3D Printed Titanium: Innovations and Industry Impact
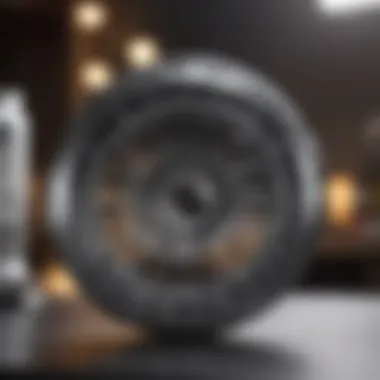
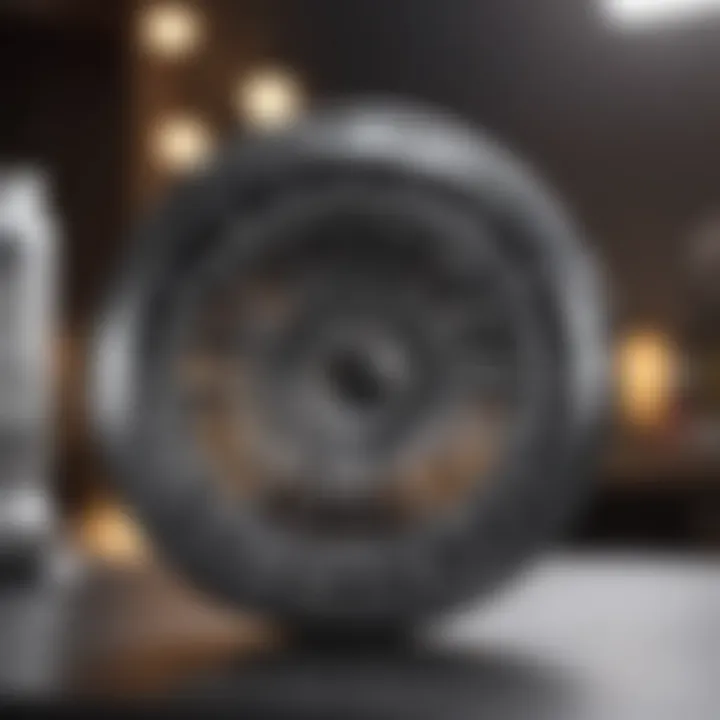
Intro
The advancements in 3D printing technology have significantly changed various industries, especially through the use of titanium. Titanium and its alloys have long been recognized for exceptional properties such as high strength-to-weight ratio, corrosion resistance, and biocompatibility. These attributes make titanium an ideal material for a wide range of applications, from aerospace to medical and automotive sectors. The ability to 3D print titanium not only enhances design options but also optimizes production efficiency.
This article will delve into the intricate details surrounding 3D printed titanium, providing a robust understanding of its manufacturing processes, material properties, and applications across diverse industries. By exploring the innovations in additive manufacturing, its relevance in real-world applications will be highlighted, alongside the potential future implications of this technology.
Research Overview
Summary of Key Findings
Recent research indicates that 3D printed titanium offers considerable advantages over traditional manufacturing techniques. The ability to create complex geometries and lightweight structures can lead to enhancements in performance and reduced material waste. Industries that have adopted this technology, such as aerospace, medical, and automotive, reap benefits from improved design flexibility and production speeds. The use of titanium enhances component durability and reliability, especially in high-stress environments.
Methodologies Employed
The methodologies involved in studying 3D printed titanium often include experimental analysis, computational modeling, and comparative studies. Using advanced equipment and analysis techniques, researchers assess the material properties, such as tensile strength and fatigue resistance. Such investigations help to ensure that the produced components meet or exceed industry standards. Furthermore, simulation tools can predict how components will behave under various conditions, allowing for optimization before physical manufacturing takes place.
In-Depth Analysis
Detailed Examination of Results
The results from various studies demonstrate consistent advantages of 3D printed titanium components. For example:
- Weight Reduction: Aerospace applications have reported weight reductions of over 50% when using 3D printed titanium parts. This capability leads to decreased fuel consumption and improved efficiency.
- Customization: Medical implants made with 3D printed titanium can be tailored to fit the specific anatomical requirements of patients, leading to improved outcomes.
- Reduced Lead Time: The time taken to develop prototypes and finished products has considerably decreased, allowing companies to respond more swiftly to market demands.
Comparison with Previous Studies
When comparing the findings of current studies to previous research, substantial progress is evident. Traditional methods of titanium manufacturing are often costly and time-consuming. Conversely, recent studies reflect a paradigm shift where 3D printing not only reduces costs but also minimizes production times. This evolution reveals a tendency towards more sustainable practices, as waste material generated during production significantly drops in additive manufacturing processes.
"The shift towards 3D printing titanium is not merely a trend; it is a fundamental change in how industries approach manufacturing and design."
Prelims to 3D Printed Titanium
3D printed titanium represents a remarkable convergence of advanced manufacturing techniques and material science innovation. This emerging field is reshaping varied industries through its ability to produce complex, lightweight structures with high performance. Understanding this section lays the groundwork for appreciating not only the advancements in technology but also the broad applications of titanium across sectors like aerospace, medical, and automotive.
Definition and Overview
3D printed titanium refers to the process of creating titanium components layer by layer using additive manufacturing techniques. With a unique capability to fabricate intricate designs, it offers significant flexibility compared to traditional machining processes. The titanium powder is sintered or melted using lasers or electron beams, forming solid structures that retain the material’s advantageous properties.
In addition to the production capabilities, 3D printing allows for material efficiency, as it minimizes waste by using only the necessary amount of titanium powder. This efficiency, combined with the strength-to-weight ratio of titanium, makes it appealing to industries that require durable yet lightweight parts.
Historical Context
Titanium gained attention in the mid-20th century, primarily for its strength-to-weight ratio and corrosion resistance. Initial applications were observed in aerospace, where its mechanical properties made it ideal for flight components. With time, these favorable characteristics led to explorations in 3D printing, which began to take shape in the 1980s with the advancement of laser sintering techniques.
The evolution of 3D printing technology greatly enhanced the potential applications of titanium. By the 2000s, companies began to explore ways of merging titanium with additive manufacturing to enable custom solutions in design and production. Today, the industry celebrates a rich history that combines materials science and innovative technology, paving the way for extensive applications in various sectors.
"The intersection of titanium and 3D printing is not merely a trend; it is fundamentally changing how we approach design and manufacturing in industry."
The historical timeline illustrates not only the growing capabilities in 3D printing technology but also the escalating recognition of titanium’s properties, positioning it as a material of choice for complex and critical applications.
Understanding Titanium
Titanium is an essential material in the landscape of advanced manufacturing, particularly in the context of 3D printing. It holds a unique position due to its combination of strength, lightweight properties, and corrosion resistance. Understanding titanium enables industries to harness its capabilities effectively and create components that push the boundaries of current technology.
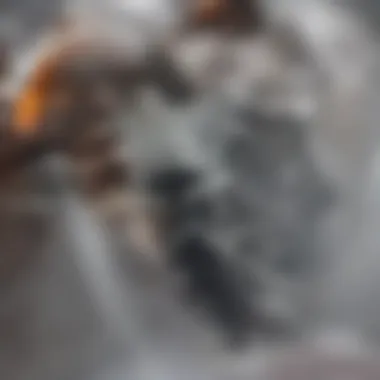
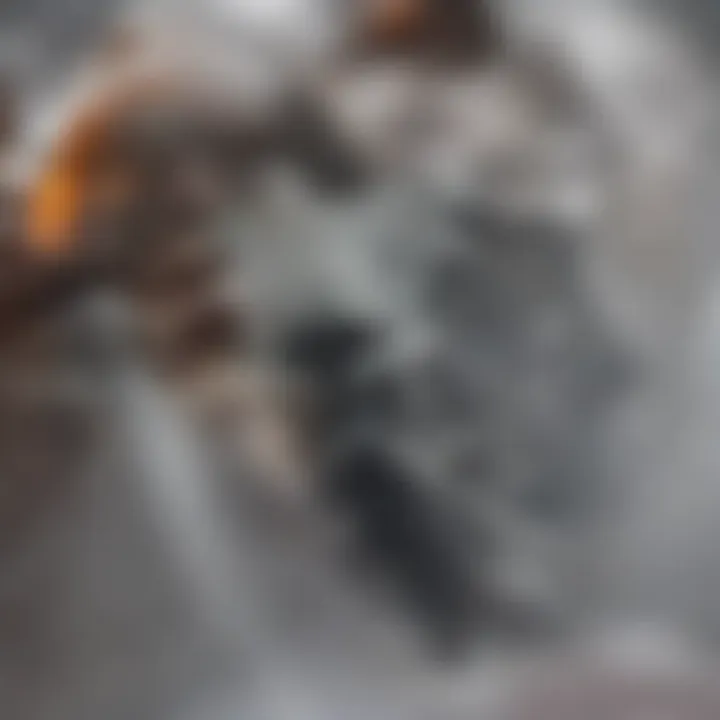
Chemical and Physical Properties
Titanium has several notable chemical and physical properties that make it particularly valuable. Its atomic number is 22, and its density is about 4.5 g/cm³, which is significantly lower than other metals like steel, yet it offers comparable strength.
- Strength-to-Weight Ratio: Titanium boasts a high strength-to-weight ratio. This means it can be used in applications where both weight savings and structural integrity are critical. For example, many aerospace components are made from titanium because small reductions in weight can lead to significant fuel savings.
- Corrosion Resistance: Titanium is highly resistant to corrosion. This is especially useful in medical implants and marine applications, where exposure to harsh environments is common.
- Temperature Stability: The metal remains stable over a broad temperature range. It retains its properties in extreme conditions, making it suitable for both high and low-temperature applications.
- Biocompatibility: In medical applications, titanium is known for its biocompatibility, meaning it can coexist with living tissues without eliciting an immune response. This property makes it an excellent choice for implants and prosthetics.
Understanding these properties is crucial in determining how titanium can be utilized in various industries, especially as the technology behind 3D printing evolves.
Advantages of Titanium as a Material
The advantages of titanium extend beyond its inherent physical properties. Here are some key benefits that make it a preferred material in many applications:
- Durability: Titanium components exhibit remarkable durability and longevity compared to alternative materials. This provides value in terms of reduced maintenance and replacement costs.
- Machinability: While titanium can be challenging to machine, advances in technology have improved its processability. Techniques such as 3D printing allow for more complex shapes and forms that traditional methods might not achieve.
- Design Flexibility: The additive manufacturing processes used in 3D printing titanium open possibilities for designs that were previously infeasible. This leads to innovation in component design and manufacturing processes.
- Economic Efficiency: Although initially costly, the long-term economic benefits often justify the investment in titanium components. Considering factors like reduced weight and the longevity of products, companies can see a favorable return on investment.
In summary, a thorough understanding of titanium’s chemical and physical properties, alongside its advantages as a material, allows engineers and manufacturers to innovate and utilize this metal effectively in various applications. As industries continue to adopt 3D printing technologies, titanium's role will only expand.
3D Printing Techniques
3D printing techniques are crucial in understanding the production of titanium parts, driving innovation in manufacturing across various sectors. The development and refinement of these processes have influenced not only the efficiency of production but also the quality and functionality of titanium components. It leads to significant cost reductions and the ability to create geometrically complex designs that are often not feasible with traditional manufacturing methods.
Furthermore, these processes allow for rapid prototyping, which is a key factor in modern engineering and design. Companies can iterate designs more quickly, leading to faster product development cycles. This agility becomes especially important when addressing the evolving demands of the aerospace, medical, and automotive industries.
Additive Manufacturing Processes
Additive manufacturing refers to a set of techniques that build components layer by layer from a digital model. In this realm, various processes are leveraged when working with titanium. Each method offers unique benefits and specific applications depending on the requirements of the final product.
One major advantage of additive manufacturing is its ability to reduce material waste. Traditional subtractive methods often result in significant material loss, whereas additive techniques utilize only the material necessary for the part, leading to more sustainable practices.
Key additive manufacturing processes include:
- Selective Laser Melting (SLM): A high-powered laser melts titanium powder to create the part layer by layer. This method is widely used for complex geometries.
- Electron Beam Melting (EBM): This process utilizes an electron beam under vacuum conditions to fuse titanium powder. It is known for producing higher density parts.
- Binder Jetting: This method involves depositing a binding agent onto layers of titanium powder, followed by sintering to achieve solid parts. It allows for faster production times.
The choice of manufacturing process can significantly impact mechanical properties and performance of the finished product. Choices may vary based on part complexity, volume of production, and specific titanium alloys used.
Powder Bed Fusion vs. Directed Energy Deposition
In the context of titanium, two prominent 3D printing techniques are Powder Bed Fusion and Directed Energy Deposition. Both processes have distinct methodologies, advantages, and applications.
Powder Bed Fusion involves spreading a layer of titanium powder over a build platform, after which a laser or electron beam selectively fuses the powder. This process allows for intricate designs with high precision. It is typically used in aerospace applications where component performance is critical. The resulting parts often exhibit superior mechanical properties due to the controlled cooling and solidification processes involved.
On the other hand, Directed Energy Deposition uses a focused heat source, such as a laser or electron beam, to melt metal powder or wire feedstock as it is deposited on the substrate. This technique enables repair and add-on manufacturing, making it suitable for applications in the aerospace and medical fields where refurbishing parts is necessary. This method presents the advantage of faster production rates for larger components but can sometimes lead to less intricate geometries compared to Powder Bed Fusion.
"The choice between Powder Bed Fusion and Directed Energy Deposition significantly impacts the design possibilities and material properties of titanium parts produced through 3D printing."
In summary, understanding these additive techniques is essential for leveraging the full potential of 3D printed titanium. Both approaches offer unique advantages, contributing to the growing trend of titanium applications in high-performance industries.
Manufacturing Workflow
The manufacturing workflow of 3D printed titanium is a critical aspect that influences the overall quality, efficiency, and profitability of producing titanium components. This workflow encompasses several key steps, including design considerations, the actual printing process, and subsequent post-processing techniques. Understanding each element can lead to improved design efficiency and cost-effectiveness while ensuring high-quality outputs.
Design Considerations
When embarking on the design phase for 3D printed titanium parts, several factors must be evaluated. Here are some significant considerations:
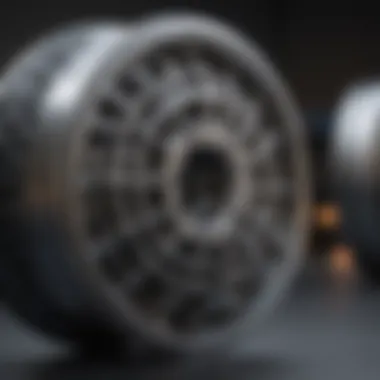
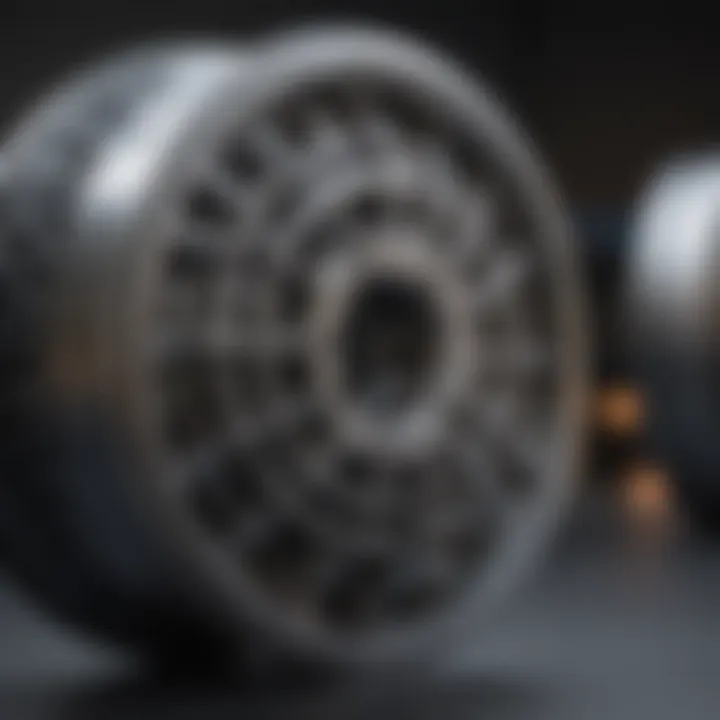
- Geometric Complexity: 3D printing allows for intricate designs that are difficult or impossible to achieve with traditional manufacturing methods. Designers should exploit this advantage.
- Weight Reduction: Titanium’s strength-to-weight ratio is favorable. Design elements that minimize weight can result in better performance, especially in industries like aerospace and automotive.
- Thermal Expansion: It is crucial to consider how titanium responds to heat during the printing process. The thermal characteristics might affect the part's final shape and structural integrity.
- Material Orientation: The orientation of the part in the printer can significantly influence mechanical properties and surface finish. This step requires careful planning and can lead to improved performance of the final product.
A well-thought-out design can help avoid issues during the printing phase, ensuring that the desired mechanical properties are achieved. Effective communication between engineers and designers can enhance the workflow significantly.
Post-Processing Techniques
After the printing process, titanium parts often require post-processing to meet the specific requirements of final applications. Some common techniques include:
- Heat Treatment: This process enhances mechanical properties, such as tensile strength and fatigue resistance. Heat treatment is often necessary for aerospace and medical applications to ensure safety and reliability.
- Surface Finish: A smooth finish is often required for aesthetic and functional reasons. Techniques like bead blasting or chemical polishing remove imperfections and improve surface characteristics.
- Machining: Some parts may require machining to achieve tolerances or final dimensions that cannot be achieved through 3D printing alone. This includes drilling holes or creating flat surfaces.
- Quality Inspection: Ensuring parts meet quality standards generally involves techniques like X-ray inspection or CT scanning. These methods verify the integrity of the part without causing damage.
Proper post-processing not only enhances appearances but also ensures compliance with industry standards.
The integration of these techniques into the manufacturing workflow can improve part durability and performance. Understanding how each component of the workflow interacts is essential for maximizing the benefits of 3D printed titanium technology.
Applications of 3D Printed Titanium
The applications of 3D printed titanium are expansive and varied, reflecting the material's unique characteristics and suitability for demanding environments. Industries increasingly embrace this technology, enhancing product performance and driving innovation. 3D printing with titanium brings substantial benefits, especially in terms of design flexibility, material efficiency, and the ability to create complex geometries that traditional methods struggle to achieve.
Aerospace Industry
Aerospace is a prominent area where 3D printed titanium demonstrates significant advantages. The industry requires lightweight yet durable materials to improve fuel efficiency and performance of aircraft. Titanium’s high strength-to-weight ratio makes it ideal for applications in aerospace. Parts such as brackets, structural components, and engine parts can be fabricated using additive manufacturing. This reduces waste during production and shortens lead times for prototyping and final parts. Moreover, parts designed with intricate structures can result in improved aerodynamic properties, which is crucial in this field.
Medical Devices and Prosthetics
In the medical field, titanium is favored due to its biocompatibility, strength, and resistance to corrosion. 3D printing has revolutionized the manufacturing of medical devices and prosthetics. Custom implants can be designed specifically for patients, ensuring better fit and functionality. The ability to create patient-specific models reduces surgery time and improves overall patient outcomes. Products such as dental implants, orthopedic devices, and surgical instruments are now being developed using this technology, allowing for enhanced precision and personalization in healthcare.
Automotive Sector
The automotive industry is also exploring the potential of 3D printed titanium. This material allows for the production of lightweight components that can enhance vehicle performance and efficiency. Components like exhaust systems, engine parts, and brackets can be produced more efficiently. The automotive sector benefits from shortened development cycles and reduced fabrication costs. As an added bonus, the use of titanium can help in reducing the vehicle’s overall weight, thus improving fuel consumption and emissions ratings.
Marine Applications
In marine environments, where components face harsh conditions, titanium’s resistance to corrosion is highly valuable. 3D printed titanium can be implemented for parts such as fittings, valves, and structural components in ships and submarines. The manufacturing process allows for the creation of parts that meet specific design requirements while minimizing material waste. The lightweight nature of titanium is also advantageous in terms of buoyancy and overall vessel performance. As the outlook for marine engineering involves a focus on efficiency and durability, titanium continues to emerge as a pivotal material.
"The adaptability of 3D printed titanium technology across various industries speaks volumes about its transformational potential."
In summary, applications of 3D printed titanium are not just limited to one area or sector. The aerospace, medical, automotive, and marine industries showcase the material's versatility and importance in advancing technology and improving product offerings. As this technology continues to evolve, further possibilities and improvements are likely to emerge, making it an exciting field for research and investment.
Economic Implications
The economic implications of 3D printed titanium are significant in today’s rapidly evolving manufacturing landscape. This section illustrates not only the cost factors related to 3D printing but also the potential economic benefits that industries can gain through its adoption. Understanding these elements is crucial for stakeholders as they consider investments in new technologies and processes.
Cost Analysis of 3D Printing
The cost analysis of 3D printing titanium involves a thorough examination of various factors affecting overall expenses. The initial investment in 3D printing equipment and materials can be high, particularly for advanced machines that utilize selective laser melting or electron beam melting. However, it is essential to evaluate these costs against the long-term savings and productivity gains that can be achieved.
- Material Costs: Titanium is a relatively expensive material, but the properties it offers, such as strength-to-weight ratio and corrosion resistance, often justify the expenditures. Traditional methods of titanium machining can result in significant waste, whereas 3D printing is an additive process, meaning less material is wasted.
- Production Speed: The speed at which components can be produced often leads to shorter lead times than traditional manufacturing methods. For industries that rely on rapid prototyping or time-sensitive projects, this can lead to a compelling cost advantage.
- Labor Costs: 3D printing can reduce the need for extensive labor involvement in the manufacturing process. Automated systems can streamline operations, which reduces labor expenses while maintaining high-quality production standards.
Consequently, the total cost of ownership may reveal that, over time, 3D printing offers a more economically viable pathway for manufacturing titanium components compared to conventional methods.
Return on Investment for Industries
The return on investment (ROI) for industries utilizing 3D printed titanium can be substantial. Companies must consider various factors that can lead to economic gains, including:
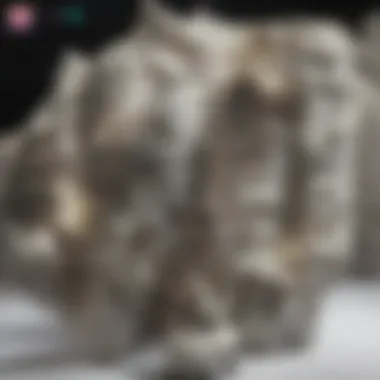
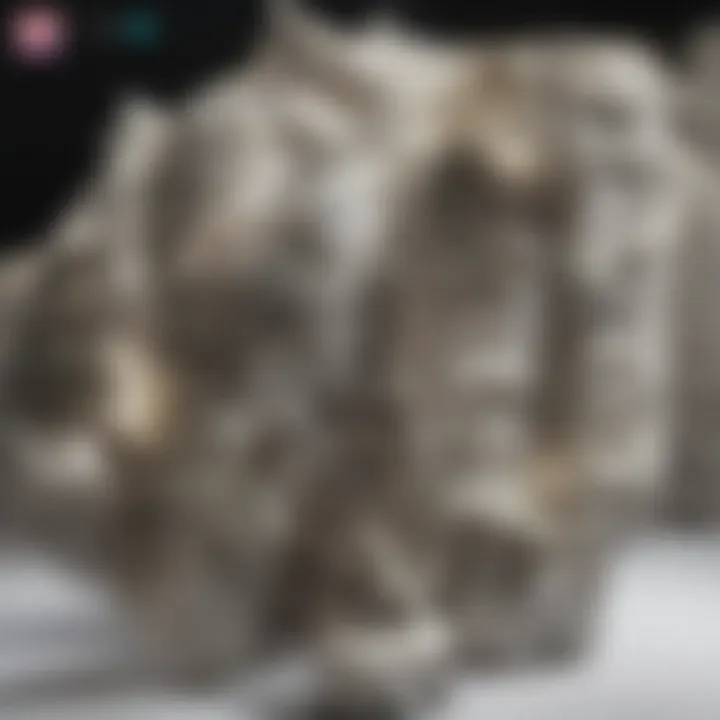
- Customization and Flexibility: 3D printing allows for the rapid adjustment of designs, making it easier for companies to tailor products to specific customer needs without extensive retooling costs.
- Inventory Management: Reducing inventory and storage costs is a significant benefit. Parts can be produced on-demand, minimizing stockpiling of materials and components.
- Market Competitiveness: Early adoption of 3D printing technology can provide a competitive edge. Companies can innovate faster than competitors who rely on older manufacturing processes.
- Sustainability: Emphasizing cost-effectiveness through a reduction in waste aligns with growing trends toward sustainable practices in manufacturing. This can enhance a company’s reputation and attract environmentally conscious consumers.
The potential economic advantages of 3D printed titanium are compelling. As industries continue to evaluate the role of additive manufacturing in their processes, understanding the ROI from these technologies becomes critical.
The integration of 3D printing into manufacturing can transform traditional economic models, leading industries to rethink operational efficiency and financial strategies.
In summary, the economic implications of 3D printed titanium are vast, influencing decisions that range from initial investments to inventory strategies. As industries increasingly adopt this technology, its impact on overall productivity and competitiveness will only continue to grow.
Challenges in 3D Printing with Titanium
Titanium is a favored material within the realm of additive manufacturing. Its unique properties confer significant advantages, especially in sectors like aerospace and medical devices. However, despite these benefits, there are considerable challenges associated with 3D printing titanium components. Understanding these challenges is crucial for advancing technology and optimizing production processes. With heightened awareness, industries can mitigate risks while reaping the rewards of titanium's extensive capabilities.
Material Limitations
The challenges of 3D printing titanium often begin with its material limitations. Titanium, while strong, exhibits several characteristics that complicate its use in additive manufacturing. The first point to note is its high reactivity at elevated temperatures. During the melting and solidification processes, titanium can react with oxygen, nitrogen, and hydrogen in the environment. This leads to the formation of defects in the final product, such as embrittlement.
Moreover, the cost of titanium powder remains significantly high compared to other materials like aluminum or steel. This factor limits its accessibility for some manufacturers, especially those venturing into small-scale productions or prototypes. Additionally, the availability of certain titanium alloys may also restrict the range of applications, as not all alloys are suited for 3D printing processes.
The limited knowledge about optimal material parameters for various titanium alloys further creates uncertainty in the use of this metal in different applications. Potential users must conduct extensive research to understand how different properties of each alloy will react during printing.
Technical Challenges
Technical challenges present a formidable barrier when it comes to 3D printing titanium. One major issue is the high thermal gradients experienced during the printing process. These gradients can cause warping or thermal stresses in the component, leading to distortions that can affect the dimensional accuracy.
Printing speed also plays a role in the quality of the final product. Faster printing speeds may compromise the layer adhesion and, as a consequence, the overall strength of the part. Therefore, a delicate balance must be struck between speed and quality.
Post-processing is another technical hurdle that often requires significant time and resources. Elements like support structures must be removed, and surface finishing often demands precision. While these steps are critical for the final integrity and functionality of the titanium pieces, they add to the overall manufacturing timeline and costs.
Future Directions of 3D Printed Titanium
As industries evolve, the significance of future directions in 3D printed titanium becomes increasingly apparent. This section not only outlines ongoing research but also emphasizes how these advancements will impact various sectors. Understanding these trajectories is crucial for professionals looking to harness the potential of this technology.
Research and Innovations
Research into 3D printed titanium has expanded rapidly, focusing on enhancing the material properties and streamlining the printing processes. Innovations emerge continuously in areas such as:
- Enhanced Material Strength: Investigators are working on titanium alloys that offer improved strength-to-weight ratios, catering especially to aerospace and automotive applications.
- Surface Treatments: Innovative coating techniques are being explored to increase resistance to corrosion and wear, thus extending the lifespan of titanium components.
- Biocompatibility Studies: In the medical field, research seeks to improve the compatibility of titanium with biological tissues, expanding its use in prosthetics and implants.
These avenues not only promise greater performance but also broaden the application spectrum of 3D printed titanium.
Potential Market Trends
The market for 3D printed titanium is poised for growth, shaped by several key trends.
- Customization Demand: With the rise in consumer preferences for personalized products, the customizability of 3D printed titanium parts becomes a significant market driver.
- Regulatory Advancements: As standards for additively manufactured parts evolve, industries like aerospace and healthcare will likely see an increase in certified products, enhancing market trust.
- Sustainability Focus: The push for more sustainable manufacturing processes aligns with the environmental benefits of 3D printing, such as reduced material waste. This trend is anticipated to accelerate adoption across various sectors.
The confluence of these factors indicates a vibrant future landscape for 3D printed titanium, suggesting that both research and market dynamics will continue to play integral roles in shaping this field.
Finale
The exploration of 3D printed titanium reveals significant advancements that have reshaped various industries. This section aims to highlight the importance of understanding these developments and their implications.
3D printed titanium stands out due to its unique properties like high strength-to-weight ratio and resistance to corrosion, which are critical for applications in the aerospace, medical, and automotive sectors. The technology of additive manufacturing enables complex designs that were once impossible with traditional methods. In this way, the production of titanium components becomes not only more efficient but also more sustainable, reducing waste and improving performance.
Recap of Key Insights
- Material Benefits: The advantages of titanium, particularly in terms of durability and lightness, make it an exceptional choice for high-performance applications
- Manufacturing Techniques: Knowledge of processes such as Powder Bed Fusion and Directed Energy Deposition provides insight into how complex geometries are realized in titanium components.
- Application Spectrum: This technology finds applications in diverse fields including aerospace, where components must withstand extreme conditions, and in medical devices that require biocompatibility.
- Economic Assessments: Analyzing the cost structure and potential for return on investment helps industries justify the transition to 3D printed titanium.
- Future Trends: Continuous research and innovation promise expanded applications and enhanced performance characteristics in the future.
Final Thoughts on 3D Printed Titanium
The complexities involved in handling titanium through additive techniques require deep understanding and expertise. However, the potential rewards are substantial, making it a worthy consideration for researchers, engineers, and industries focused on innovation and excellence.