Exploring the Landscape of Chemical Machinery
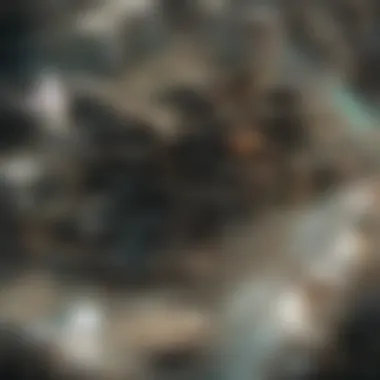
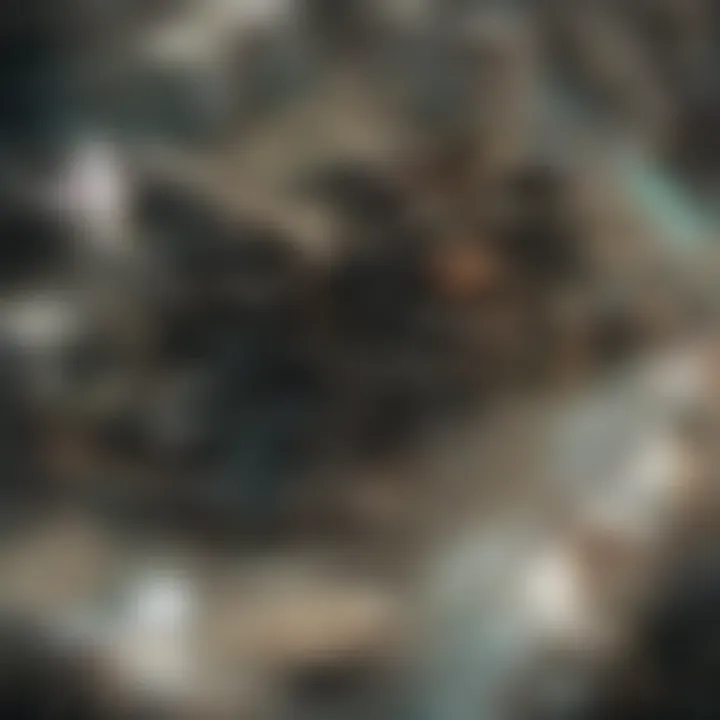
Intro
The field of chemical machinery is pivotal to modern industry. It includes a range of equipment and systems used for the processing of chemicals. As industries grow, the need for efficient and safe machinery becomes increasingly significant. This piece will dissect the landscape surrounding chemical machinery, examining its definitions, types, and roles in various sectors.
Chemical machinery not only plays a crucial part in manufacturing processes but also intersects with technological advancements and environmental sustainability. Understanding this domain is essential for students, researchers, and professionals alike.
Through this article, readers will gain insights into the operational frameworks, maintenance standards, and safety protocols integral to the industry. Furthermore, upcoming trends and innovations will be spotlighted, revealing how chemical machinery is adapting to environmental considerations.
As we embark on this exploration, we will unfold the nuances of chemical machinery, detailing its complexities in an engaging and informative manner.
Prologue to Chemical Machinery
Chemical machinery represents a crucial segment of modern industrial processes. It is the backbone of operations in various sectors such as pharmaceuticals, petrochemicals, and food production. Understanding chemical machinery is imperative for both efficiency and safety in these industries. Today’s sectors rely on complex systems that not only streamline operations but also enhance product quality. This introduction aims to highlight the relevance of chemical machinery in industry and its evolution over time.
Definition and Relevance
Chemical machinery refers to equipment and systems used in chemical processes. This includes devices for mixing, reacting, separating, and transferring materials. The relevance of these machines extends beyond mere operation. They help maintain product consistency, reduce waste, and improve safety standards. As industrial demands increase, the role of chemical machinery becomes more pronounced. Businesses continually seek innovations that increase productivity while adhering to environmental regulations.
Historical Context
The history of chemical machinery dates back to the early days of chemistry. Initially, simple devices like kettles and pots were used for basic reactions. Over time, with the industrial revolution, the development of more sophisticated machinery began. The introduction of processes such as distillation and filtration changed the landscape significantly. The advancement in materials and technology has paved the way for more efficient, durable, and safer machines. The progression illustrates not just technological advancements, but also a growing understanding of the chemical processes involved.
"The design and function of chemical machinery must evolve continuously to meet the demands of safety and efficiency in an ever-changing industrial landscape."
Understanding this journey is essential for grasping the complexities of modern chemical systems.
Categories of Chemical Machinery
The exploration of chemical machinery reveals a multifaceted structure that is essential to modern industrial processes. Understanding the categories of chemical machinery allows professionals, students, and researchers to appreciate the specific functions and applications within various sectors. Each category integrates unique mechanisms tailored to distinct tasks in chemical processing, enhancing efficiency and productivity.
Mixers and Agitators
Mixers and agitators are crucial in ensuring homogeneity in mixtures. They operate by combining different components, which can include solids, liquids, and gases. This category plays a key role in various industries such as food, pharmaceuticals, and chemicals.
Proper mixing leads to uniform reactions and ensures product quality. For example, in the food industry, consistent mixing is vital for sauces and emulsions. The design of mixers may include blades, impellers, or other means to create flow patterns that enhance blending.
Reactors
Reactors are central to chemical transformation processes. They provide the environment necessary for chemical reactions to occur. Different types of reactors exist, including batch, continuous, and semi-continuous. Each type has its specific application depending on the scale of production and the nature of the process.
The performance of a reactor is significantly influenced by factors such as temperature, pressure, and residence time. Careful design and operation of reactors can optimize yield and selectivity, crucial in industries like petrochemicals and pharmaceuticals.
Separators
Separators are essential for the purification and recovery of products after chemical reactions. They help isolate desired materials from by-products and impurities. Common methods employed by separators include filtration, centrifugation, and distillation. Each method has its advantages, depending on the physical properties of the materials being processed.
For instance, centrifuges are often used when dealing with suspensions, whereas distillation is beneficial for liquid mixtures with different boiling points. Understanding the capabilities and limitations of various separators can significantly impact the overall efficiency of production processes.
Heat Exchangers
Heat exchangers play a vital role in regulating temperature during chemical processes. They transfer heat between two or more fluids, which can be essential for either heating or cooling reactions. This category includes shell-and-tube, plate, and air-cooled designs.
Efficient heat exchange is critical for maintaining optimal reaction conditions. Moreover, it can lead to substantial energy savings. An effective heat exchanger design minimizes temperature gradients and maximizes surface area, enhancing the overall thermal efficiency of the plant.
Pumps and Compressors
Pumps and compressors are crucial for the movement of fluids and gases within chemical plants. Pumps facilitate the transfer of liquids, whereas compressors increase the pressure of gases, ensuring efficient transport throughout the facility.
Different types of pumps, such as centrifugal and positive displacement pumps, are optimized for various applications. Meanwhile, compressors can include reciprocating or rotary designs, tailored based on the requirements of pressure and flow rate in specific processes.
Understanding the operation and selection of pumps and compressors is essential for the design and maintenance of chemical machinery. Proper functioning affects not only efficiency but also safety within production environments.
"Thorough knowledge of machinery categories aids in the appropriate selection and application of equipment, thus enhancing operational success."
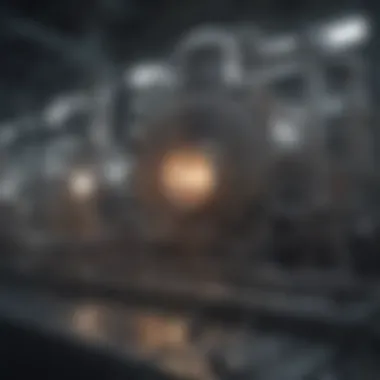
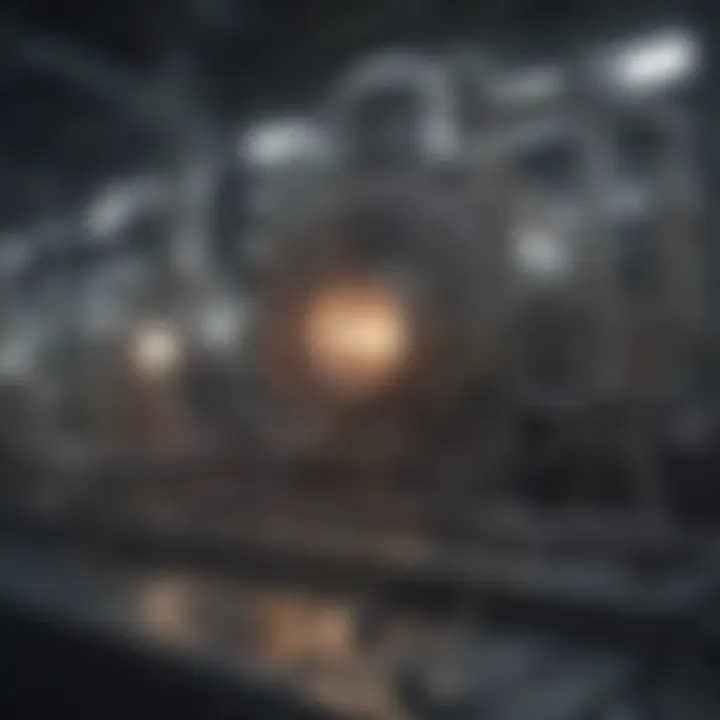
In essence, delving into the categories of chemical machinery offers insights necessary for professionals looking to improve process efficiency and product quality. The interplay between mixers, reactors, separators, heat exchangers, pumps, and compressors fosters an environment where industrial operations can thrive.
Operational Mechanisms
Understanding operational mechanisms is essential in the chemical machinery sector. This aspect lays out how machinery functions and interacts within industrial settings. Efficient operation ensures high productivity, safety, and reduced waste. Misunderstanding these mechanisms can lead to costly errors and safety hazards. Following are key components that define operational mechanisms.
Principles of Function
The principles of function govern how chemical machinery operates. Each piece of equipment, be it a mixer or a reactor, possesses a specific way in which it transforms raw materials into desired products. Key principles include:
- Input-Output Relationships: Understanding the flow of materials and how inputs affect outputs is paramount.
- Energy Transfer: Chemical processes often involve heat, mechanical energy, or mass transfer. An example is heat exchangers, which facilitate efficient heat management.
- Reaction Mechanisms: In reactors, the rate of chemical reactions is critical. This depends on temperature, concentration, and pressure. Monitoring these variables ensures optimal reactions.
The synergy of these principles results in improved operational efficiencies and product quality.
Integration with Automated Systems
In today’s industrial landscape, automation plays a vital role. Integrating chemical machinery with automated systems enhances precision and reduces human error. Several factors contribute to successful integration:
- Control Systems: Modern machinery utilizes advanced control systems. These systems monitor and adjust operational variables in real-time.
- Data Acquisition: Automated systems collect data that can be analyzed. This assists in decision making and troubleshooting.
- Remote Monitoring: Operators can oversee processes remotely. This capability allows for immediate response to any irregularities.
The integration of automation improves operational safety and efficiency.
Efficiency Optimization
Efficiency optimization is crucial for maintaining competitive advantages in the chemical industry. It encompasses various strategies, such as:
- Regular Maintenance: Scheduled maintenance reduces downtime and keeps machinery functioning smoothly.
- Performance Metrics: Establishing key performance metrics helps track efficiency and identify areas for improvement.
- Upgrading Technology: Investing in new technologies such as sensors and control systems enhances operational efficiency.
The following benefits arise from effective efficiency optimization:
- Reduced operational costs
- Enhanced product quality
- Improved resource management
"Performance metrics are key indicators of machinery efficiency and successful operational mechanisms."
In summary, operational mechanisms encompass principles of function, integration with automated systems, and more. Each of these components is integral to understanding how chemical machinery operates effectively in various industrial contexts.
Maintenance Practices
Maintenance practices are crucial in the realm of chemical machinery. They ensure that equipment operates safely, efficiently, and reliably. Without a proper maintenance routine, machinery is subject to wear and tear that can lead to costly downtimes and accidents. The three key components of maintenance practices include routine inspections, troubleshooting techniques, and replacement of parts. Together, they form a framework that aids in sustaining operational integrity and longevity of chemical equipment.
Routine Inspections
Routine inspections are essential for identifying potential issues before they escalate. Through regular checks, operators can assess the condition of mixers, reactors, separators, and other key machinery. Inspections often involve assessing fluid levels, examining physical wear, and checking for leaks. Effective inspections require a clear checklist and an understanding of machinery specifics. The use of technology, such as sensors and control systems, enhances this process.
Benefits of routine inspections include:
- Early detection of problems: Identifying issues promptly can prevent catastrophic failures.
- Performance optimization: Continuous monitoring contributes to more efficient operations.
- Consistency in output: Regular checks help maintain product quality by ensuring equipment functions within specifications.
Troubleshooting Techniques
Troubleshooting techniques are vital when issues arise during operation. Effective troubleshooting involves systematic investigation to identify the root cause of malfunction. Common methods include:
- Checking for error messages from control systems.
- Verifying connections and mechanical integrity.
- Analyzing performance data to detect anomalies.
It is crucial for personnel to be well-trained in these techniques. False assumptions can lead to unnecessary repairs or further safety hazards. Troubleshooting not only resolves immediate issues but also provides insights for future improvements.
Replacement of Parts
The replacement of parts is a fundamental aspect of maintenance. Over time, components of chemical machinery may degrade or fail. This replacement process requires careful planning and execution to ensure minimal disruption.
Key considerations include:
- Scheduling replacements: Regularly scheduled replacements based on operating hours or condition monitoring can reduce unexpected failures.
- Quality of replacement parts: Using certified parts guarantees compatibility and maintains safety standards.
- Documentation: Keeping records of replaced parts helps track machinery health and informs future maintenance strategies.
Proper maintenance practices are not only about extending the life of equipment but also enhancing the safety and efficiency of chemical operations.
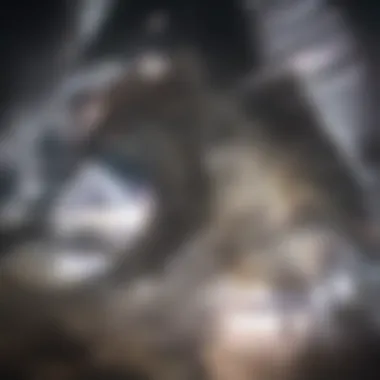
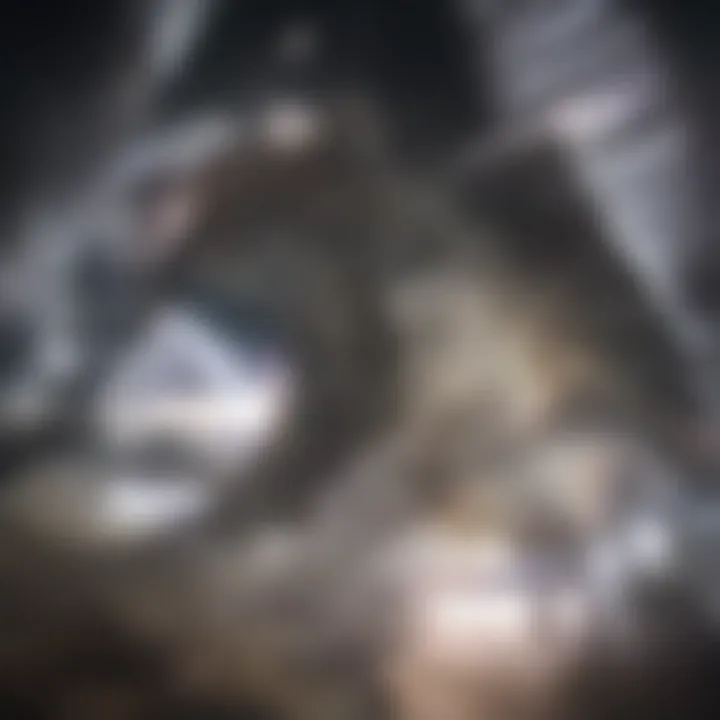
In summary, effective maintenance practices are vital for the sustainability and reliability of chemical machinery. Through routine inspections, troubleshooting techniques, and timely replacement of parts, industries can maintain high standards of operational safety and efficiency.
Safety Protocols in Chemical Operations
Safety protocols are an essential aspect of chemical operations. They help ensure that workers, the environment, and the surrounding community are protected from the risks associated with handling hazardous materials. Adhering to these protocols not only complies with regulations but also fosters a culture of safety within the industry. This section highlights the significant elements, benefits, and considerations surrounding safety protocols in chemical operations.
Risk Assessment Procedures
Risk assessment procedures are fundamental to identifying potential hazards in chemical operations. This process involves the systematic evaluation of activities, materials, and equipment to determine what could go wrong. By assessing the likelihood and impact of specific risks, organizations can implement control measures to mitigate them.
A thorough risk assessment comprises several steps:
- Hazard Identification: Recognizing and listing all possible hazards that could arise during operations.
- Risk Analysis: Evaluating the potential consequences and likelihood of each hazard occurring.
- Risk Evaluation: Prioritizing risks based on their severity and the level of control already in place.
- Control Measures: Developing strategies to minimize or eliminate identified risks, such as engineering controls, administrative measures, and personal protective equipment.
Implementing regular risk assessments ensures that safety protocols remain up-to-date and effective. It also helps to cultivate an awareness of safety among staff, leading to a proactive approach to risk management.
Emergency Response Plans
Emergency response plans are designed to prepare organizations for potential incidents that may occur in chemical operations. These plans outline immediate and effective responses to various emergency scenarios, including chemical spills, fires, and equipment failures. An effective emergency response plan can significantly reduce the impact of accidents and protect people and the environment.
Key components of an emergency response plan include:
- Clear Roles and Responsibilities: Outline who is responsible for what during an emergency.
- Communication Protocols: Establish clear lines of communication to alert necessary personnel and emergency services promptly.
- Evacuation Procedures: Design routes and processes for safely evacuating personnel from hazardous areas.
- Training and Drills: Regular training and drills to ensure staff are familiar with emergency procedures and can act swiftly.
Having a robust emergency response plan in place underscores the commitment to safety in chemical operations. It empowers employees, allowing them to respond effectively in case of emergencies.
"The presence of well-structured safety protocols is not merely a regulatory compliance issue; it is a core component of operational integrity and sustainability in chemical industries."
The Impact of Regulations
The landscape of chemical machinery is significantly shaped by regulations, making this aspect crucial for industry stakeholders. Regulations are not merely guidelines; they form the foundation for safe and efficient operations within chemical processes. Understanding the impact of regulations can drive compliance, enhance operational protocols, and ensure the safety of personnel and the environment.
Local and International Standards
Regulatory standards vary widely across different regions. Local regulations often prioritize community safety and environmental protection. These laws typically dictate how chemical machinery should be designed, operated, and maintained. For instance, the Environmental Protection Agency (EPA) in the United States imposes strict guidelines on emissions and waste disposal, pushing industries to adopt cleaner technologies.
International standards, on the other hand, aim to harmonize practices across borders. Organizations such as the International Organization for Standardization (ISO) establish protocols that apply to multiple countries. The ISO 14001 standard focuses on effective environmental management systems, ensuring that chemical operations meet global benchmarks. These standards help integrate sustainable practices into chemical machinery operations, leading to broader ecological benefits.
Compliance Challenges
While regulations are vital, they also pose significant challenges. Many companies struggle to keep pace with the evolving landscape of compliance requirements. This complexity is compounded by the need for continuous monitoring and assessment of equipment. Furthermore, regulations can change frequently, which necessitates urgent adaptations in operational practices.
Companies often face resource constraints in implementing compliance measures effectively. This can lead to increased operational costs or even penalties for non-compliance. It is essential for businesses to invest in training and technology that supports adherence to regulations. Regular audits and updates to compliance strategies can mitigate these challenges.
"Adhering to regulations will not only protect the environment but also enhance the reputation and operational efficiency of chemical manufacturing businesses."
In summary, regulations play a critical role in shaping chemical machinery operations. Understanding local and international standards is vital. Addressing compliance challenges with proactive measures can lead to improved safety and environmental stewardship.
Environmental Considerations
The significance of environmental considerations within chemical machinery cannot be overstated. As industries continually advance, the need to integrate sustainable practices in chemical processes has become apparent. This section examines the pertinent aspects of environmental considerations, particularly focusing on two key areas: waste management practices and the overall sustainability of chemical machinery.
Waste Management Practices
Effective waste management is essential in minimizing the environmental impact of chemical operations. Chemical plants produce a variety of waste, including hazardous and non-hazardous materials. Meticulous waste management strategies can significantly reduce water and air pollution, ensuring compliance with environmental regulations.
Important waste management practices include:
- Source Reduction: By altering processes or materials to minimize waste generation from the outset. This can involve re-evaluating chemical formulas or improving theoretical yields.
- Recycling and Reuse: Implementing systems to reclaim useful materials from waste streams. This reduces overall waste and can lower material cost.
- Destruction Technologies: Utilizing incineration or other methods to safely dispose of hazardous waste, reducing its potential environmental threat.
- Monitoring and Reporting: Regularly assessing waste generation and management efforts can help in identifying areas for improvement and ensuring compliance with relevant environmental regulations.
In summary, effective waste management not only mitigates environmental harm but also promotes operational efficiency and financial savings.
Sustainability and Chemical Machinery
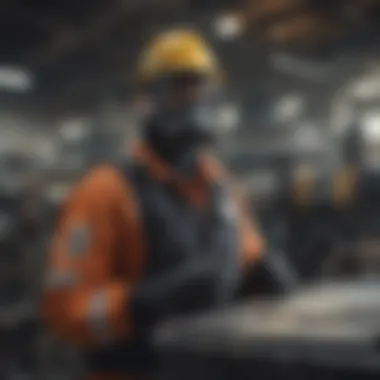
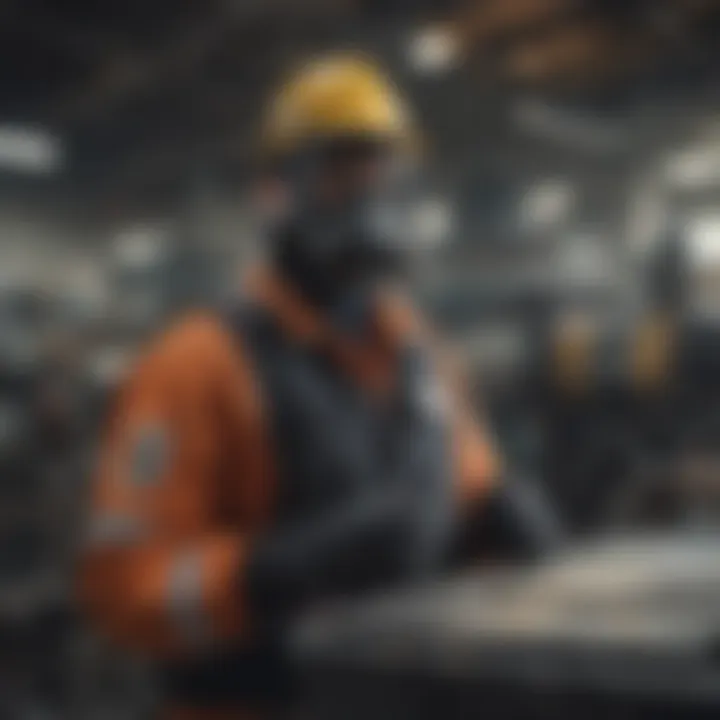
Sustainability in the field of chemical machinery encompasses strategic decisions made by firms aiming to preserve natural resources while maintaining productivity. This commitment to sustainable practices includes choosing the right machinery and processes that minimize resource use and waste generation. Some essential sustainability aspects include:
- Energy Efficiency: Utilizing energy-efficient machinery can substantially lower operational costs. This involves the adoption of advanced technologies, such as variable frequency drives and highly efficient heat exchangers.
- Green Chemistry Principles: Integrating principles of green chemistry can lead to the development of processes that reduce or eliminate hazardous substances. This not only serves the environment but can also enhance product safety.
- Lifecycle Assessment (LCA): An LCA approach allows companies to evaluate the environmental impact of their processes from production through disposal. Understanding a product’s entire lifecycle can guide improvements and innovations.
By focusing on sustainability, companies can ensure they meet contemporary challenges while remaining competitive in their industries. The transition to sustainable practices is not merely a trend; it is a necessity for the longevity and success of chemical operations in the future.
Sustainability in chemical machinery is not only beneficial for the environment but also presents economic advantages and improved social responsibility.
Future Trends in Chemical Machinery
The field of chemical machinery is ever-evolving, influenced by numerous advances in technology and changes in industrial practices. Recognizing future trends is crucial not only for adapting to innovations but also for ensuring sustainability and efficiency in operations. Companies that stay informed about these trends can gain a competitive edge and contribute to safer, more environmentally friendly practices.
Advancements in Automation and AI
Automation and artificial intelligence (AI) are reshaping the landscape of chemical machinery. With increased automation, routine tasks that were once performed manually are now carried out by precision machinery and software. This transition reduces the potential for human error, enhances consistency, and improves overall productivity.
AI integration allows for more complex data analysis. Machine learning algorithms can predict equipment failures before they occur. This predictive maintenance minimizes downtime and extends the lifespan of equipment. Moreover, AI-driven systems enable real-time monitoring of chemical processes, allowing for immediate adjustments. As functions become automated, operators can focus on strategic decision-making rather than daily operational tasks, increasing overall efficiency.
Emerging Technologies
Emerging technologies are transforming chemical machinery with innovative capabilities. One significant development is the rise of IoT (Internet of Things) devices. These devices enable machinery to communicate seamlessly with other machines and operators through a centralized network. By gathering data on performance and efficiency, industries can optimize operations based on real-time insights.
Additionally, advanced materials are emerging in the manufacturing of machinery. Lightweight and corrosion-resistant materials allow for more durable and energy-efficient designs. This evolution leads to reduced resource consumption and better environmental outcomes.
"The continual progress in automation and technology signals a shift towards intelligent and sustainable chemical machinery."
The trends discussed above highlight the importance of adaptability in the face of change. Whether it be the integration of smart systems or the materials used in production, embracing innovation is essential for the industry's future.
For further insights, visit Wikipedia or Britannica.
Case Studies
Case studies play a crucial role in understanding the practical applications of chemical machinery across various industries. They offer real-world insights that complement theoretical knowledge, thereby bridging the gap between academic learning and industrial practice. Through detailed exploration of specific cases, one can appreciate how machinery performs in different environments and under various operational conditions.
One significant benefit of case studies is their ability to showcase the effectiveness of particular machines in actual production processes. By analyzing how mixers, reactors, or heat exchangers function in specific scenarios, researchers and professionals alike can identify best practices, recognize common challenges, and develop solutions tailored to those challenges.
Moreover, case studies let us analyze the decision-making processes behind machinery selection and integration. Factors such as cost-effectiveness, energy consumption, and maintenance requirements are often pivotal in choosing the right type of machinery, and these elements can be understood better through focused geographical or operational contexts.
Industry Applications
The application of chemical machinery is vast, spanning several sectors. For instance, in the pharmaceutical industry, chemical reactors are integral to the production of essential medicines. An example is the use of continuous flow reactors for the synthesis of active pharmaceutical ingredients (APIs). These reactors simplify the process and enhance yield, thus directly impacting drug availability and cost.
Agricultural chemicals often rely on mixers specifically designed to handle abrasive materials. Companies like Bayer implement state-of-the-art mixing technology to ensure homogeneity in their products. This directly translates to better performance in the field, securing a reliable supply chain and customer satisfaction.
In the food industry, heat exchangers are critical in pasteurization processes. Brands such as Tetra Pak utilize this machinery efficiently to ensure food safety standards are met while conserving energy. Understanding their case studies informs future designs of heat exchangers to further optimize efficiency and reduce environmental impact.
Lessons Learned
One of the most significant lessons derived from case studies is the importance of adaptability in machinery design. Industries face unique challenges, and machinery must evolve to meet these. For example, the increasing demand for energy-efficient solutions has led to innovations in pump technology. Companies have learned to prioritize energy consumption metrics alongside performance specifications when choosing equipment.
Another lesson is the necessity of ongoing maintenance and inspections. Failures in machinery can lead to costly downtimes. Case studies often highlight organizations that adopted predictive maintenance strategies, demonstrating the advantages of monitoring systems that provide early warnings about potential issues.
Lastly, case studies underscore the relevance of safety protocols within chemical machinery operations. Incidents that may have been prevented through stricter adherence to safety guidelines serve as crucial reminders. Organizations that prioritize safety in machinery operation show improved employee morale and lower accident rates, ultimately leading to a more effective and sustainable operation.
"Understanding the practical application of case studies not only helps in decision-making but also enhances operational efficiency and safety within industries using chemical machinery."
Reflecting on the insights gained from case studies equips professionals with the knowledge needed to navigate future developments in chemical machinery more adeptly.
The End
The conclusion of this article serves to underscore the importance of chemical machinery in various industrial settings. Throughout the discussion, readers gain insight into the essential functions and operational mechanisms that drive this field. Each section highlights key components and considerations that are vital to optimizing processes and ensuring safety in chemical operations.
Summary of Key Points
Chemical machinery encompasses diverse equipment crucial for mixing, reacting, separating, heating, and pumping materials in industrial chemistry. Understanding the historical context provides a baseline for appreciating advancements seen today. Regular maintenance practices and adherence to safety protocols are not merely recommendations; they are essential to prevent accidents and ensure operational efficiency.
Moreover, compliance with local and international regulations informs how companies manage their practices. Environmental considerations, especially waste management and sustainability, illustrate the industry's shifts toward more responsible operations. Future advancements in automation and AI promise to reshape the landscape further, enhancing efficiency and safety through innovative technologies.
"Understanding the complex interplay of chemical machinery can lead to significant improvements in production efficiency and safety, thus benefiting the entire industry."
The Future Outlook
Looking ahead, the future of chemical machinery is intertwined with technological innovations. As industries prioritize automation, tools such as AI can analyze data more effectively, leading to improved decision-making processes. Predictive maintenance powered by machine learning algorithms can significantly reduce downtime and extend equipment lifespan.
Sustainability practices will also become increasingly significant. Industries will likely adopt greener technologies, focusing on reducing waste and minimizing environmental impact. Collaborative research between industrial practices and academia may drive new solutions and methodologies.