavily on the behavior of magnetic fields and forces as well as the fundamentals of electromagnetism. This section explains these elements, emphasizing their significance in designing and optimizing magnetic rotors.
Magnetic Fields and Forces
Magnetic fields are regions where magnetic forces can be detected. They are generated by moving electric charges or inherent magnetic materials. The force exerted by a magnetic field can influence nearby materials, which is essential for the functionality of magnetic rotors.
The strength of a magnetic field is measured in teslas (T), and it diminishes with distance from the source.
- Key characteristics of magnetic fields include:
- Direction: The orientation of the magnetic field lines indicates the direction of the magnetic force.
- Strength: The density of field lines shows field strength - closer lines represent a stronger field.
- Polarity: Every magnet has a north and south pole, where lines of force emanate outward from the north and enter through the south.
Effective designs of magnetic rotors utilize these characteristics to enhance performance in electric motors and other devices. Understanding how magnetic fields interact with various materials is necessary to improve rotor efficiency and durability.
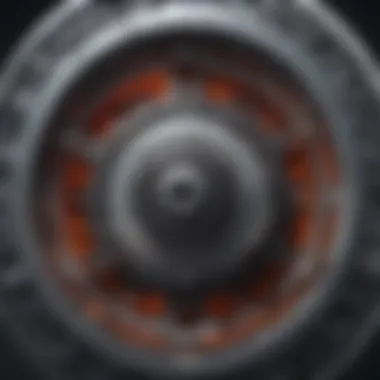
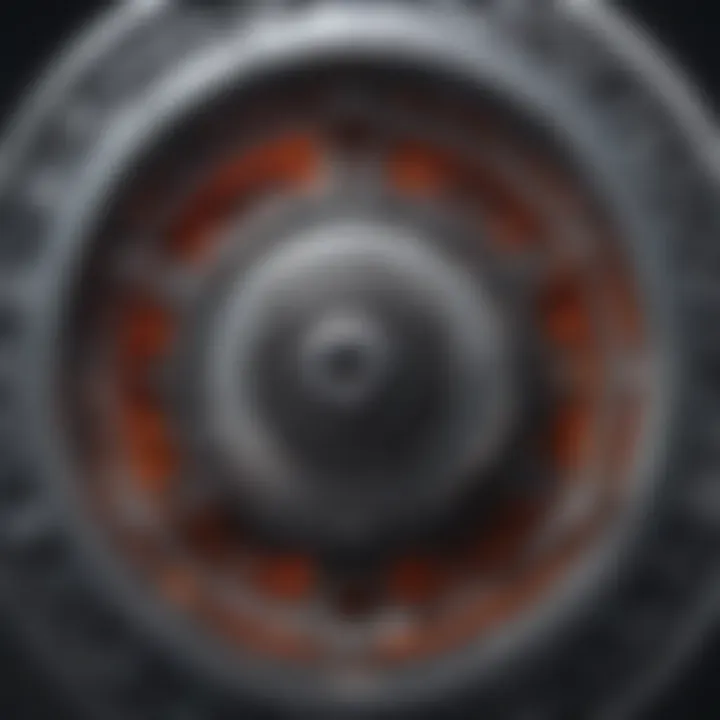
"Magnetic fields are not just invisible forces; they actively engage with materials, shaping performance and efficiency in many technological applications."
Electromagnetism Basics
Electromagnetism is a branch of physics that combines electricity and magnetism into a single theory. It describes how electric currents produce magnetic fields and how changing magnetic fields can induce electric currents. This interplay is a fundamental aspect of how magnetic rotors operate.
The basics of electromagnetism involve several concepts:
- Current and Magnetism: An electric current passing through a conductor generates a magnetic field around it. This principle is harnessed in electromagnetic coils used in magnetic rotors.
- Induction: Changing magnetic fields can induce electromotive force (EMF) in nearby conductors. This principle allows for the conversion of mechanical energy into electrical energy, essential for applications such as wind turbines.
- Faraday's Law: This law quantifies the induced EMF in a circuit due to a change in magnetic flux.
Understanding these concepts is essential for engineers and researchers working with magnetic rotors, as they provide insight into how to optimize magnetic field interactions and enhance rotor performance. Exploring these principles not only advances research but also contributes to significant technological advancements.
Design Characteristics of Magnetic Rotors
The design characteristics of magnetic rotors are crucial for their functionality and efficiency. These elements directly influence how effectively a rotor converts magnetic energy into mechanical energy. Understanding the specific design choices allows engineers to optimize rotor performance for various applications. Key benefits from these characteristics include enhanced operational efficiency, improved durability, and adaptability to different engineering requirements.
Materials Used in Construction
The choice of materials used in the construction of magnetic rotors has a profound impact on their efficiency and longevity. Two main types of materials are essential: permanent magnets and electromagnetic coils.
Permanent Magnets
Permanent magnets are integral to many types of magnetic rotors. A key characteristic of permanent magnets is their ability to maintain a consistent magnetic field without the need for an external power source. This makes them a popular choice for energy-efficient applications, particularly in electric motors.
A unique feature of permanent magnets is their high magnetic energy density, which allows for smaller and lighter designs. However, they can be affected by temperature changes, which may reduce their effectiveness. Despite this disadvantage, their simplicity in design and installation makes them a preferred choice in various applications, from small engines to large generators.
Electromagnetic Coils
Electromagnetic coils play a different role in magnetic rotor design. These coils enable the creation of a magnetic field that can be dynamically adjusted based on the electrical input. This adjustability is the key characteristic that makes electromagnetic coils widely used in advanced motor designs.
One significant feature of these coils is that they can provide greater torque at various speeds, making them suitable for applications requiring adjustable power output. However, their reliance on external power sources presents some challenges in terms of energy consumption and heat generation, which must be managed effectively to maintain rotor functionality.
Geometric Configurations
Geometric configurations of magnetic rotors determine their operational capabilities and efficiency. The design can vary significantly, with disc type and synchronous designs being two prominent configurations.
Disc Type
The disc type configuration is commonly used in many electrical applications due to its straightforward design and efficiency in generating rotational motion. The key characteristic of disc type rotors is their flat, circular shape, which facilitates uniform magnetic fields and minimizes energy loss.
A unique feature of disc rotors is their compact design, allowing for integration into numerous systems. They are beneficial in applications where space constraints exist. On the downside, disc configurations may have limitations in torque capacity compared to other designs, which should be considered during application-specific design planning.
Synchronous Designs
Synchronous designs feature a more complex arrangement. These rotors operate in sync with the frequency of the supply current, which enhances their efficiency. A key characteristic of synchronous designs is their ability to maintain constant speed regardless of load variations, making them highly efficient for certain applications.
These rotors' unique feature lies in their capability to produce stable and high torque outputs, making them suitable for industrial and high-performance environments. However, their complexity can lead to higher manufacturing and maintenance costs, thus requiring careful consideration in design choices.
Manufacturing Processes
Manufacturing processes play a crucial role in the production of magnetic rotors. Understanding and implementing efficient techniques can greatly affect the quality and performance of these devices. The manufacturing processes not only determine the capability, but also the longevity and efficiency of magnetic rotors in their varied applications.
Techniques for Magnetic Rotor Fabrication
Molding Processes
Molding processes are a fundamental technique in the fabrication of magnetic rotors. This method involves shaping materials into specific designs using molds. One significant aspect of molding processes is the ability to create complex geometric shapes with high precision. This is particularly advantageous in magnetic rotor manufacturing.
Molding allows for controlled material distribution, which enhances the uniformity of magnetic properties. Additionally, it contributes to reducing production time and costs. A unique feature of molding processes is their suitability for mass production, making them a popular choice for manufacturers looking to scale operations.
However, there are disadvantages. The initial setup cost for molds can be high, and modifications to existing molds can be time-consuming. As a result, careful planning is needed during the design phase.
Assembling Techniques
Assembling techniques are equally important in magnetic rotor construction. This aspect focuses on the mechanical and optical assembly of various components to create a finished rotor. One notable characteristic of assembling techniques is their adaptability; they can be tailored to fit different production sizes and configurations.
This flexibility makes assembling techniques a beneficial option for manufacturers who need to adjust to changing demand. Moreover, good assembly practices ensure optimal alignment of rotor components, which is vital for performance. A unique feature of assembling techniques is the integration of automation, increasingly common in modern manufacturing settings.
While automation can enhance efficiency, there are challenges related to the initial investment and training requirements for personnel. Nevertheless, proper assembly techniques can significantly improve the reliability and durability of magnetic rotors.
Quality Control Measures
Quality control measures are essential in ensuring the reliability of magnetic rotors. Implementing strict quality assessments minimizes defects and enhances product uniformity. This can significantly affect the performance of rotors in various applications.
Regular inspections and testing protocols should be in place to evaluate both material integrity and operational performance. Establishing a detailed quality control strategy can help in maintaining high standards.
Ultimately, the intersection of effective manufacturing processes and rigorous quality control forms the backbone of successful magnetic rotor production.
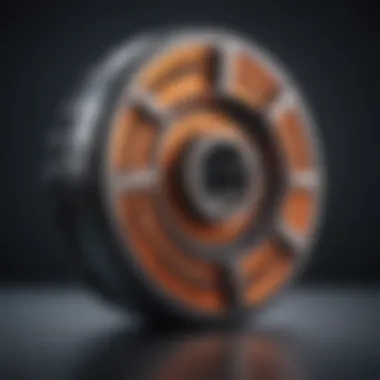

Theoretical Models in Magnetic Rotor Design
The theoretical models in magnetic rotor design are essential to fully understand their operation and maximize their efficiency. These models help researchers and engineers simulate the magnetic fields and the resultant forces within rotors. This understanding leads to designs that optimize performance and minimize potential failures. By relying on both computational and analytical methods, practitioners can explore various rotor configurations and predict their behavior under different conditions.
Magnetic Field Simulation
Computational Methods
Computational methods play a crucial role in the simulation of magnetic fields in rotor designs. Software tools like finite element analysis (FEA) allow for accurate modeling of complex geometries and magnetic interactions. One key characteristic of these methods is their ability to process large datasets, providing detailed insights into electromagnetic behavior.
The benefit of using computational methods is significant in todayβs engineering practices. They allow for quick iterations and scenario testing, leading to better-informed design decisions. A unique feature of these methods is their adaptive meshing capabilities, which optimize computational resources by focusing on critical areas of the design. However, they do require considerable computational resources and expertise, which can be a limitation for some smaller teams or projects.
Analytical Approaches
Analytical approaches offer a different route for examining magnetic fields in rotors. This method relies on mathematical models and equations to predict performance, which can be simpler and quicker than running simulations. The key characteristic of analytical methods is that they often provide closed-form solutions that help in understanding basic relationships and principles.
The value of analytical approaches lies in their straightforwardness. They can validate computational results, serving as a benchmark in design. A distinct feature is their lower computational demand, making them accessible to a wider range of researchers and engineers. Nevertheless, these methods may lack the precision required for more complex designs and may oversimplify the physical phenomena involved.
Performance Metrics
Performance metrics are vital for evaluating the efficiency and effectiveness of magnetic rotors. They provide quantifiable data that informs design choices and optimizations.
Torque Calculations
Torque calculations are a critical aspect of assessing rotor performance. They determine the torque produced by magnetic forces under various operational conditions. This is essential for inviting understanding on whether a rotor can meet specific power requirements. A key attribute of torque calculations is their ability to capture the relationship between current, magnetic field strength, and rotor speed.
The advantage of these calculations is their direct link to performance in practical applications; they help predict how engines will behave under load. A notable feature is that they can also predict failure points in the rotorβs performance. On the downside, torque calculations can be complicated by factors like temperature variations and material discrepancies, potentially leading to inaccuracies if not properly accounted for.
Efficiency Ratios
Efficiency ratios provide insight into how well a magnetic rotor converts input energy into useful work. High efficiency is a desirable characteristic, especially in applications where energy conservation is critical. Efficiency ratios help convey the ratio of output power to input powerβa crucial benchmark in rotor design.
These ratios serve as a beneficial tool for engineers looking to improve designs. They highlight energy losses and help identify areas needing enhancement. The advantage of using efficiency ratios is their straightforward nature; they are easy to interpret and communicate among stakeholders. However, calculating these ratios can sometimes oversimplify the complexities involved in real-world operations, leading to potentially misleading conclusions if not put in context.
Applications of Magnetic Rotors
The applications of magnetic rotors span a range of fields and technologies, reflecting their versatility and effectiveness in various systems. The increasing demand for energy efficiency and performance drives interest in these components, bending the edge of engineering innovation.
In electrical machines, magnetic rotors play a key role in determining efficiency and performance. Their design directly influences torque generation and overall effectiveness in converting electrical energy into mechanical motion. In renewable energy systems, magnetic rotors are essential for harnessing natural forces, which leads to sustainable power production. Furthermore, sectors like aerospace and defense leverage the precise control and reliability offered by magnetic rotors to meet strict operational requirements.
In Electric Motors
Brushless Motors
Brushless DC motors are one application of magnetic rotors that have gained significant traction in recent years. The main characteristic of these motors is their lack of brushes, which eliminates mechanical wear and enhances longevity. This feature makes them highly suitable for applications requiring reliability and low maintenance.
Furthermore, the absence of brushes allows for better thermal management since there is less heat generation. This leads to improves efficiency in converting electrical power into mechanical power. Additionally, brushless DC motors operate with a smoother torque, which is crucial for applications in robotics and electric vehicles. However, their design complexity and control system demands can be seen as downsides, requiring knowledgeable handling in engineering.
Synchronous Motors
Synchronous motors utilize magnetic rotors for controlled and efficient rotational speed. A key characteristic of these motors is that they operate at a constant speed determined by the supply frequency. This provides excellent performance in applications where speed consistency is necessary, such as in industrial drives.
The ability to run synchronously results in high efficiency and power factor correction. Moreover, they can achieve higher torque at low speeds. However, the requirement for complex control systems can also introduce challenges in terms of design and implementation.
In Renewable Energy Systems
Wind Turbines
Wind turbines effectively utilize magnetic rotors to generate electricity from wind energy. The principal advantage of utilizing magnetic rotors in turbines is their capacity to ensure efficient energy conversion. The rotor's design, which often includes permanent magnets, facilitates better performance under varying wind conditions. This feature is particularly important for maximizing energy capture in fluctuating environments. Yet, challenges arise with scaling, as larger rotors may increase installation complexity and costs.
Hydroelectric Applications
In hydroelectric systems, magnetic rotors help convert kinetic energy from flowing water into electrical energy. A significant aspect of these applications is the high efficiency achieved in power generation, which is crucial for energy sustainability. The unique feature of using magnetic rotors in hydroelectric systems is their ability for precise speed regulation, which is necessary to meet grid requirements. However, these systems also come with drawbacks, including the need for substantial investment in infrastructure and the potential environmental impact of dam constructions.
In Aerospace and Defense
Active Control Systems
Active control systems in aerospace and defense benefit from the precision and responsiveness afforded by magnetic rotors. A key characteristic of these systems is their capacity for real-time adjustments, making them highly effective in dynamic environments like aircraft. The integration of magnetic rotors allows for consistent performance under stress while minimizing weight, which is crucial for aerospace applications. A distinctive feature is their reliability under various operational conditions. However, the complex nature of these systems can pose challenges in terms of maintenance and calibration.
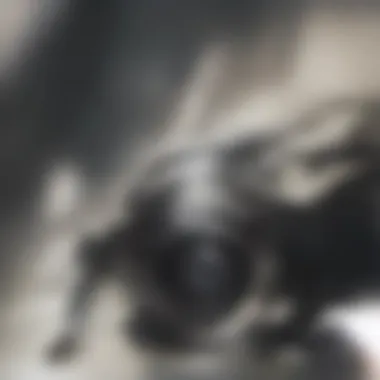
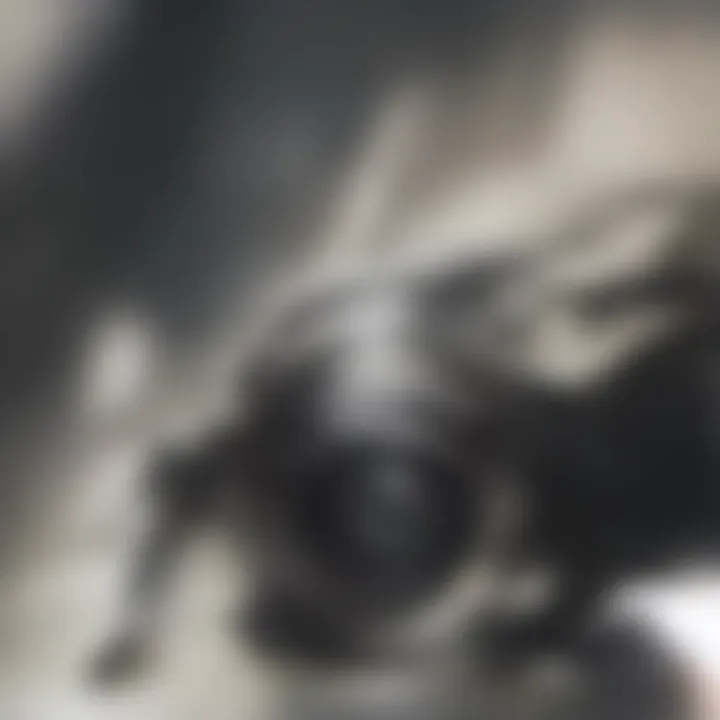
Robotics
In robotics, magnetic rotors contribute to efficient movement and control. The distinct advantage lies in their ability to provide accurate positioning and high torque density, enabling precise robotic operations. This makes them popular in applications that require speed and agility, such as robotic arms and automated manufacturing processes. One challenge here includes the potential for reduced performance in demanding environments, which could impose limitations on specific robotic tasks.
The sections covered above illustrate the profound significance of magnetic rotors. As technology continues to advance, the role of magnetic rotors will expand further, paving pathways for innovations across various industries.
Challenges and Limitations
Understanding the challenges and limitations associated with magnetic rotors is crucial for several reasons. As technology advances, potential applications become broader, yet these same innovations often face significant hurdles that can impede effectiveness and performance. Addressing these challenges will not only help in optimizing performance but also in guiding future research and development. By identifying the constraints in material selection and external conditions, engineers and researchers can innovate and create more efficient and reliable magnetic rotor designs.
Material Constraints
Material selection is one of the most pivotal elements impacting the design and functionality of magnetic rotors. The properties of materials determine not just the efficiency, but also the longevity and reliability of the rotor in real-world scenarios. Common materials like neodymium, ferrite, and various alloys are frequently used, but each has its own set of limitations.
For example, neodymium magnets have high strength but may suffer from temperature sensitivity. This means that in high-temperature environments, the performance may degrade significantly. Ferrite magnets, while more temperature stable, typically offer lower magnetic strength. The choice of materials directly influences not only the magnetic efficiency but also the weight and cost of a rotor.
Key materials challenges include:
- Temperature sensitivity: Reduced performance at elevated temperatures.
- Cost factors: High-performance magnets like neodymium can be expensive.
- Size limitations: Smaller can be insufficient for large-scale applications.
- Environmental concerns: Some materials may pose sustainability issues.
Performance Under Stress
Magnetic rotors often operate under various stress conditions in practical applications. These stress factors include mechanical stress, thermal fluctuations, and magnetic interference. Understanding how these factors affect rotor performance is essential for ensuring reliability and efficiency.
Mechanical stress can arise from rotational forces and system vibrations. If not properly designed, rotors can suffer from fatigue or catastrophic failure. Thermal performance under varying temperatures critically impacts the rotor's magnetic properties as discussed previously. Furthermore, exposure to competing magnetic fields can disrupt their operational capabilities.
In a nutshell, both mechanical and thermal stress significantly impact the performance of magnetic rotors. There are multiple ways to assess and mitigate these effects:
- Finite element analysis: To simulate stress distribution.
- Thermal management: Utilizing heat sinks or cooling techniques.
- Field shielding: To minimize interference from external sources.
"Innovations in material science can provide solutions to many of the limitations faced by magnetic rotors, leading to improved applications and enhanced performance."
In summary, grasping the challenges related to material constraints and performance under stress is essential to drive advancements in magnetic rotor technologies. By addressing these issues, researchers and engineers can further enhance the efficacy and application potential of magnetic rotors in various industrial fields.
Future Directions in Magnetic Rotor Research
As we look into the future of magnetic rotor research, it becomes evident that this field harbors immense potential for advancements and innovations. The focus on evolving technologies and materials is paramount as industries aim to enhance efficiency and performance. Researchers and engineers are now tasked with addressing emerging challenges while exploring opportunities that can significantly improve magnetic rotor applications across various sectors.
Innovative Materials
Nanocomposites
Nanocomposites have emerged as a significant topic in the context of magnetic rotors due to their unique properties. These materials generally consist of a matrix embedded with nanoparticles, which enhances their mechanical and magnetic characteristics. One of the key characteristics of nanocomposites is their improved magnetic permeability, making them an efficient choice for rotor applications. They permit better energy efficiency and reduce losses, which is crucial in electric motor performance.
A distinctive feature of nanocomposites is their lightweight nature compared to traditional materials. This aspect is advantageous in designing smaller, more compact magnetic rotors that do not compromise performance. However, one must consider that the variability in quality and production may lead to inconsistencies in performance.
Metamaterials
Metamaterials are another innovative class of materials shaping the future of magnetic rotors. These engineered materials possess unique electromagnetic properties that are not found in nature. The capability of metamaterials to manipulate electromagnetic waves leads to possibilities in optimizing rotor design, thus enhancing control and efficiency. Their primary attribute is the ability to exhibit effective magnetic properties that can be adjusted through design rather than relying solely on the material itself.
The unique feature of metamaterials lies in their tunability, allowing for dynamic adjustments based on application requirements. This adaptability makes them particularly attractive to research focused on magnetic rotor applications. Despite these advantages, metamaterials may present challenges in terms of production costs and scalability, which remain areas for further exploration in the research community.
Integration with Smart Technologies
Integrating magnetic rotors with smart technologies is another avenue fueling future advancements. As the Internet of Things (IoT) continues to permeate various industries, the need for intelligent systems becomes more pressing. Magnetic rotors that can communicate and interact with other smart devices offer significant advantages in automation and functionality. This integration can lead to enhanced performance through real-time monitoring and control, optimizing energy consumption in various applications.
The shift towards automation increases reliability and precision in rotor-driven systems. This aspect is crucial for applications in sectors such as renewable energy, aerospace, and electric vehicles, where performance and efficiency cannot be compromised. As this integration trend progresses, the potential to create more sophisticated and adaptable magnetic rotor designs will grow, promising to reshape how these components are viewed in engineering and technological contexts.
Closure
The conclusion of this article synthesizes the comprehensive insights into magnetic rotors, tying together the various elements discussed throughout the sections. It is essential to recognize how the principles of magnetism, advanced designs, and diverse applications interrelate to establish a complete understanding of the topic. Each aspect, from the manufacturing processes to the challenges facing the industry, contributes to the overall narrative of magnetic rotors as fundamental components in modern engineering.
Recapitulation of Key Points
A thorough examination of magnetic rotors reveals several crucial takeaways:
- Fundamental Principles: An understanding of magnetism, particularly magnetic fields and forces, lays the groundwork for comprehending how magnetic rotors function.
- Design and Materials: The choice of materials, such as permanent magnets and electromagnetic coils, significantly influences rotor performance. The geometric configurations like disc and synchronous designs impact efficiency.
- Applications: Magnetic rotors find critical use in electric motors, renewable energy systems, and aerospace, demonstrating their versatility and importance.
- Challenges: There are limitations, including material constraints and performance under stress, that necessitate further study and innovation for future advancements.
Significance of Continuing Research
Continued research in the field of magnetic rotors is vital for several reasons:
- Innovation: As technology evolves, the development of innovative materials, such as nanocomposites and metamaterials, can enhance the performance of magnetic rotors significantly.
- Integration with Smart Technologies: The future of magnetic rotors lies in their integration with intelligent systems. This will improve functionality and efficiency, particularly in applications requiring precise control.
- Addressing Challenges: Ongoing research is necessary to overcome material limitations and optimize rotor performance under various operating conditions.
"The research community must remain focused on advancing our understanding of magnetic rotors to unlock their full potential across industries."