In-Depth Insight into MEMS Flow Sensors
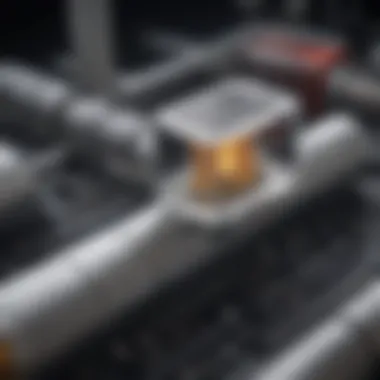
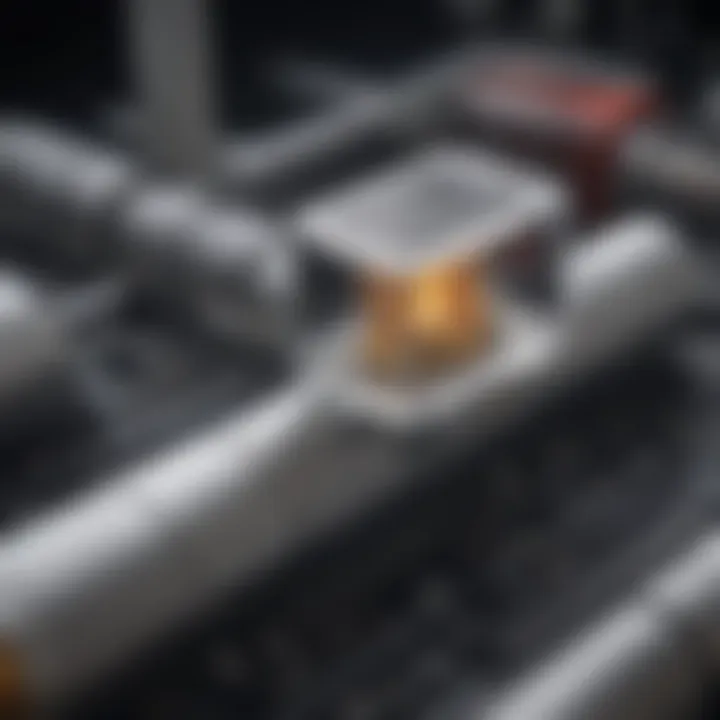
Intro
Micro-Electro-Mechanical Systems (MEMS) flow sensors have emerged as pivotal technology in a wide range of applications. These sensors enable precise measurement of fluid flow, playing a critical role in various sectors, from medical devices to automotive systems. Their compact size, low power consumption, and high sensitivity offer distinct advantages over traditional flow measurement technologies.
The rise of MEMS technology coincides with an increased demand for miniaturized devices that deliver reliable performance in constrained environments. As industries strive for greater efficiency and control, understanding MEMS flow sensors becomes not just relevant, but necessary.
This examination aims to provide clarity on the design, functionality, applications, and the potential challenges surrounding MEMS flow sensors. In doing so, it invites professionals and enthusiasts alike to delve into the intricate world of MEMS technology.
Research Overview
Summary of Key Findings
The comprehensive exploration of MEMS flow sensors reveals several critical insights. First, their unique design leverages micro fabrication techniques, allowing for exceptional accuracy in measuring fluid dynamics. Second, MEMS sensors can operate in adverse conditions, making them suitable for diverse applications. Finally, they offer significant embedding potential in IoT devices, enhancing smart technology environments.
Methodologies Employed
To gather data regarding MEMS flow sensors, various methodologies were utilized, including:
- Literature Review: Analyzing existing research papers and articles provided a foundation regarding the development and advancements in MEMS technology.
- Case Studies: Examining specific applications in industries such as healthcare and automotive highlighted the practical implementation of MEMS flow sensors.
- Technical Analysis: Detailed examination of sensor designs and attributes showcased the engineering principles at play.
In-Depth Analysis
Detailed Examination of Results
The results from this investigation underline the sophistication of MEMS flow sensors. Key aspects include:
- Response Time: MEMS sensors exhibit rapid response times due to their small mass, enabling quick adjustments to flow changes.
- Sensitivity: Their high sensitivity allows minimal flow levels to be detected accurately, crucial for applications in fields like pharmaceuticals where maintaining exact fluid quantities is vital.
- Integration: The compatibility with microcontroller systems facilitates seamless integration into larger electronic frameworks, enhancing their utility.
Comparison with Previous Studies
When compared to previous studies on traditional flow sensors, MEMS flow sensors consistently demonstrate superior performance regarding size and power efficiency. For instance, older mechanical sensors often require extensive calibration and maintenance. In contrast, MEMS technology integrates self-calibration features, making them more reliable for long-term use.
"The evolution of MEMS technology marks a significant leap, aligning with the demands of modern industries for precision and compactness."
The shift towards MEMS flow sensors is evident when examining their integration in devices like insulin pumps and automotive fuel systems. These developments underscore the transformative impact of MEMS on both the technology landscape and industry standards.
This examination of MEMS flow sensors not only highlights their advantages but also encourages a broader discussion about their role in future advancements. Through careful analysis, this article aims to inform and educate, ensuring that readers grasp both the technical aspects and broader implications of MEMS technology in contemporary applications.
Preface to MEMS Technology
Micro-Electro-Mechanical Systems (MEMS) represent a pivotal advancement in technology, merging mechanical elements, sensors, actuators, and electronics on a single miniature platform. This integration not only optimizes performance but also allows for applications that were previously unattainable. In the context of flow sensors, MEMS technology significantly enhances measurement precision, reduces size and weight, and minimizes power consumption. This article aims to provide a comprehensive understanding of how MEMS technology informs the design and function of flow sensors.
Definition and Overview
MEMS devices are composed of tiny structures that operate in micrometers, often resembling microscopic machines. These devices perform a variety of functionalities, including sensing, actuation, and signal processing. The key to MEMS technology lies in its ability to harness microfabrication techniques from the semiconductor industry, enabling mass production of miniature components. The melding of mechanical and electronic systems allows for enhanced performance characteristics, making MEMS a preferred choice in various applications.
Historical Context of MEMS Development
The evolution of MEMS can be traced back to the early 1960s when the initial concepts emerged from advancements in silicon technology. The first MEMS devices were primarily used in the automobile industry, such as pressure sensors and accelerometers. Over the decades, the field grew exponentially with critical developments in fabrication methods, notably photolithography and etching techniques in the 1990s. This period also saw a push for MEMS applications in consumer electronics, healthcare, and aerospace, marking a shift to more diversified uses of these technologies.
Key Components of MEMS Devices
MEMS devices are composed of three main components, each playing a critical role in their operation:
Micro Sensors
Micro sensors are essential components of MEMS technology. They detect physical phenomena such as pressure, temperature, and flow rates. One key characteristic of micro sensors is their small size, allowing for integration into compact systems. This is particularly advantageous for applications requiring minimal space, such as in portable devices. However, a unique feature of micro sensors is their sensitivity to environmental factors, which can sometimes lead to challenges in calibration and reliability in fluctuating conditions.
Micro Actuators
Micro actuators are designed to convert electrical signals into mechanical motion. Their compact design facilitates precise control in applications like fluid valves or micro pumps. Notably, micro actuators can operate with high speed and accuracy, making them effective in dynamic environments. One disadvantage is that these components may require careful power management to avoid overheating and ensure prolonged functionality.
Micro Structures
Micro structures serve as the foundational elements in MEMS devices, providing the physical framework for sensors and actuators. Their unique characteristic includes complex geometries that enhance sensitivity and performance. This complexity allows for optimizing functions specific to applications such as flow sensing. However, creating micro structures can incur higher production costs, which could affect overall affordability in widespread applications.
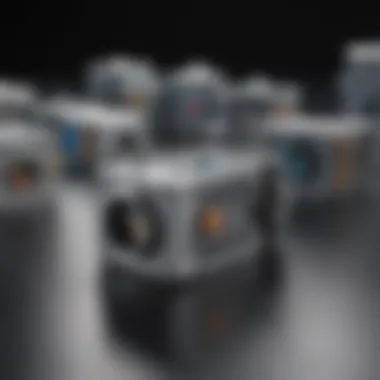
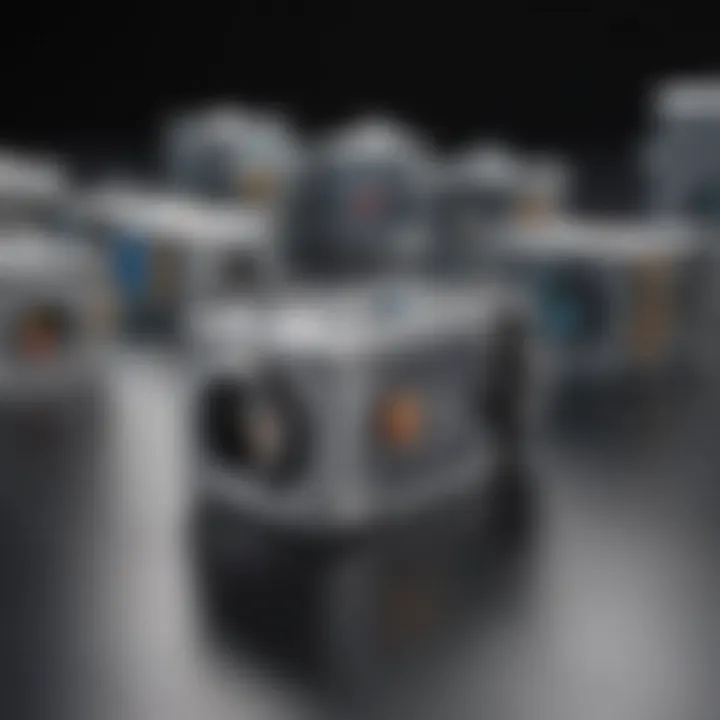
"MEMS technology bridges the gap between the micro and macro worlds, allowing for innovations that extend into numerous industries."
In sum, the introduction to MEMS technology emphasizes its foundational principles, historical development, and key components as critical to understanding MEMS flow sensors and their applications. These aspects highlight the relevance and significance of MEMS in modern technological advancements.
Understanding Flow Sensors
Flow sensors are essential devices that help us measure the flow of fluids. Their significance lies not only in various industrial applications but also in understanding fluid behavior in different environments. In this context, flow sensors provide critical data that informs decisions related to efficiency and safety across multiple sectors, like automotive and healthcare.
Fundamentals of Fluid Dynamics
Fluid dynamics is a field focused on the behavior of fluids in motion. Understanding this area is vital for grasping how flow sensors operate and the principles driving their design.
Principles of Fluid Flow
The principles of fluid flow involve concepts like laminar and turbulent flow. These principles explain how fluids behave under different conditions. Fluid dynamics is a key aspect that influences the design of flow sensors. A primary characteristic of fluid flow is its variability; as conditions change, so do the fluid dynamics.
This variability contributes to the need for accurate measurement tools. Understanding these principles helps researchers and engineers improve sensor design to meet specific requirements of various applications. A unique feature of fluid dynamics is the Reynolds number, which helps predict flow patterns. However, reliance on this can be a disadvantage, as it may not account for complex interactions in some fluids.
Measurement Parameters
Measurement parameters are crucial in determining the performance and accuracy of flow sensors. These parameters include flow rate, pressure, and temperature. They provide benchmarks for evaluating sensor effectiveness. A key characteristic of these parameters is their impact on accuracy; incorrect readings can lead to inefficiencies.
These measurement parameters are beneficial because they inform engineers about the expected flow conditions. A distinctive feature of measurement parameters is their direct correlation to performance metrics. However, relying solely on these can lead to oversights in other contributing factors, such as chemical properties of the fluid.
Types of Flow Sensors
Flow sensors are divided into several types, each serving its purpose based on the application requirements. Understanding these variations is essential for selecting the right sensor for specific jobs.
Mechanical Flow Sensors
Mechanical flow sensors operate based on moving parts that interact with the fluid. They measure flow through mechanical movement, making them simple and reliable. A key characteristic of mechanical sensors is their durability; they can last longer in harsh conditions compared to other types. Mechanical flow sensors are popular in many applications, ranging from water meters to industrial setups. Their unique feature is their simplicity in design, which can also lead to disadvantages, like susceptibility to wear and tear from continuous use, which might affect accuracy over time.
Electrical Flow Sensors
Electrical flow sensors utilize electrical signals to measure the flow of fluid. They work by detecting changes in voltage or current as fluid flows. A major characteristic of these sensors is their sensitivity, allowing them to detect even slight variations in flow. Electrical flow sensors are beneficial in applications that require precision. Their unique feature is their adaptability; they can be calibrated to work in various environments. However, they may not perform adequately in all fluid types, particularly those with solids or high viscosity, which can interfere with the measurements.
MEMS Flow Sensors
MEMS flow sensors are advanced devices that leverage micro-electro-mechanical systems technology to achieve precise measurement. Their compact design allows for high integration within systems. A key characteristic of MEMS flow sensors is their miniaturization, which provides advantages in both space-saving and power efficiency. MEMS sensors are invaluable in applications where foot-print and energy consumption are critical, such as portable devices. Their unique feature is their ability to be produced at lower costs due to advancements in manufacturing processes. However, the sensitivity to environmental factors can be a concern, as it may lead to inaccuracies in certain situations.
Technical Principles of MEMS Flow Sensors
The technical principles underlying MEMS flow sensors are crucial to understanding their design and operational effectiveness. These principles dictate how sensors detect and measure fluid flow, leading to various applications in industries such as healthcare, automotive, and environmental monitoring.
Sensing Mechanisms
Sensing mechanisms determine how a flow sensor interacts with the fluid to produce measurable signals. Two prominent methods are the Coriolis effect and capacitive sensing.
Coriolis Effect
The Coriolis effect is a phenomenon that occurs in rotating systems. In MEMS flow sensors, this effect is harnessed to measure the mass flow rate of fluids. When a fluid flows through a vibrating tube, the Coriolis effect causes a phase shift in the vibration. This shift is proportional to the mass flow rate of the fluid, making it a precise measurement technique.
A key characteristic of the Coriolis effect is its sensitivity to changes in flow, which enhances measurement accuracy. Additionally, sensors using this mechanism often offer robustness and excellent repeatability, characteristics essential for critical applications. However, the Coriolis effect can be more expensive to implement due to the complexity of the required components.
Capacitive Sensing
Capacitive sensing measures changes in capacitance between conductive plates. In MEMS flow sensors, the variation in capacitance corresponds to the fluid's flow rate, thereby allowing for fluid measurement. One significant advantage of capacitive sensing is its compact design, which fits well within the small scale of MEMS devices.
The ability to provide real-time data is another key trait, making capacitive sensors popular in many applications. However, they can be susceptible to environmental factors such as temperature and pressure changes, which may impact measurement reliability.
Microfabrication Techniques
The microfabrication techniques used in creating MEMS flow sensors are vital in determining their performance and scalability. The key methods include photolithography, etching processes, and deposition methods.
Photolithography
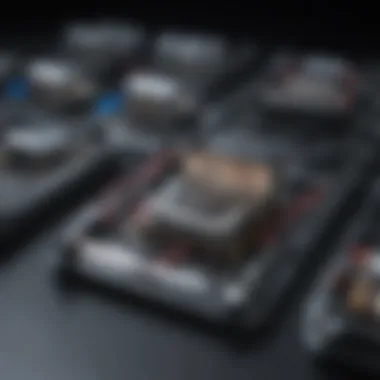

Photolithography is a process used to pattern thin films, pivotal in the development of MEMS devices. This technique allows for the precise definition of microstructures necessary for sensor functionality. It is beneficial due to its relatively high resolution, enabling the production of intricate designs and layouts.
The unique feature of photolithography lies in its adaptability. It can be applied to various materials, expanding the type of sensors that can be manufactured. However, the complexity of the equipment and the need for cleanroom environments can increase production costs.
Etching Processes
Etching processes remove layers from the surface of materials, essential for shaping the microstructures needed in MEMS flow sensors. Two primary types of etching are used: wet and dry etching. These methods allow for the refinement of sensor features, enhancing performance.
A significant characteristic of etching processes is their ability to create high aspect ratio structures, which are critical in improving sensor sensitivity and response time. On the downside, controlling the etching rate can be challenging, which might result in varying results with different batches.
Deposition Methods
Deposition methods involve adding thin layers of materials onto a substrate. Techniques such as chemical vapor deposition are crucial for creating layers essential for sensor function. One key advantage of deposition methods is the ability to produce highly uniform films, which improve the consistency and reliability of sensors.
These methods enable the incorporation of various materials, enhancing functionality. However, some deposition techniques can require high temperatures, which may limit the compatibility with certain materials.
MEMS flow sensors leverage advanced microfabrication techniques to create highly sensitive and compact devices capable of precise fluid measurements.
Applications of MEMS Flow Sensors
The section on Applications of MEMS Flow Sensors highlights their significance across various fields. These sensors are pivotal in enhancing efficiency, precision, and functionality. By studying their applications, one can appreciate how MEMS technology influences modern systems and its potential for future innovations. Understanding where MEMS flow sensors are employed reveals their critical role in diverse industries.
Healthcare and Medical Monitoring
In healthcare, MEMS flow sensors serve vital functions. Monitoring blood flow, drug delivery systems, and respiratory airflow are some key applications. High accuracy is critical in medical environments, where slight deviations can have serious implications. MEMS technology is notable for its miniaturization, which is essential in wearable devices. For instance, devices like smart inhalers utilize MEMS flow sensors to measure the precise dose of medication delivered to patients, improving treatment outcomes.
Another aspect is the integration with electronic health records. Real-time data from these sensors enhances patient monitoring. It allows healthcare professionals to make timely decisions. The capability to measure fluid dynamics in minute details aids in developing customized therapies, thereby improving patient care and safety.
Automotive Industry
In the automotive sector, MEMS flow sensors are indispensable for engine management and emissions control. They monitor fuel consumption and air intake. This leads to optimal engine performance and reduced emissions. For instance, the sensor in a fuel injection system ensures the correct air-fuel ratio. This ratio is crucial for efficient combustion, which in turn enhances fuel economy while minimizing pollutants.
Moreover, MEMS flow sensors are used in advanced driver assistance systems. They contribute to evaluating fluid flow in various systems such as cooling and lubrication. With the industry's shift towards electric vehicles, these sensors also aid in thermal management. This is significant as maintaining optimal temperatures in electric vehicle batteries is essential for performance and safety.
Environmental Monitoring
Environmental applications of MEMS flow sensors focus on air and water quality monitoring. In scenarios like pollution measurement, accurate data is vital. MEMS sensors provide the required sensitivity and precision. They help detect minute changes in flow rates and concentrations of harmful substances. Such capabilities enable regulatory compliance and proactive measures against pollution.
Additionally, these sensors play a role in meteorology. They are used for measuring atmospheric gas flows, which can help predict weather patterns more accurately. Their small size allows integration into various monitoring devices, leading to extensive deployment across urban environments.
Aerospace Applications
In aerospace, MEMS flow sensors are critical for flight safety and efficiency. They monitor fuel flow in aircraft, ensuring optimal performance. The precision of these sensors can significantly impact fuel costs over long term flights. Moreover, they are utilized for monitoring cabin air quality. Ensuring passengers' well-being is a priority, and MEMS flow sensors enables continuous tracking of air composition.
Further, their ability to withstand extreme conditions adds to their value. They perform reliably in high-altitude and high-temperatures. These qualities make MEMS flow sensors suitable for various aerospace technologies, from commercial aviation to unmanned aerial vehicles.
In short, MEMS flow sensors are central to enhancing operational efficiency, safety, and precision across numerous applications. Their versatility positions them as a key technology for future advancements.
Advantages of MEMS Flow Sensors
The significance of MEMS flow sensors extends beyond their technical specifications. They offer several advantages that make them a valuable asset across various industries. Each advantage contributes uniquely to enhancing measurement accuracy and system integration, ensuring these sensors remain relevant in a fast-evolving technological landscape. Below, we explore the key benefits of MEMS flow sensors in detail.
Compact Size and Integration
MEMS flow sensors are notably compact. This miniaturization allows for further integration into existing systems without significant redesign efforts. In many applications, space is at a premium. Therefore, having sensors that do not bulk up the device enhances overall system performance. Their small size reduces the need for large housings and additional mounting systems.
Moreover, the integration of MEMS technology can lead to simplified designs. Instead of having multiple components performing various functions, MEMS allows for the combination of sensing and actuating capabilities onto a single chip. For example, a MEMS flow sensor might combine flow measurement with real-time data processing.
High Sensitivity and Accuracy
High sensitivity is another defining feature of MEMS flow sensors. They can detect minute changes in fluid dynamics, making them suitable for precision applications. The ability to measure flow rates accurately ensures better control in processes where even slight variations can lead to significant consequences, such as in medical devices.
Accuracy is often achieved through advanced sensing mechanisms. MEMS flow sensors utilize cutting-edge technologies like capacitive and Coriolis sensing. These technologies allow for reliable readings and minimize errors, essential in high-stakes environments. Higher accuracy can lead to improved product quality and reduced waste in manufacturing processes.
Low Power Consumption
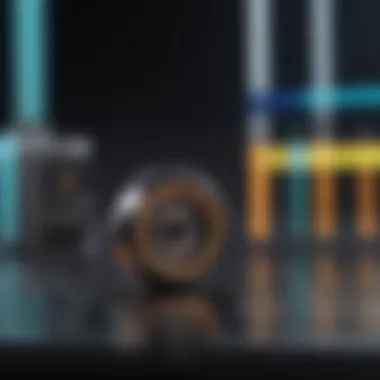
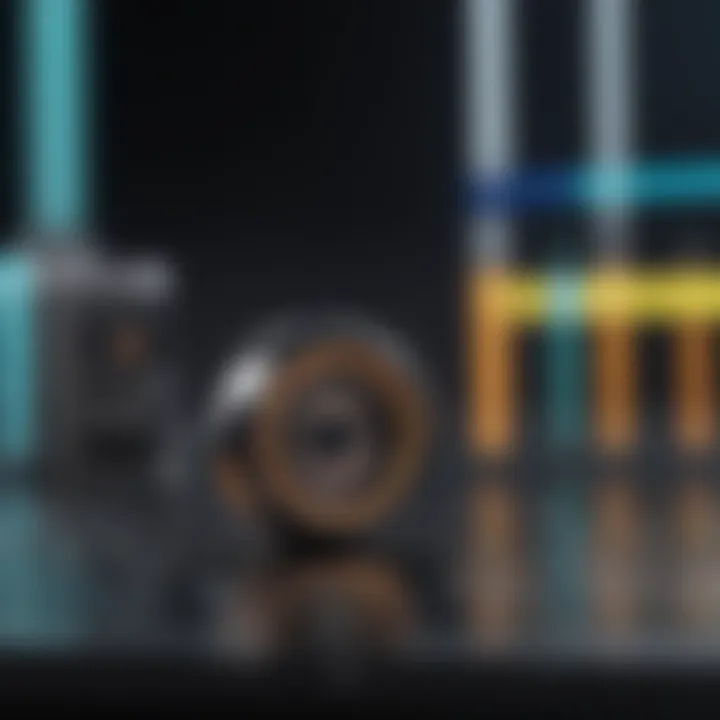
Energy efficiency is a growing concern in nearly all fields of technology. MEMS flow sensors excel in this regard as they typically consume less power than traditional flow measurement devices. The reduced power consumption not only leads to lower operational costs but also extends the lifespan of battery-powered devices, which is particularly important in the Internet of Things (IoT) applications.
By using low power, MEMS flow sensors also contribute positively to environmental sustainability. Devices powered by MEMS technology frequently lead to a smaller carbon footprint through energy-efficient operations. Thus, the applications of these sensors span even more fields, including those focused on environmental conservation.
The advantages of MEMS flow sensorsβcompact size, high sensitivity, and low power consumptionβmake them essential in modern applications across various industries. Their integration potential unlocks a new realm of possibilities in sensor technology.
Challenges in MEMS Flow Sensor Implementation
The implementation of MEMS flow sensors presents several significant challenges that must be addressed to maximize their potential within various applications. These challenges impact the performance, reliability, and overall effectiveness of the sensors. Understanding these obstacles can guide future developments and shape the evolution of MEMS technology in flow measurement.
Material Limitations
Material selection is crucial in the design and efficacy of MEMS flow sensors. MEMS devices generally require materials that can withstand varying conditions while maintaining performance. Common materials such as silicon and polymers are used, but they have limitations. For instance, silicon may not be suitable for extreme temperature or corrosive environments, which can limit its application in certain fields.
Some materials might also not offer the strength or flexibility needed for microfabricated components. These limitations can lead to sensor failure or inaccurate readings, which ultimately compromise the sensor's reliability.
Calibration and Maintenance Issues
Calibration plays a vital role in ensuring that MEMS flow sensors provide accurate readings. However, several factors contribute to the complexities of calibration. For instance, environmental conditions and varying fluid characteristics can affect sensor output. To maintain accuracy, regular calibration is necessary, which requires time and resources.
Moreover, maintenance of MEMS flow sensors poses its own challenges. The microcomponents are sensitive and may degrade over time. They may require careful handling during installation and maintenance, contributing to an increase in operational expenses. Ensuring long-term reliability without excessive maintenance can be a challenge for engineers.
Cost of Development
The development costs associated with MEMS flow sensors can be significant. While the sensors offer advantages, the initial investment in research, development, and production can deter many organizations from adopting this technology.
The intricate microfabrication processes often demand advanced technology and expertise, leading to higher costs. Additionally, the cost of materials, equipment, and skilled labor contributes to the overall financial burden. This expense raises concerns, particularly for small to medium enterprises looking to implement MEMS flow sensors into their operations.
In summary, addressing these challenges is essential for promoting the wider application of MEMS flow sensors. A holistic understanding and continuous innovation can help overcome limitations, offering better solutions and enhancing the adoption rate across various industries.
"Membrane fabrication and material selection are pivotal in determining the reliability and functionality of MEMS devices in fluid measurements."
Future Prospects for MEMS Flow Sensors
The future prospects for MEMS flow sensors are broad and intriguing. As industries evolve, there is a growing demand for more precise and efficient sensing technologies. MEMS flow sensors can play a critical role in this evolution. They are at the intersection of micro-scale technology and fluid dynamics, thus making them highly suitable for a variety of applications. In particular, advancements in microfabrication techniques and integration with IoT technologies will set the foundation for these sensors' future development.
Advancements in Microfabrication
Recent developments in microfabrication techniques have significantly enhanced the ability to produce MEMS flow sensors with complex geometries and tailored functionalities. Techniques like deep reactive ion etching and micro-molding allow for new designs that improve sensitivity and responsiveness. These advancements enable the production of smaller, more efficient sensors that maintain high accuracy. With new materials such as graphene and advanced polymers, the performance of MEMS sensors can reach unprecedented levels. Moreover, research into new fabrication methods can lead to reduced manufacturing costs, thus promoting wider adoption.
Integration with IoT
The integration of MEMS flow sensors with IoT systems presents a paradigm shift in how data is collected and utilized. By connecting sensors to the internet, real-time monitoring and data analysis become feasible. This opens up numerous possibilities in smart cities, healthcare, and industrial automation. For instance, real-time flow monitoring can enhance water management systems, helping to prevent leaks and optimize usage. Additionally, with the capability to analyze large data sets, predictive maintenance can be implemented, leading to significant operational improvements. In this regard, MEMS flow sensors are poised to become essential components of smart ecosystems.
Enhancements in Performance Metrics
Enhancements in performance metrics for MEMS flow sensors are crucial for their competitive edge. Improvements in measurement accuracy, sensitivity, and response time will dictate their effectiveness in various applications. Research into novel sensing mechanisms and materials aims to push the boundaries of what these sensors can achieve. For instance, techniques that leverage machine learning algorithms can optimize data interpretation, making sensors smarter.
In summary, as advancements continue, MEMS flow sensors are expected to not only enhance existing applications but also pave the way for entirely new uses across multiple industries.
"The future of MEMS flow sensors lies in their ability to adapt and integrate with emerging technologies, enhancing their significance in a digital world."
The effort to cultivate these technologies will likely yield improvements that extend far beyond the traditional realms of fluid measurement.
Finale
The conclusion of this article serves as a vital component in encapsulating the discussed elements surrounding MEMS flow sensors. It is important because it not only synthesizes the information throughout the document but also highlights the implications that can be drawn from the findings. MEMS flow sensors epitomize a remarkable advancement in sensor technology, demonstrating versatility across various applications including healthcare, automotive, and environmental monitoring.
Summary of Key Points
In this section, we summarize the essential points presented in the article:
- Definition and Overview: MEMS flow sensors are miniaturized devices employing micro-electromechanical systems to measure fluid flow with precision.
- Technical Principles: The underlying mechanisms, such as the Coriolis effect and capacitive sensing, provide insights into how these sensors operate effectively.
- Applications: Their utility spans numerous industries, showcasing their adaptability in modern technology.
- Advantages: Characteristics like compact size, high sensitivity, and low power consumption make MEMS flow sensors an excellent choice in many settings.
- Challenges: There are ongoing discussions concerning material limitations, calibration, maintenance, and costs associated with development.
- Future Prospects: Advancements in microfabrication techniques and integration with IoT technologies promise further improvements in the performance metrics of these sensors.
By consolidating these key elements, we underscore the pivotal role MEMS flow sensors will play in shaping future technologies and industries.
Implications for Future Research
Looking forward, the implications for future research in MEMS flow sensors are significant. Key areas to consider include:
- Microfabrication Advancements: Ongoing research into microfabrication methods will influence the development processes, potentially leading to more cost-effective and reliable sensors.
- Integration with IoT: As the Internet of Things continues to expand, the integration capabilities of MEMS flow sensors will be essential in automating data collection and improving efficiency in various applications.
- Performance Metrics: Future studies may focus on enhancing the sensitivity, accuracy, and response times of MEMS flow sensors to meet the growing demands of the industry.
This exploration into MEMS flow sensors is just at the beginning. Continued research will likely yield innovations that further refine this technology, addressing current limitations and unlocking new opportunities. The insights gained here set a foundation for future inquiries and applications.