Exploring 3D Printing Technologies: A Comprehensive Guide
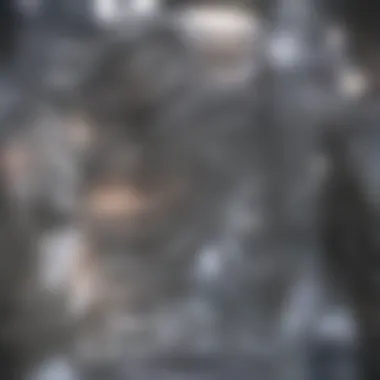
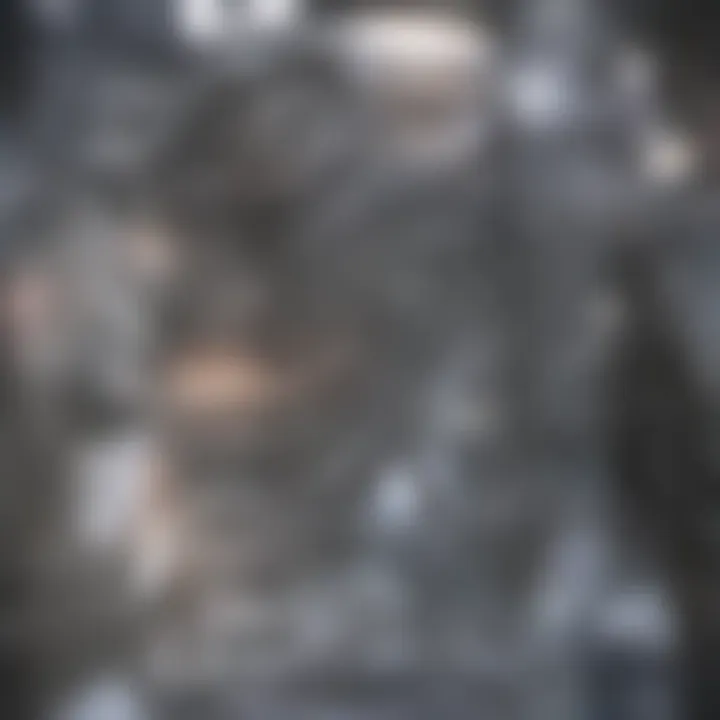
Intro
The present landscape of 3D printing technologies is vast and multifaceted. This article seeks to uncover the various methods and applications driving innovations in numerous sectors. As industries evolve, understanding 3D printing becomes essential for students, professionals, and hobbyists alike. This understanding allows for better decisions in implementing these technologies, be it in manufacturing, healthcare, or architecture.
3D printing, or additive manufacturing, serves as a powerful tool capable of producing complex shapes using a variety of materials. It enables rapid prototyping and customization, thus presenting a significant shift from traditional manufacturing. As we explore the nuances of various techniques, one must grasp the principles that underpin these technologies, their advantages, and their limitations.
"The shift from subtractive to additive manufacturing is not merely a trend; it is a revolution in how we conceive production processes."
In this comprehensive analysis, we will delve into the core principles governing each technology, assessing both their strengths and weaknesses. Moreover, we will discuss the implications of these advancements across critical fields. By synthesizing the findings of multiple studies, this examination aims to clarify the continued evolution within additive manufacturing.
Prologue to 3D Printing Technologies
The realm of 3D printing holds significant importance in today's technological landscape. It represents a fundamental shift in how products are designed, developed, and manufactured. Understanding 3D printing technologies is crucial for various stakeholders, including students, researchers, and professionals who aim to stay ahead in the rapidly evolving industries.
Key points to consider include the versatility and efficiency that these technologies offer. They enable the production of complex geometries that traditional manufacturing methods often struggle to realize. With applications spanning healthcare, aerospace, automotive, and consumer products, the potential benefits are substantial. Moreover, considerations such as cost-effectiveness, speed, and materials used can influence the choice of technology for specific applications. As the industry progresses, staying informed about these innovations becomes key to leveraging their advantages.
Definition and Overview
3D printing, also known as additive manufacturing, refers to the techniques used to create three-dimensional objects from a digital file. This process involves layering materials until the desired shape is achieved. It contrasts with traditional subtractive manufacturing methods that often remove material to create forms.
Additive manufacturing encompasses several technologies, each differing in how layers are built and the materials employed. Some of the most common methods include Fused Deposition Modelling (FDM), Stereolithography (SLA), and Selective Laser Sintering (SLS).
Overall, 3D printing represents a transformative approach to manufacturing, allowing for more flexibility in the design and production processes.
The Evolution of 3D Printing
3D printing technology has undergone significant changes since its inception in the 1980s. Initially, it was mostly limited to prototyping. At that time, industries relied primarily on traditional methods for production. However, with advancements, 3D printing has expanded into a variety of sectors.
- 1980s: The first 3D printer was created by Chuck Hull using stereolithography, which used ultraviolet light to cure liquid resin.
- 1990s: New technologies emerged, including SLS and FDM. This decade marked an expansion of materials used in 3D printing processes.
- 2000s: The development of more affordable printers led to a spike in popularity among hobbyists and manufacturers alike.
- 2010s: 3D printing began to be used in production, revolutionizing industries like healthcare with the introduction of custom implants and prosthetics.
Today, innovative practices continue to transform the landscape. Research focuses on expanding materials and ensuring quality. The future of 3D printing promises even more integration across diverse fields, enhancing efficiency and customization.
"As 3D printing technologies evolve, they continue to challenge and redefine the limits of manufacturing and design."
Fused Deposition Modeling (FDM)
Fused Deposition Modeling, often referred to as FDM, is a cornerstone technology in the realm of 3D printing. It holds significant relevance due to its accessibility and versatility in various sectors, including prototyping, product design, and even healthcare. This technique capitalizes on the principle of layer-by-layer construction, wherein thermoplastic materials are extruded through a heated nozzle. As the nozzle moves in a precise pattern, it deposits material, which cools and solidifies to form the desired object. Its importance in this article lies not only in its foundational place within additive manufacturing technologies but also in its practical applications and the advantages it offers.
Principles of FDM
FDM operates on a straightforward yet effective principle. The process begins with thermoplastic filament being fed into a heated nozzle. The temperature of the nozzle is carefully controlled to ensure the filament melts at an optimal temperature, usually around 190 to 220 degrees Celsius, depending on the material type. Once melted, the filament is extruded through the nozzle to create a thin bead of material. This bead is deposited onto a build platform.
The deposition occurs line by line, allowing for intricate designs to be formed from the bottom up. This layer-by-layer approach enables both complex geometries and fine details to be achieved. As each layer is completed, the platform lowers slightly, positioning itself for the subsequent layer. The cooling process solidifies the thermoplastic, binding each layer to the previous one. This principle encapsulates how FDM is able to produce functional prototypes and products with relative ease.
Applications of FDM in Industry
FDM's adaptability makes it suitable for numerous applications across various industries. Some prominent uses include:
- Prototyping: FDM is commonly employed for rapid prototyping, allowing designers to create physical models of their designs quickly.
- Manufacturing: It's used for producing end-use parts in industries, including automotive and aerospace.
- Healthcare: In the medical field, FDM technology helps produce custom prosthetics and anatomical models for surgical planning.
- Education: Many educational institutions utilize FDM printers to teach students about engineering and design principles.
The technologyโs ability to handle diverse materials, including PLA, ABS, and PETG, also adds to its application versatility, making it an attractive option for both small-scale and large-scale manufacturing needs.
Advantages and Disadvantages of FDM
FDM technology presents a balance of benefits and challenges that users should consider. The main advantages include:
- Cost-Effectiveness: FDM printers are often less expensive than other 3D printing technologies, making them accessible for both individuals and businesses.
- Ease of Use: The operation is relatively simple, allowing users to produce models quickly without extensive training.
- Material Options: A broad variety of thermoplastics can be used, including those that offer varying mechanical properties.
However, there are also disadvantages:
- Surface Finish: The layer-by-layer method may produce rougher surfaces compared to other technologies like SLA.
- Dimensional Accuracy: FDM may not achieve the same precision as techniques that utilize lasers or light-based curing.
- Strength Limitations: The strength of finished FDM parts can be lower than that achieved through other 3D printing methods, often depending on print settings and material choice.
"FDM stands as a gateway technology for those venturing into 3D printing, striking a balance between cost, accessibility, and versatility."
Understanding these aspects of Fused Deposition Modeling provides invaluable insight for professionals and hobbyists alike, guiding informed decisions when selecting a 3D printing method for specific projects.
Stereolithography (SLA)
Stereolithography, commonly known as SLA, is an essential technology in the realm of 3D printing. It has cemented its position as a leading method for producing highly detailed and accurate prototypes. SLA utilizes a unique mechanism that leverages light to cure liquid resin into solid structures. This article discusses its inner workings, primary applications, and the limitations faced when applying SLA in various contexts.
Mechanism of SLA
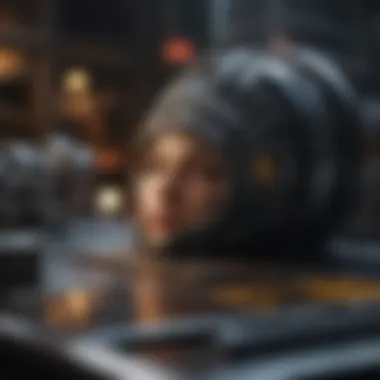
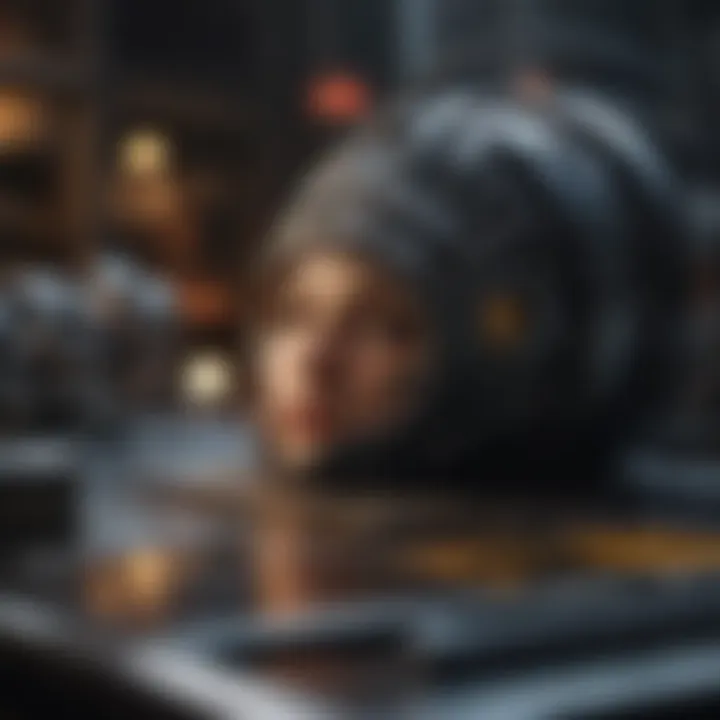
The core principle behind SLA involves a vat of photopolymer resin and a UV laser source. As the laser scans across the surface of the resin, it selectively cures sections into solid plastic. This process occurs layer by layer. Initially, a build platform lowers into the resin tank, just beneath the surface. The UV laser then traces a pre-defined pattern, solidifying a thin layer of resin. Once the first layer is complete, the platform rises slightly, allowing more resin to flow and preparing for the next layer.
A significant aspect of the SLA mechanism is the type of resin, which varies in properties such as flexibility, strength, and finish. There are specialized resins for specific applications, creating opportunities for tailored solutions. This technology excels in producing intricate designs and fine details, making it favorable in fields that demand high precision.
Common Uses of SLA
SLA is prominent in various industries for different purposes:
- Prototyping: Rapid and accurate prototyping in product design allows designers and engineers to visualize concepts early in development.
- Medical: In the medical sector, SLA is used to create dental models, surgical guides, and anatomical models.
- Jewelry: The jewelry industry benefits from SLA by creating molds for casting detailed designs, which enhances creativity and reduces production time.
- Aerospace and Automotive: Detailed components for testing aerodynamic properties or aesthetic designs are developed using SLA.
SLAโs ability to produce complex geometries and smooth surfaces makes it a preferred choice in these sectors, especially where performance and aesthetics matter.
Limitations and Challenges
Despite its advantages, SLA comes with notable limitations:
- Material limitations: The range of materials suitable for SLA is narrower compared to other 3D printing technologies. Most materials are rigid, which restricts some applications.
- Post-processing: Parts produced via SLA generally require cleaning and curing after printing, adding to time and labor costs.
- Speed: While it is faster than traditional methods, SLA can still be slower compared to other 3D printing technologies like FDM for large parts due to its layer-by-layer approach.
- Cost: Equipment costs for SLA printers remain relatively high, potentially limiting accessibility for small businesses or hobbyists.
Selective Laser Sintering (SLS)
Selective Laser Sintering is a significant player in the domain of 3D printing technologies. It stands out for its ability to process a variety of materials, including plastics, metals, and ceramics, to create highly detailed and functional parts. This method utilizes a high-powered laser to selectively fuse powdered materials into solid structures. Understanding SLS technology is essential due to its versatility and potential applications in several industries, such as aerospace, automotive, and healthcare. The exploration of SLS offers insights into modern additive manufacturing's advancement and capabilities.
Overview of SLS Technology
SLS, developed in the 1980s, is based on the principle of sintering. In this process, the laser scans the surface of a thin layer of powder, fusing it at specific points. The layer is then lowered, and a new layer of powder is applied. This cycle repeats until the part is fully formed. Temperature control is crucial throughout this process to prevent warping or uneven thermal expansion.
- Materials: Common materials used include nylon, glass-filled nylon, and various metal powders. The choice of material affects the final product's mechanical properties and appearance.
- Temperature: The laser's high temperature enables melting of the powder particles, leading to a strong bond when cooled. This aspect is vital to ensure the structural integrity of the printed parts.
SLS technology provides benefits including:
- High part accuracy
- Complex geometries that are hard to achieve with traditional methods
- No need for support structures, as the unsintered powder acts as support.
Industry Applications of SLS
The applications for SLS technology span across multiple sectors, highlighting its effectiveness in both prototyping and production. Some of the most notable applications include:
- Aerospace: Components such as brackets and housings are produced using SLS, benefiting from lightweight and strong materials which enhance performance and efficiency.
- Automotive: SLS enables rapid prototyping for parts like air intake manifolds and tooling purposes, streamlining the development process.
- Healthcare: Custom prosthetics and dental products leverage SLS technology for tailored fit and intricate designs. The ability to produce patient-specific components can improve treatment outcomes.
Comparative Analysis with Other Technologies
Selective Laser Sintering offers unique advantages when compared to other additive manufacturing processes such as Fused Deposition Modeling and Stereolithography.
- Material Range: SLS can use a broader range of materials, including high-performance polymers and metals, unlike FDM which typically relies on thermoplastics.
- Part Strength: Parts made via SLS tend to exhibit higher mechanical strength due to the sintering process. In contrast, FDM parts may have layered weaknesses.
- Complexity and Design Freedom: SLS allows for greater design freedom, enabling the creation of intricate geometries without the need for additional support.
However, there are challenges in SLS as well. The process can be slower than other methods, and initial setup costs are typically higher. Additionally, post-processing is often required to achieve desired surface finishes. This trade-off of speed versus quality is crucial for businesses to consider when choosing SLS over alternative 3D printing technologies.
"SLS technology paves the way for innovation across multiple industries, driving the development of smarter, more efficient products."
Selective Laser Sintering thus represents a pivotal technology in the realm of additive manufacturing, balancing complexity in design and functionality with the needs of modern industries.
Digital Light Processing (DLP)
Digital Light Processing (DLP) is a pivotal technology in the realm of 3D printing, notable for its precision and adaptability. This section offers a thorough examination of DLP, considering its mechanisms, advantages, and the challenges it currently faces. Understanding DLP is essential for professionals engaged in sectors that rely heavily on detailed prototyping and intricate design work, such as jewelry, dental, and engineering. The technology, distinguished by its efficiency and high resolution, positions itself as a strong contender among other printing methodologies.
What is DLP?
Digital Light Processing is based on the principle of using a digital micromirror device (DMD) to project light onto a layer of photosensitive resin, effectively curing it layer by layer. Particularly, DLP printers utilize high-resolution projectors that can cure entire layers at once, offering a speed advantage relative to other processes like Stereolithography (SLA). The light source typically used in DLP printers can be either a standard projector bulb or more advanced light sources such as LEDs, contributing to their versatility and efficiency.
Key Benefits of DLP Technology
The advantages of DLP technology are significant and impactful:
- High Resolution: DLP is known for producing finely detailed prints. The capability to work at an excellent resolution makes it suitable for creating intricate models.
- Speed: DLPโs layer-by-layer curing process allows for faster print times compared to other printing techniques. This quality can reduce overall project timelines, which is a vital factor in manufacturing and prototyping.
- Wide Range of Materials: DLP is compatible with various photosensitive resins, enabling diverse applications across different industries.
- Smooth Surfaces: Prints produced by DLP usually exhibit smooth finishes, decreasing the need for extensive post-processing.
Challenges of DLP in Practical Use
Despite its many strengths, DLP technology also faces challenges that can impact its deployment:
- Material Limitations: While there are many resins used in DLP printing, their mechanical properties can limit applications. Certain industries require materials with specific strength or flexibility characteristics that may not be available.
- Cost of Equipment and Materials: The initial investment for DLP printers and their resins can be higher than that of other techniques such as FDM. This cost factor could deter small businesses and hobbyists from adopting this technology.
- Post-Processing Needs: DLP prints often require curing and cleaning after printing, which adds further steps to the production process.
"Understanding the balance between DLP advantages and challenges can help design teams make informed decisions on the best technology for their projects."
Binder Jetting
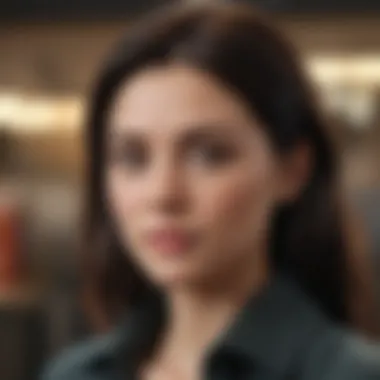
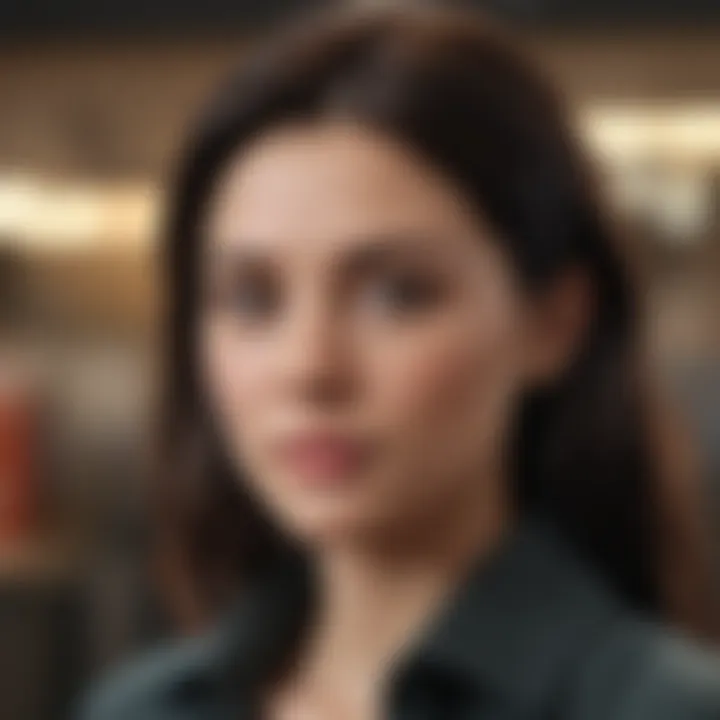
Binder jetting represents a significant advancement in 3D printing technology. It uses a unique process that involves the deposition of a binding agent onto a powder bed. Consequently, this method allows for the creation of complex geometries that would be difficult to achieve with other techniques. Furthermore, binder jetting places emphasis on speed and material diversity, making it an appealing option for various industry needs.
Understanding Binder Jetting
Binder jetting involves a few key steps. First, a layer of fine powder is spread across a build platform. Next, a print head moves across the layer, depositing a liquid binder at specific locations. This process continues layer by layer until the entire object is formed. The result is a solid object that needs further post-processing, often involving baking or infiltration with other materials. The ability to use different powders, such as metals, ceramics, and sand, enhances the versatility of this technology across numerous applications.
Applications and Innovations
The applications of binder jetting are diverse and continually evolving. For instance, it is widely used for creating prototypes in engineering and design. Additionally, it has made significant inroads into the production of final parts in industries like aerospace and automotive.
Innovations in binder jetting have also emerged, including advancements in Binder Jetting for metal parts. This allows for the production of lightweight and durable components. Moreover, the ability to print with multiple materials opens up new possibilities for functional prototypes that combine different properties in one object. Rising interest in biomedical applications demonstrates the potential of binder jetting to revolutionize fields such as custom implants and dental devices.
Material Limitations and Prospects
Despite its advantages, binder jetting has its limitations. One significant challenge is achieving the strength and durability of parts produced by this method. Post-processing steps are often required to meet strength requirements, which can add time and cost to the production process.
Moreover, the specific powders used can limit the applications. For example, some materials may not bind effectively or can lead to imperfections in the final product. Future developments may focus on overcoming these challenges by improving binder formulations or adopting innovative approaches to material selection.
Overall, binder jetting holds promise, with ongoing research aimed at enhancing its capabilities and expanding its range of materials. As technology advances, it is expected that both the performance and applicability of binder jetting will significantly increase.
"Binder Jetting's growth in application and material variation marks it as one to watch in the future of 3D printing."
Direct Metal Laser Sintering (DMLS)
Direct Metal Laser Sintering (DMLS) represents a significant advancement within the realm of 3D printing technologies, particularly in the manufacturing of metal components. Its importance lies in its ability to create complex geometries and high-performance parts directly from digital files. This method is especially relevant for industries needing both structural integrity and precision, such as aerospace, automotive, and medical sectors. By leveraging DMLS, companies can streamline production processes, reducing lead times and material waste.
Mechanics of DMLS
DMLS employs a laser to sinter powdered metal, binding the particles together layer by layer. Initially, a thin layer of metal powder is spread across the build platform. The high-powered laser then scans the cross-section of the part design, heating the powder until it reaches a temperature just below its melting point. This process causes the metal particles to fuse together. After each layer is complete, the platform lowers, and a new layer of powder is applied. This cycle repeats until the object is fully formed. The precision of this technology allows for intricate designs that may not be feasible with traditional manufacturing methods.
Sector-Specific Applications of DMLS
DMLS finds its applications in various sectors, thanks to its flexibility in metal types and complex geometries:
- Aerospace: Components like turbine blades and brackets, which require weight reduction and strength, are ideal candidates.
- Automotive: DMLS is employed for tooling, prototypes, and custom parts, allowing for lighter and more efficient vehicle designs.
- Medical: In producing surgical instruments and implants, DMLS offers design freedom and the ability to customize shapes for individual patients.
- Energy: In oil and gas industries, components that can withstand extreme conditions are produced, enhancing operational efficiency.
Strengths and Weaknesses in DMLS
Like any technology, DMLS has its strengths and weaknesses:
Strengths:
- High precision and accuracy for complex structures.
- Reduction of material waste, as it uses only the needed amount of powder.
- Capability to create lightweight parts due to design flexibility.
- Customization is practical for one-off or low-volume production runs.
Weaknesses:
- High material costs compared to traditional processes.
- Longer production times for larger builds can limit efficiency.
- Surface finish may require post-processing to achieve desired characteristics.
"DMLS has transformed the scope of manufacturing, providing an avenue for innovations that address complex industry demands."
In summary, Direct Metal Laser Sintering facilitates the manufacture of high-quality metal parts with precision and complexity in various sectors. However, while its advantages are notable, consideration of its limitations is crucial for making informed decisions in production processes.
Multi Jet Modeling (MJM)
Multi Jet Modeling is a sophisticated and versatile 3D printing technology that offers significant advantages over other methods. MJM employs a unique approach to material deposition, involving the jetting of photopolymer onto a build platform. As this technique continues to evolve, it becomes increasingly relevant for various applications in industries such as healthcare, automotive, and consumer products. Understanding MJM is crucial for anyone who wishes to engage with modern 3D printing technologies and their implications.
Principles of Multi Jet Modeling
The core principle of Multi Jet Modeling combines elements of inkjet and traditional additive manufacturing processes. This technology utilizes multiple print heads to jet layers of liquid material, usually a photopolymer, onto a platform. Once dispensed, the material is cured using ultraviolet light, resulting in hardening when exposed. This layer-by-layer approach enables high precision and accuracy in producing intricate designs with fine details. The ability to print with multiple materials simultaneously also enlarges the scope of what can be created, from rigid components to flexible parts.
Use Cases for MJM Technology
MJM technology is adaptable for several industries and applications. Some notable use cases include:
- Prototyping: Designers and engineers leverage MJM for rapid prototyping, enabling quick iterations of product designs. This is vital in keeping up with market needs.
- Medical Models: In healthcare, MJM is used to create anatomical models which help surgeons in planning complex procedures.
- Cosmetics and Jewelry: The detailed nature of MJM allows for intricate designs that are important in the cosmetics and jewelry industries.
- Functional Parts: In automotive or electronics, MJM can create parts that are both aesthetically pleasing and functional, allowing manufacturers to test and refine their products.
Comparative Analysis of MJM with Other Methods
When comparing Multi Jet Modeling to other 3D printing methods, several distinctions and advantages emerge:
- Detail and Resolution: MJM can achieve finer details compared to technologies like Fused Deposition Modeling (FDM), which may struggle with intricate designs. Additionally, MJM allows for the integration of multiple materials within a single build, while FDM generally requires separate processes.
- Speed: MJM can accelerate the production process through simultaneous material deposition. In contrast, methods such as Selective Laser Sintering (SLS) often involve longer build times due to the need for layer-by-layer sintering.
- Post-Processing Needs: MJM can require minimal post-processing compared to processes like SLS or SLA, which may leave residual materials or require significant finishing work. This characteristic makes MJM attractive for those looking to streamline production.
In summary, Multi Jet Modeling presents a significant development in the 3D printing field. Its precision, versatility, and ability to create complex structures make it a valuable technology across various sectors. As the applications continue to expand, understanding MJM becomes increasingly important for professionals and enthusiasts alike.
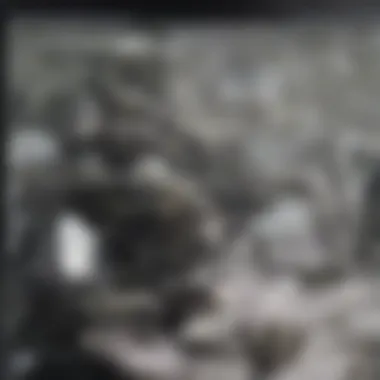
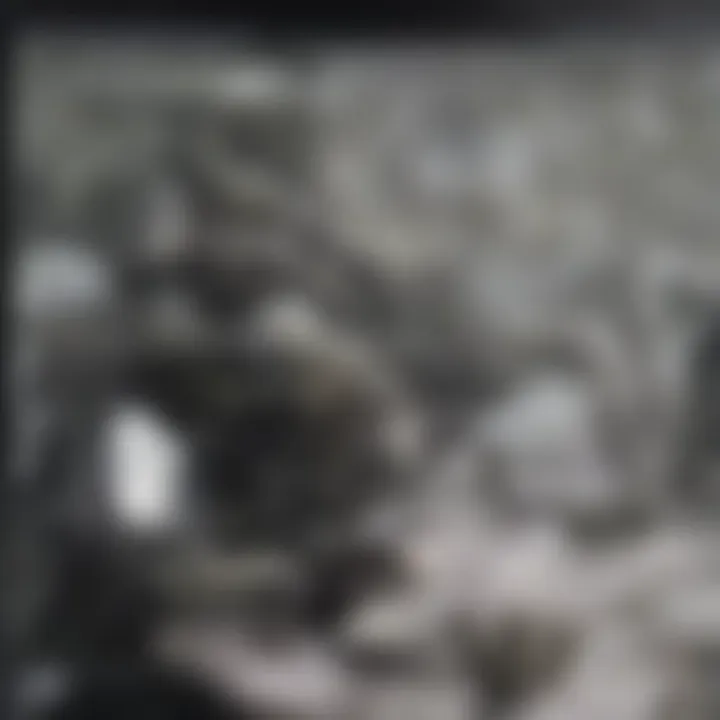
"The capability to create functional and aesthetic components using MJM shows its potential to revolutionize numerous industries."
For further reading on 3D printing technologies: Wikipedia, Britannica, Reddit, Facebook.
Material Jetting
Material Jetting is significant in the realm of 3D printing technologies due to its unique method of producing high-resolution parts with a smooth finish. This technology allows for the deposition of thousands of tiny droplets of material to form a final object. With the capacity to use multiple materials simultaneously, it provides great diversity in design applications. The ability to combine different materials for color or functional characteristics makes it highly versatile in industrial and commercial uses.
How Material Jetting Works
Material Jetting operates through the use of inkjet technology in three-dimensional space. The printer produces thin layers of photopolymer or wax-like materials. Small droplets land on the build platform in a sequential manner, building up the model layer by layer. After each layer is deposited, UV light is often used to cure the resin, solidifying it instantly. This process not only leads to solidified parts but also enhances the precision of details, which is vital for intricate designs. The layer-by-layer approach allows for complex geometries that are essential for many applications.
Applications in Various Industries
Material Jetting has found its application in multiple sectors. Some of the key industries include:
- Healthcare: Used to create patient-specific implants and prosthetics.
- Aerospace: Produces lightweight components that meet stringent regulations.
- Automotive: Rapid prototyping of models, enabling faster time-to-market.
- Consumer Products: Creates detailed models for marketing and presentation.
The capacity to use multiple materials in a single print makes it valuable for creating parts that require multiple colors, textures or characteristics.
Limitations of Material Jetting
Despite its advantages, Material Jetting comes with certain limitations. One major drawback is the cost of materials and equipment, which can be a significant investment for smaller firms or consumers. Additionally, the production speed tends to be slower compared to other methods like FDM or SLS. The dependency on relatively fragile materials can lead to challenges in durability for certain applications. Furthermore, post-processing often requires additional time and effort to achieve the desired finish and strength in parts.
"Material Jetting stands out for its precision and detail, but challenges in cost and material properties can restrict its widespread adoption."
Carbon Dioxide Laser Technology
Carbon Dioxide (CO2) laser technology plays a significant role in the sphere of 3D printing and manufacturing processes. This technology utilizes CO2 gas as the medium through which laser beams are generated. The emissions from these lasers are particularly advantageous for cutting and engraving various materials, including plastics, metals, and wood. As 3D printing technologies continue to evolve, understanding the applications, advantages, and challenges of CO2 lasers becomes crucial for industries aiming to innovate and optimize their production methods.
Prologue to CO2 Laser Technology
CO2 lasers are one of the oldest types of lasers and remain widely used due to their effectiveness. These lasers generate a beam through the excitation of CO2 gas, leading to a coherent and intense light profile. Typically, they operate with wavelengths around 10.6 microns, making them highly effective for interacting with various materials. Their functionality hinges on the conversion of electrical energy into a laser beam, facilitating efficient cutting and engraving applications.
The principle behind CO2 lasers is relatively straightforward. The laser beam is directed onto the workpiece, causing rapid heating and vaporization or melting. This precise mechanism allows for high-quality finished products while minimizing material loss. CO2 lasers are suitable for both small and large-scale projects, which makes them versatile in diverse industrial settings.
Advantages of Using CO2 Lasers
Utilizing CO2 lasers comes with numerous benefits:
- Precision: CO2 lasers provide high accuracy, allowing for intricate designs and fine detail work.
- Speed: The rapid cutting speed can significantly reduce manufacturing time.
- Material Versatility: They can cut or engrave an array of materials, making them ideal for multi-material projects.
- Cost-Efficiency: Operating a CO2 laser is often more economical than other laser types, particularly when considering the long-term operational costs.
- Quality of Cuts: The laser beam results in clean edges, reducing the need for post-processing.
These factors contribute to CO2 lasers being a preferred choice in various industries, including automotive, aerospace, and product design.
Challenges in CO2 Laser Applications
Nevertheless, using CO2 lasers is not without challenges. Some of the common drawbacks include:
- Reflectivity: Certain metals are highly reflective to CO2 lasers, which can lead to inefficient cutting or potential damage to the equipment.
- Material Limitations: Some advanced materials, particularly certain plastics and composites, may not respond well to CO2 lasers.
- Initial Setup Cost: Although operational costs are relatively low, the initial investment for high-quality CO2 laser systems can be substantial.
- Maintenance Requirements: Regular maintenance is essential to ensure consistent performance, adding to overall costs and downtime.
Understanding these challenges allows operators to make informed decisions when integrating CO2 laser technology into their production processes.
"CO2 lasers remain a cornerstone of modern manufacturing, yet they require careful consideration of both benefits and challenges to maximize their potential."
The Future of 3D Printing Technologies
The future of 3D printing technologies is a critical focus for professionals and researchers within this field. This topic carries significant weight as it sheds light on how advancements in 3D printing will influence various industries in the coming years. Understanding these predictions enables manufacturers, educators, and innovators to plan effectively for the transformations that additive manufacturing will bring.
Emerging Trends in 3D Printing
As we observe the growth of 3D printing, several trends are emerging. One notable trend is the increase in materials diversity. New materials such as bio-inks for medical applications and advanced composites for aerospace are becoming more common. The exploration of these unique materials will allow for more customized and efficient solutions across multiple sectors.
Another trend is automation and process integration. Companies are investing in software that can integrate 3D printing with other manufacturing systems. This integration improves efficiency and reduces waste. Moreover, the rise of cloud-based 3D printing services allows for distributed manufacturing, where parts can be produced on demand anywhere in the world.
Potential Impact on Industries
The potential impact of future 3D printing technologies on industries is vast. Healthcare is one area that stands to gain significantly. With bioprinting, the ability to create human tissues and organs could revolutionize transplant procedures. On the other hand, aerospace industries are expected to benefit from lighter and stronger components produced through advanced 3D printing techniques, enabling more fuel-efficient aircraft.
Furthermore, the automotive industry is already experimenting with 3D-printed components in vehicle production. This allows for rapid prototyping and customization, meeting consumer needs without lengthy manufacturing cycles.
Research and Development Directions
Research and development in 3D printing technology is expanding in various key directions. One of these directions is improving printing speed and accuracy. Fast and reliable production will make additive manufacturing a viable option for mass production.
Additionally, sustainability remains a significant focus. Efforts are underway to establish eco-friendly materials and processes to minimize environmental impact. This includes recycling methods and the development of biodegradable materials.
In summary, the future of 3D printing technologies is remarkably promising. Emerging trends signal a shift towards materials innovation, automation, and more robust integrations into existing manufacturing systems. The impact on industries will likely be transformative, and research will continuously push the boundaries of what's possible within additive manufacturing.
The advent of 3D printing presents unparalleled opportunities to reimagine manufacturing processes across sectors.